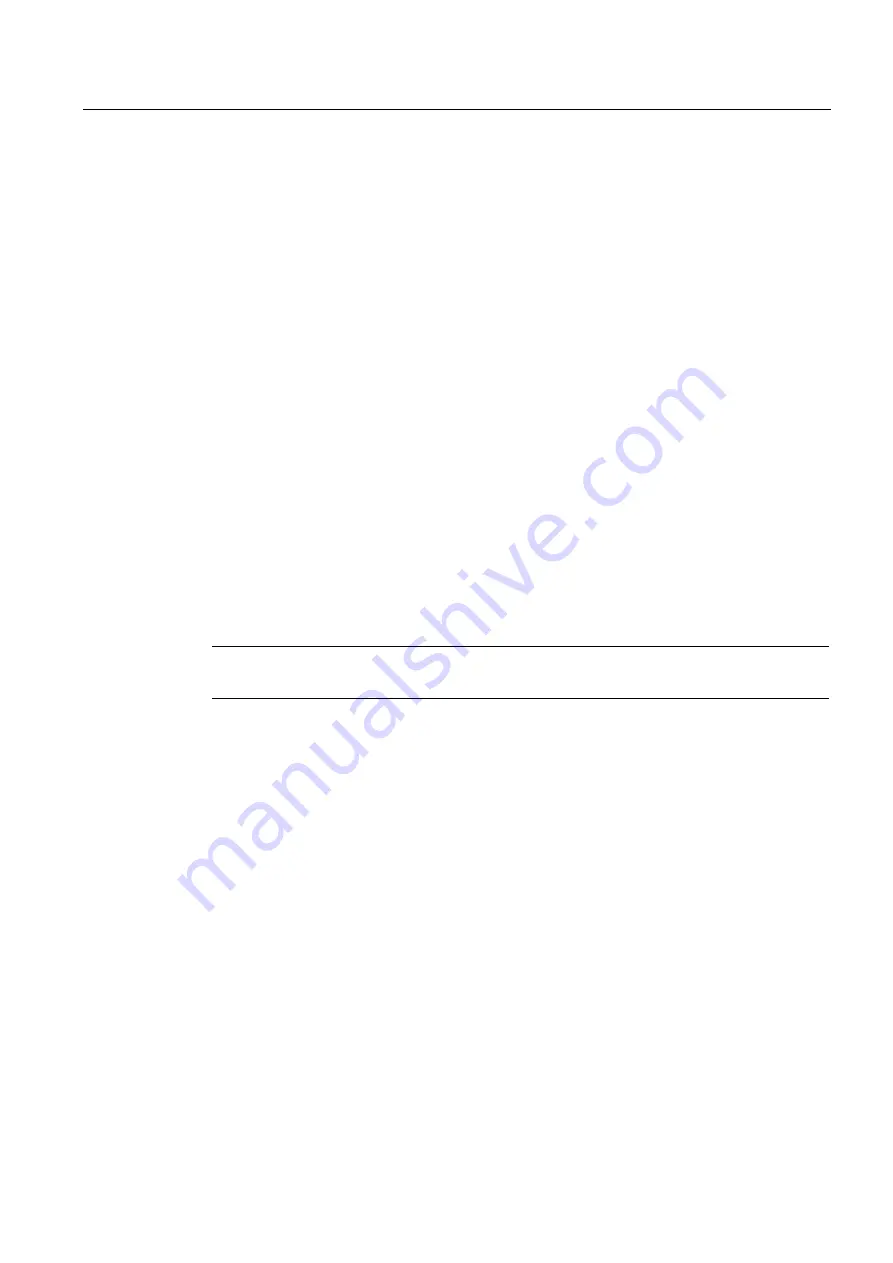
Functions, monitoring, and protective functions
9.4 Extended functions
Drive converter cabinet units
Operating Instructions, 07/07, A5E00288214A
373
9.4.6.3
Referencing
Description
Once a machine has been switched on, the absolute dimensional reference to the machine’s
zero point must be established for positioning purposes. This procedure is referred to as
homing.
The following types of homing are available:
●
Setting reference point (all encoder types)
●
Active homing (reference point approach (p2597 = 0), with incremental encoder):
–
Homing cam and encoder zero mark (p2607 = 1)
–
Encoder zero mark (p0495 = 0)
–
External zero mark (p0495 ≠ 0)
●
Flying referencing (passive (p2597 = 1), with incremental encoder)
●
Absolute encoder adjustment (with absolute value encoder)
●
Flying referencing (passive (p2597 = 1), with absolute value encoder)
A connector input is provided for the specification of reference point coordinates for all types
of homing. This allows e.g. for modification/specification by means of higher-level control. A
setting parameter for this variable is however needed for the fixed specification of reference
point coordinates. This setting parameter p2599 is connected to connector input p2598 as
standard.
Note
Homing of distance-coded zero marks is not supported.
Set reference point
The reference point can be set by a 0/1 edge on binector input p2596 (set reference point) if
no other traversing block is active or has been interrupted by an interim stop. The current
actual position of the drive is set here as the reference point using the coordinates specified
by connector input p2598 (reference point coordinates). The setpoint (r2665) is adjusted
accordingly.
This function also uses actual position value correction for the position controller (p2512 and
p2513). Connector input p2598 is connected to setting parameter p2599 as standard. The
binector input is not effective for the traversing task being presently executed.
Absolute encoder adjustment
Absolute value encoders have to be adjusted during commissioning. Once the machine has
been switched off, the encoder’s position information is retained.
With the aid of the reference point coordinates in p2599 and by entering p2507 = 2, an offset
value (p2525) is calculated and is then used to calculate the actual position value (r2521).
Parameter p2507 reports calibration using a "3". Bit r2684.11 (reference point set) is also set
to "1".
Содержание SINAMICS S150
Страница 2: ......
Страница 6: ...Preface Drive converter cabinet units 6 Operating Instructions 07 07 A5E00288214A ...
Страница 14: ...Table of contents Drive converter cabinet units 14 Operating Instructions 07 07 A5E00288214A ...
Страница 28: ...Device overview 2 5 Type plate Drive converter cabinet units 28 Operating Instructions 07 07 A5E00288214A ...
Страница 519: ......
Страница 520: ...Siemens AG Automation and Drives Large Drives P O Box 4743 90025 NÜRNBERG GERMANY www ad siemens com A5E00288214A ...