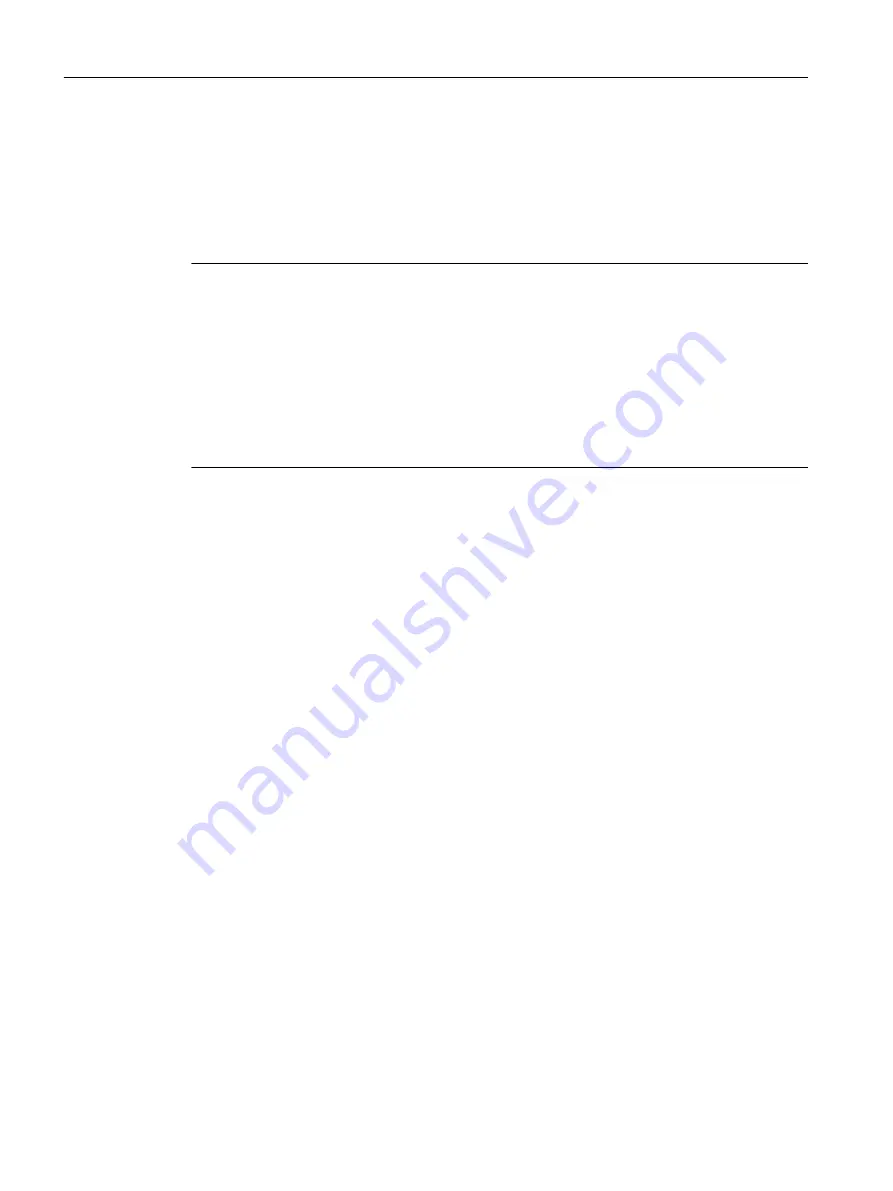
Advanced settings
If you with to suppress the automatic restart function for certain faults, then you must enter the
appropriate fault numbers in p1206[0 … 9].
Example: p1206[0] = 07331 ⇒ No restart for fault F07331.
Suppressing the automatic restart only functions for the setting p1210 = 6, 16 or 26.
Note
Motor starts in spite of an OFF command via the fieldbus
The inverter responds with a fault if fieldbus communication is interrupted. For one of the
settings p1210 = 6, 16 or 26, the inverter automatically acknowledges the fault and the motor
restarts, even if the higher-level control attempts to send an OFF command to the inverter.
● In order to prevent the motor automatically starting when the fieldbus communication fails,
you must enter the fault number of the communication error in parameter p1206.
Example for PROFINET:
Fault number F08501 means: Communication failure.
Set p1206[n] = 8501 (n = 0 … 9).
Advanced commissioning
6.27 Automatic restart
SINAMICS G120C converter
308
Operating Instructions, 09/2017, FW V4.7 SP9, A5E34263257B AF
Содержание SINAMICS G120C
Страница 2: ......
Страница 14: ...Table of contents SINAMICS G120C converter 14 Operating Instructions 09 2017 FW V4 7 SP9 A5E34263257B AF ...
Страница 469: ......