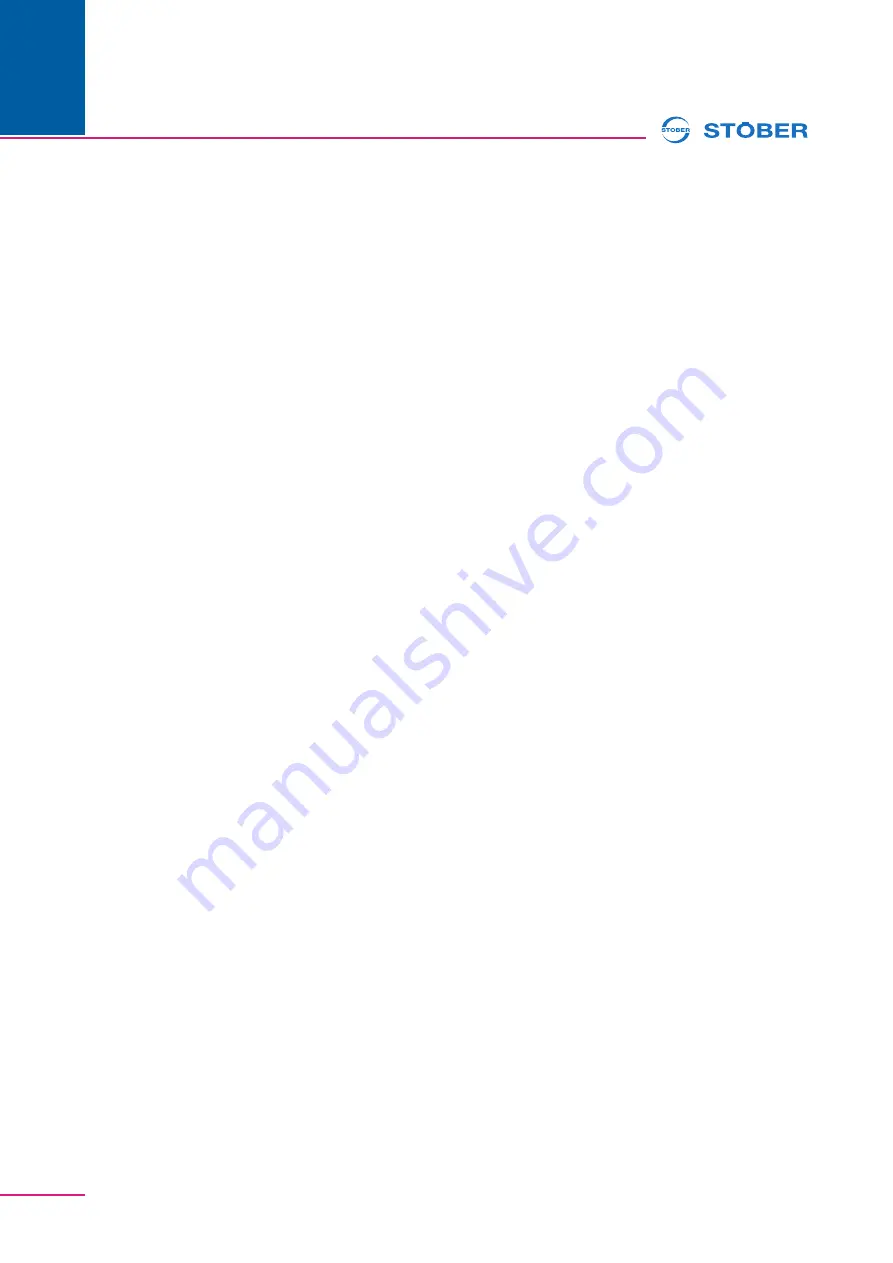
Integrated Bus
ID 442289.06
122
Operation manual POSIDYN® SDS 5000
11
WE
KEEP
THINGS
MOVING
3. Payment
3.1. The payment shall be dictated by the order confirmation. Should the Parties agree on payment
according to outlay, the outlay shall be shown in the invoice or in a separate annex to the invoice.
Should the Customer not contradict the evidenced outlay in writing within two weeks, the Customer
shall bear the burden of proof for the incorrectness of the outlay. Additional services requested by
the Customer shall be invoiced on the basis of the STÖBER ANTRIEBSTECHNIK price list. In the
absence of any other written agreement, the prices in the latest STÖBER ANTRIEBSTECHNIK
price list shall apply, according to which services are invoiced according to person-days and hours
plus the expenses incurred.
3.2. In the event of an unjustified notification of defects, STÖBER ANTRIEBSTECHNIK can invoice the
Customer for the time taken for the troubleshooting on the basis of the current price list, in particular
if the Customer reports a fault that cannot be demonstrable or reproducible, or if the fault is not
attributable to STÖBER ANTRIEBSTECHNIK.
4. Rights to Software
4.1. All intellectual property rights to the software supplied to the Customer and to the work results,
including the documentation (e.g. copyrights, trademark rights, technical property rights), in the
relationship with the Customer shall be due to STÖBER ANTRIEBSTECHNIK, even if and insofar
as the work results are obtained on the basis of the specifications from or in cooperation with the
Customer. STÖBER ANTRIEBSTECHNIK grants the Customer a simple, non-exclusive right of use
to the software supplied. The Customer shall only be entitled to use the software for its own
purposes in conjunction with the 5
th
inverter generation.
4.2. The Customer may make the requisite number of backup copies of the software, all of which,
however, must bear the STÖBER ANTRIEBSTECHNIK copyright mark and subsequently be kept
safely. The Customer may decompile the software and parts thereof (such as interface information)
only within the limitation of § 69e German Copyright Act (UrhG) and only when this intention is
notified to STÖBER ANTRIEBSTECHNIK in writing with a reasonable period of notice for provision
of the necessary information. Information on the source code shall thereby be subject to the strictest
confidentiality, irrespective of whether it was provided by STÖBER ANTRIEBSTECHNIK or a third
party or became known during the course of decompilation. Furthermore, modifications to and
editing of the software (modification, reverse engineering, decoding, translation, etc.) shall require
the prior written authorization of STÖBER ANTRIEBSTECHNIK.
4.3. If the software was supplied to the Customer electronically, any passing on of the software by the
Customer to third parties - whether or not against payment - shall not be permitted without the prior
written authorization of STÖBER ANTRIEBSTECHNIK.
4.4. STÖBER ANTRIEBSTECHNIK grants the rights of use to the software initially only revocably
subject to a condition precedent of complete remuneration or payment and can, in the event of a
delay in payment and after fruitless expiry of a reasonable grace period, revoke the granting of the
rights of use to the extent to which no remuneration or payment has been received.