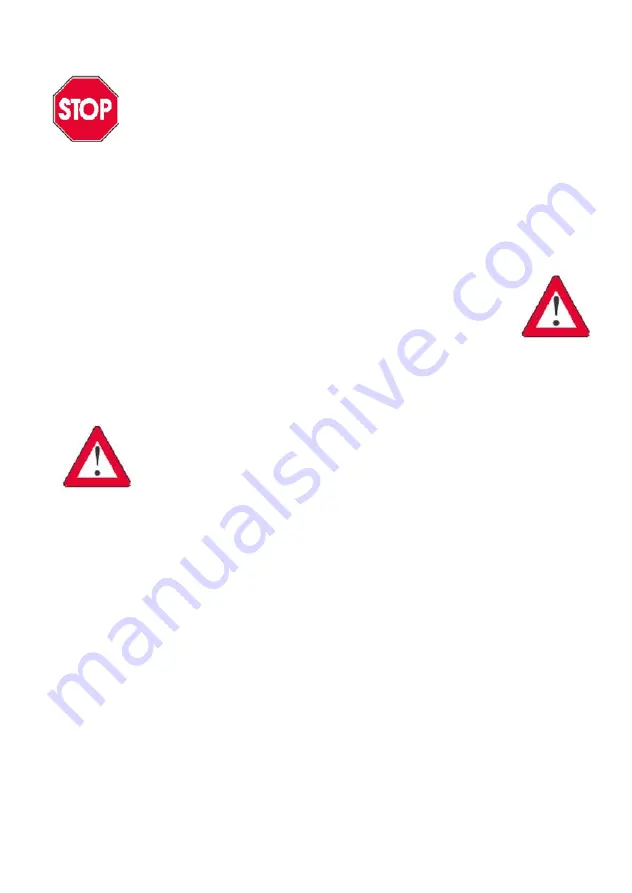
Floor Screed Machine HD 50
45
www.utiform.com
departamento.té[email protected]
Tfno. + 34 96 570 29 82 Fax: + 34 96 570 29 83
•
When draining the oil ensure that the whole circuit is emptied.
With the first oil change, change the oil filter as well. When disposing of oil, bear in mind
current regulations for eliminating contaminating substances
• If working at pressure of more than 10 bar or with oil temperatures above 100ºC, bear in mind
that the useful life of the oil diminishes
Emptying and replacement of oil
•
Stop the unit, ensure that the circuit is not pressurized and release the cap of the tank and the
lower radiator cap.
•
Remove the lower caps and drain the used oil. Check that there are no bits of metal scale or dirt.
•
Correctly tighten all the drainage caps and fill the tank to its maximum level, ensuring that you
do not exceed the limit, too much oil would produce oil overflow and the unit would not
work properly.
•
Place and tighten the filling caps.
•
Check that they are tight enough and that there are no leaks.
•
Filling the cooler is done only and automatically when the machine is running.
It is advisable to bleed the oil tank periodically to drain away water. To do so the machine must be
stopped for approximately 3 hours; following this time release the lower cap of the tank and let out the water at
the bottom. The frequency of bleeding depends largely on the working conditions (ambient temperature, relative
humidity, work load etc...). As a guide it is possible to estimate this at a frequency of about every 500 hours.
If the operation is carried out after a period of running the machine, the oil might be at a high
temperature.
Be particularly meticulous in removing any oil spilt during the oil change, so that there is no
danger of slipping or falls.
9.10.5 Motor oil change
Consult the Instruction Manual of the motor on the viscosity recommendations and the frequency of oil
change.
If in doubt, consult the UTIFORM technical service (or the motor manufacturer).
9.10.6 Motor and/or compressor aspiration filter
It is essential that during the life of the compressor and the motor, as little extraneous particles as
possible enter the machine.
Therefore, the best protection possible against wear caused by dust is to keep the filtering element of the
air aspiration in perfect condition, checking, cleaning and renewing the cartridge with a frequency which will
depend on the machine’s working conditions and environment.
The combined air system, with a cyclonic-type integrated pre-separator with a dust trap, and the filter
cartridge provides maximum degree of dust filtration (almost 100%).