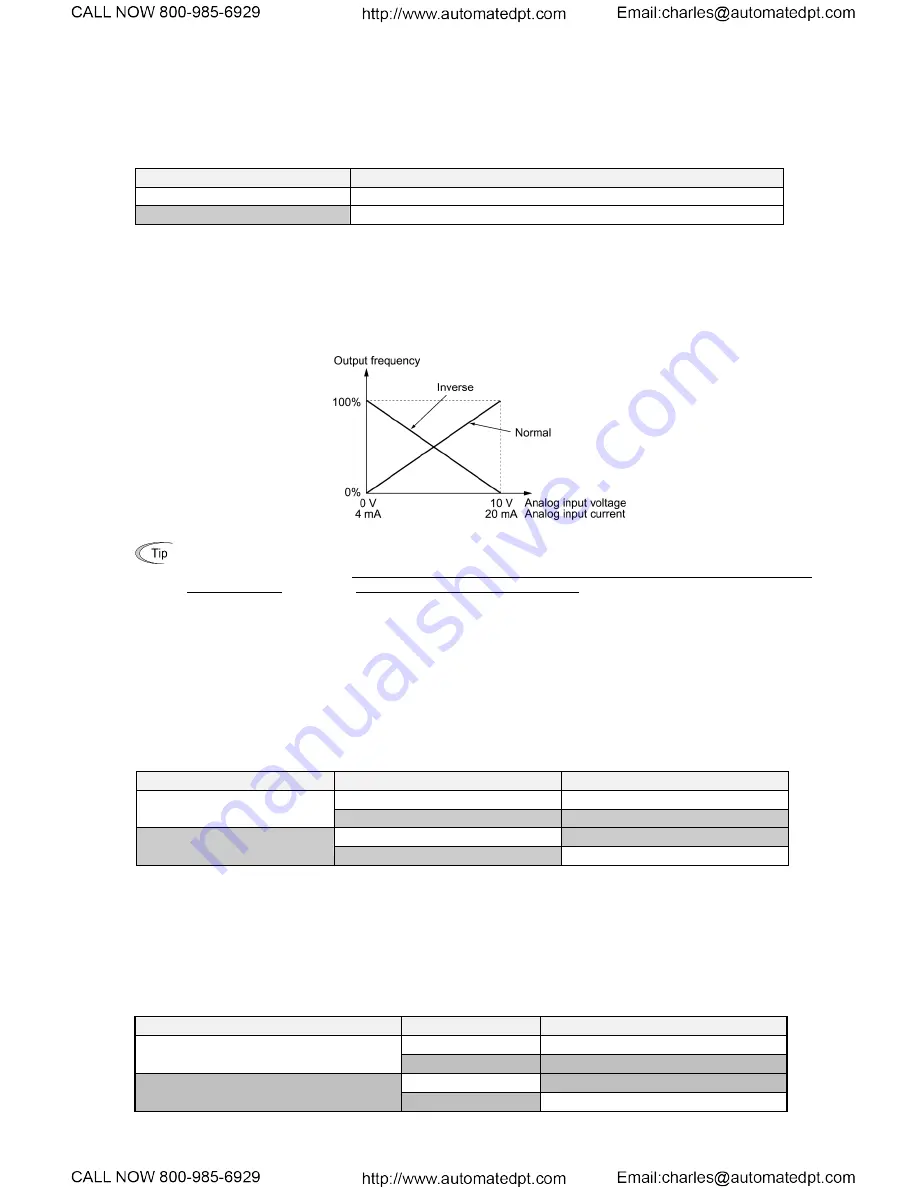
4-78
Cancel PID control --
Hz/PID
(Function code data = 20)
Turning this terminal command ON disables the PID control.
If the PID control is disabled with this command, the inverter runs the motor with the reference frequency manually
set by any of the multi-frequency, keypad, analog input, etc.
Terminal command
Hz/PID
Function
OFF
Enable PID control
ON
Disable PID control/Enable manual frequency settings
(
Refer to the descriptions of J01 through J19 and J56 through J62.)
Switch normal/inverse operation --
IVS
(Function code data = 21)
This terminal command switches the output frequency control between normal (proportional to the input value)
and inverse in analog frequency setting or under PID process control. To select the inverse operation, turn the
IVS
ON.
The normal/inverse switching operation is useful for air-handling that require switching between cooling
and heating. In cooling, the speed of the fan motor (output frequency of the inverter) is increased to lower
the temperature. In heating, it is reduced to lower the temperature. This switching is realized by this
IVS
terminal command.
• When the inverter is driven by an external analog frequency command sources (terminals [12], [C1] and
[V2]):
Switching normal/inverse operation can apply only to the analog frequency command sources (terminals [12], [C1]
and [V2]) in frequency command 1 (F01) and does not affect frequency command 2 (C30) or UP/DOWN control.
As listed below, the combination of the "Selection of normal/inverse operation for frequency command 1" (C53)
and the IVS terminal command determines the final operation.
Combination of C53 and
IVS
Data for C53
IVS
Final operation
0: Normal operation
OFF
Normal
ON
Inverse
1: Inverse operation
OFF
Inverse
ON
Normal
• When the process control is performed by the PID processor integrated in the inverter:
The terminal command
Hz
/
PID
("Cancel PID control") can switch the PID control between enabled (process is to
be controlled by the PID processor) and disabled (process is to be controlled by the manual frequency setting). In
either case, the combination of the "PID control" (J01) or "Selection of normal/inverse operation for frequency
command 1" (C53) and the terminal command
IVS
determines the final operation as listed below.
When the PID control is enabled:
The normal/inverse operation selection for the PID processor output (reference frequency) is as follows.
PID control (Mode selection) (J01)
IVS
Final operation
1: Enable (normal operation)
OFF
Normal
ON
Inverse
2: Enable (inverse operation)
OFF
Inverse
ON
Normal
Содержание EQ7 Series
Страница 1: ......
Страница 29: ...2 6 Unit inch mm Refer to Section 2 3 3 9 ...
Страница 94: ...4 25 Table B Motor Parameters Continued Three phase 460 V series EQ7 4_ _ _ C ...
Страница 152: ...4 83 Examples of Sequence Circuits 1 Standard sequence 2 Sequence with an emergency switching function ...