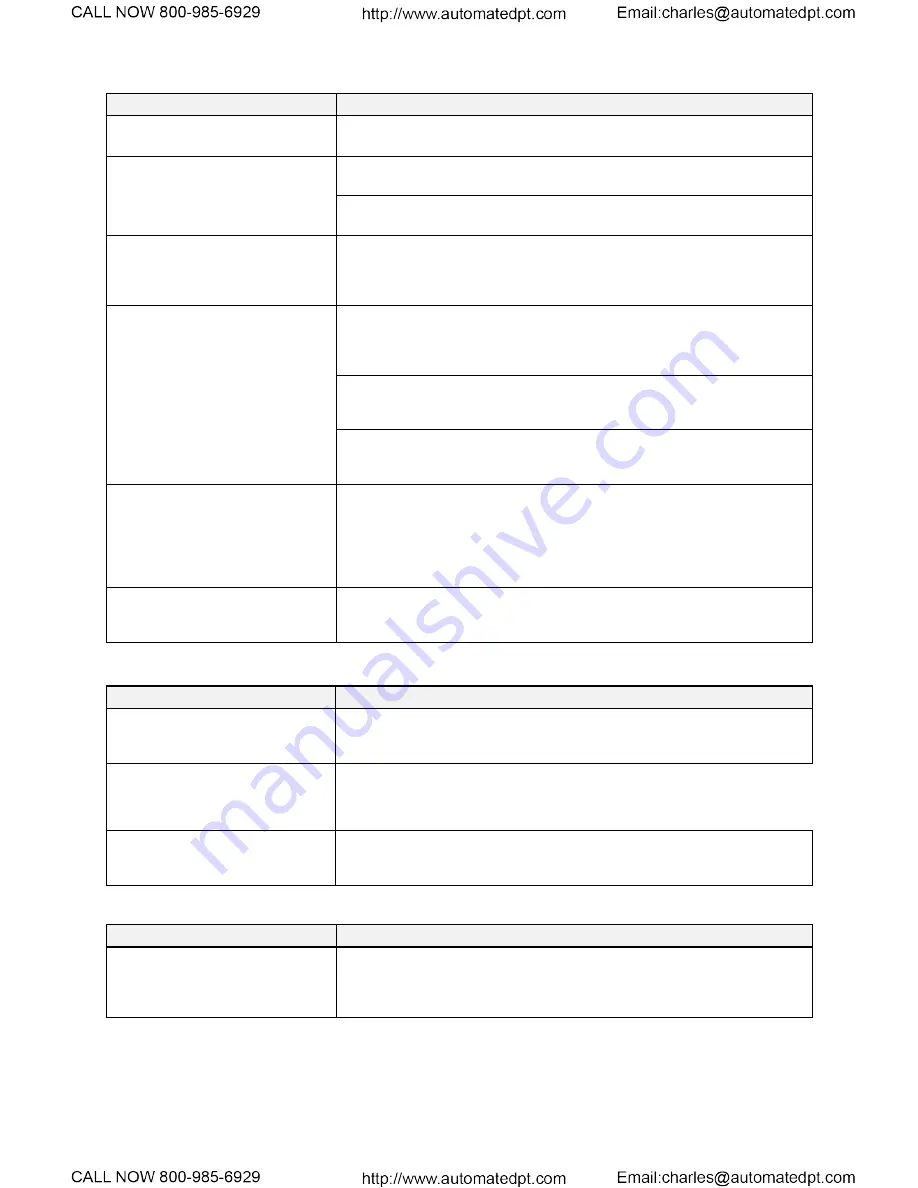
10-7
Possible Causes
What to Check and Suggested Measures
(5) The acceleration time was too
long or too short.
Check the data of function codes F07, E10, E12, and E14 (Acceleration time).
Change the acceleration time to match the load.
(6) Overload.
Measure the output current.
Reduce the load.
Check whether any mechanical brake is activated.
Release the mechanical brake.
(7) Function code settings do not
agree with the motor
characteristics.
If auto-torque boost or auto-energy saving operation is specified, check
whether the data of P02*, P03*, P06*, P07*, and P08* agree with the
parameters of the motor.
Perform auto-tuning of the inverter for the motor to be used.
(8) The output frequency does not
increase due to the current
limiter operation.
Make sure that F43 (Current limiter (Mode selection)) is set to "2" and check
the data of F44 (Current limiter (Level)).
Correct the F44 data. Or, if the current limiter operation is not needed, set
F43 to "0" (disabled).
Decrease the value of torque boost (F09*), then run the motor again and
check if the speed increases.
Adjust the value of the torque boost (F09*).
Check the data of function codes F04*, F05*, H50, H51, H52, H53, H65, and
H66 to ensure that the V/f pattern setting is right.
Match the V/f pattern setting with the motor ratings.
(9) The output frequency does not
increase due to the torque limiter
operation.
Check whether data of torque limiter related function codes (F40, F41, E16
and E17) is correctly configured and the "Select torque limiter level" terminal
command
TL2
/
TL1
is correct.
Correct data of F40, F41, E16 and E17 or reset them to the factory
defaults (disable).
Set the
TL2
/
TL1
correctly.
(10) Bias and gain incorrectly
specified.
Check the data of function codes F18, C50, C32, C34, C37, C39, C42, and
C44.
Readjust the bias and gain to appropriate values.
[ 3 ] The motor runs in the opposite direction to the command.
Possible Causes
What to Check and Suggested Measures
(1) Wiring to the motor is incorrect. Check the wiring to the motor.
Connect terminals U, V, and W of the inverter to the U, V, and W terminals
of the motor, respectively.
(2) Incorrect connection and
settings for run commands and
rotation direction commands
FWD
and
REV
.
Check the data of function codes E98 and E99 and the connection to
terminals [FWD] and [REV].
Correct the data of the function codes and the connection.
(3) The rotation direction
specification of the motor is
opposite to that of the inverter.
The rotation direction of IEC-compliant motors is opposite to that of
incompliant motors.
Switch the
FWD
/
REV
signal setting.
[ 4 ] Speed fluctuation or current oscillation (e.g., hunting) occurs during running at constant speed.
Possible Causes
What to Check and Suggested Measures
(1) The frequency command
fluctuates.
Check the signals for the frequency command with Menu #4 "I/O Checking"
using the keypad.
Increase the filter constants (C33, C38, and C43) for the frequency
command.
Содержание EQ7 Series
Страница 1: ......
Страница 29: ...2 6 Unit inch mm Refer to Section 2 3 3 9 ...
Страница 94: ...4 25 Table B Motor Parameters Continued Three phase 460 V series EQ7 4_ _ _ C ...
Страница 152: ...4 83 Examples of Sequence Circuits 1 Standard sequence 2 Sequence with an emergency switching function ...