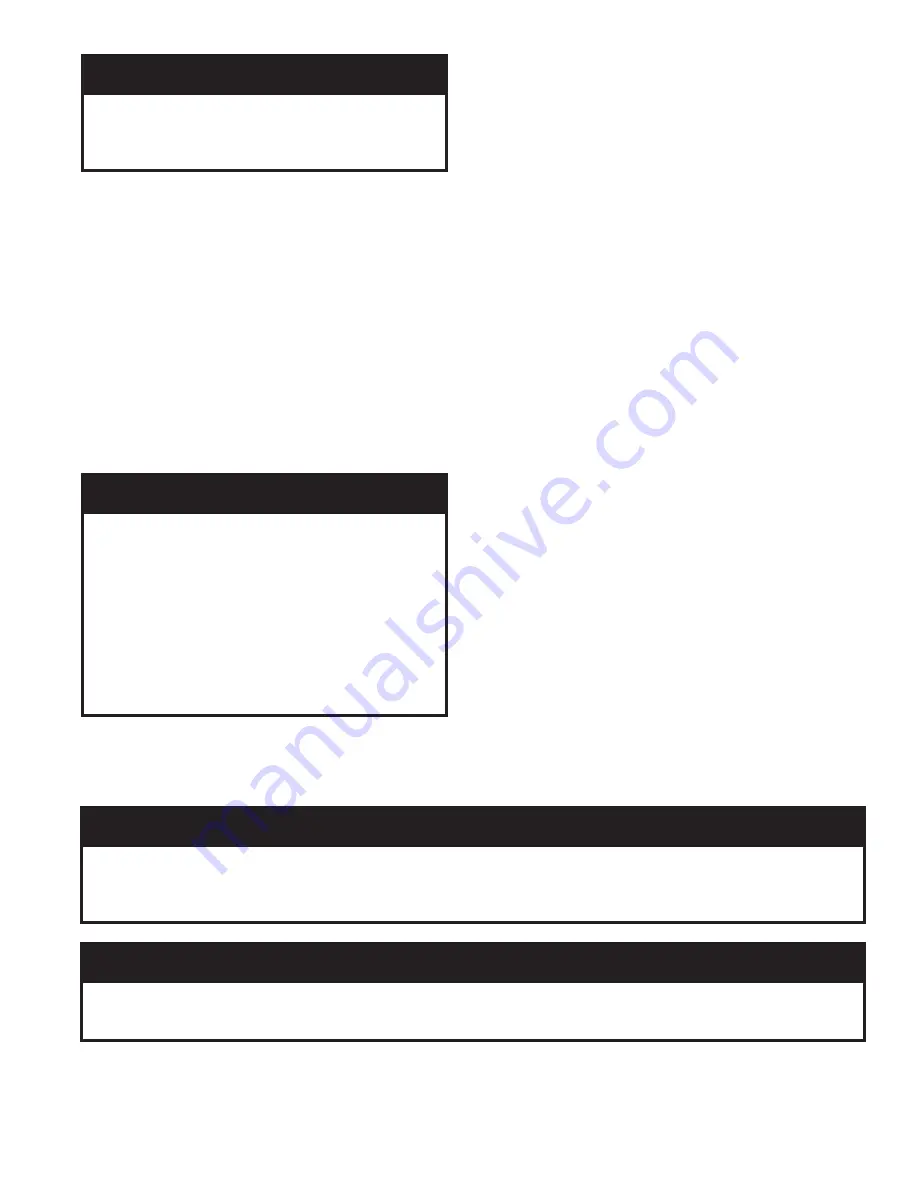
43
WARNING
Failure to properly adjust gas input rate will
result in over firing or under firing of the
appliance. Improper and unsafe boiler operation
may result.
3
.
Confirm that high and low gas pressure switches are
functioning and are adjusted to prevent over firing
or under firing of the boiler.
4
.
Adjust setting of air filter flow switch by rotating
knob on switch counter clockwise until change
filter light switch is illuminated. Turn switch knob
clockwise ¼ turn past the point where the change
filter light goes out. Replace upper front jacket
panel.
5
.
With boiler running and all panels attached,
measure oxygen (O
2
) and carbon monoxide
(CO) concentrations in the flue gas and flue gas
temperature. Compare results with values given on
factory firetest report supplied with the boiler.
DANGER
Failure to properly adjust excess air will result
in unsafe levels of carbon monoxide. Variations
in venting or combustion air pressure and
temperature will change excess air. Adjust
excess air levels so that variation in venting
or combustion air pressures and temperatures
caused by change of seasons, wind conditions,
opening or closing of boiler room doors or
windows do not cause the boiler to operate with
carbon monoxide concentrations above 400
parts per million.
6
.
Verify that all safety and operating limits and flame
controls are operating properly. These controls
and limits include combustion air switch, water
temperature operating control, manual reset water
temperature safety limit, vestibule fuseable link,
mixer fuseable link, high and low gas pressure
switches. Refer to manuals for these components for
proper start-up and operating instructions. Follow
all instructions contained in these manuals. This
manual was provided with the boiler.
J.
Finish Commissioning at the Boiler
- Reconnect any
wires from the external control system, if applicable.
1. Test function of external control system.
2
.
Place system control back in normal operation, if
necessary.
K.
Water Treatment
- Contact reputable chemical
treatment company for recommendations on proper
water treatment for the installation. Each installation
is different and must be analyzed based on local water
conditions and boiler operating schedule.
The treatment chemicals must be compatible with
copper, bronze, steel and cast iron materials of
construction.
CAUTION
A proper water treatment and monitoring program will extend the life of the boiler. The water shall have
a maximum water hardness of 8.5 grains or 150 ppm. The recommended pH range is 8.8 to 9.2. However,
other aspects of water quality can affect boiler operation and longevity. A qualified water treatment expert
should be consulted to develop a complete water treatment plan.
WARNING
Chemicals used in treating boiler water are toxic and/or harmful. Always use protective clothing and
equipment when working with/near chemicals. Contact local authorities to determine if treated boiler water
can be discharged into local waste water system.
Содержание EVCA SERIES
Страница 13: ...13 Figure 3 Typical Sidewall Pressurized Venting Optional Figure 2 Typical Sidewall Pressurized Venting ...
Страница 14: ...14 Figure 4 Typical Vertical Pressurized Venting ...
Страница 16: ...16 Figure 6 Vertical Air Intake Piping Figure 5 Horizontal Air Intake Piping ...
Страница 19: ...19 Figure 8 Schematic Boiler Piping ...
Страница 25: ...25 Figure 9a 208 230 480V 1PH 3PH 60HZ Supply Power Wiring Schematic ...
Страница 26: ...26 Figure 9b 120V 1PH 60HZ Supply Power Wiring Schematic ...
Страница 27: ...27 Figure 9c Control Wiring Schematic EVCA 750 2000 ...
Страница 29: ...29 Figure 9e Control Wiring Schematic EVCA 3000 ...
Страница 32: ...32 Figure 10 Modular System Horizontal Air Intake Piping ...
Страница 33: ...33 Figure 11 Modular System Vertical Air Intake Piping ...
Страница 34: ...34 Figure 12 Modular System Typical One Pipe Water Piping ...
Страница 35: ...35 Figure 13 Modular System Typical Primary Secondary Water Piping ...
Страница 36: ...36 Figure 14 Modular System Typical Primary Secondary without System Pump ...
Страница 37: ...37 Figure 15 Modular System Typical Reverse Return Water Piping ...
Страница 38: ...38 Figure 16 Modular System Reverse Return with System Pump Only ...
Страница 39: ...39 Figure 17 Modular System Typical Primary Secondary with Reverse Return ...
Страница 55: ...55 Figure 18 Cleaning Secondary Heat Exchanger 1 2 ...
Страница 56: ...56 This page intentionally left blank ...
Страница 58: ...58 Figure 19 Boiler Combustion Chamber ...
Страница 60: ...60 Figure 20 Burner Assembly FRONT VIEW TOP VIEW ...
Страница 62: ...62 Figure 21a UL FM CSD 1 Main Gas Train Assembly EVCA 750 2000 ...
Страница 64: ...64 Figure 21b UL FM CSD 1 Main Gas Train Assembly EVCA 3000 ...
Страница 66: ...66 Figure 22a DB B Gas Train 750 Figure 22b DB B Gas Train 1000 2000 ...
Страница 68: ...68 Figure 22c DB B w POC Gas Train 750 Figure 22d DB B w POC Gas Train 1000 2000 ...
Страница 70: ...70 Figure 22e DB B Gas Train EVCA 3000 Figure 22f DB B w POC Gas Train EVCA 3000 ...
Страница 72: ...72 Figure 23 Jacket ...
Страница 74: ...74 Figure 24 EVCA 750 1000 and 1500 Secondary Heat Exchanger and Housing ...
Страница 78: ...78 Figure 25b EVCA 3000 Secondary Heat Exchanger and Housing ...
Страница 80: ...80 Figure 26 Control Panel Assembly ...
Страница 82: ...82 Figure 27 Bishop Pilot Assembly ...
Страница 97: ...97 NOTES ...
Страница 98: ...98 NOTES ...
Страница 99: ...99 NOTES ...