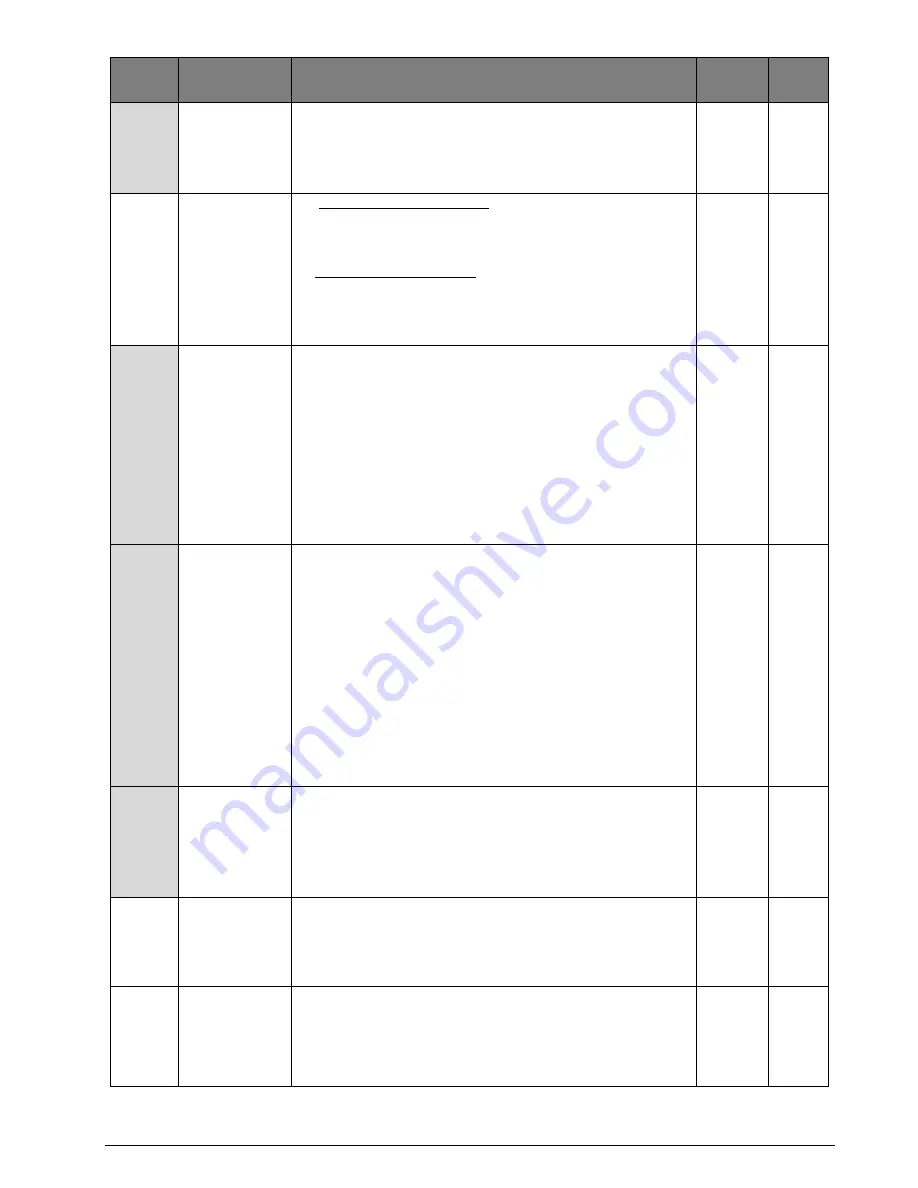
Function Parameters
71
-
144
Function
code
Name
Detailed instruction of parameters
Default
value
Modify
Note:
The reference channel and the feedback channel can
not coincide, otherwise, PID can not control effectively.
P09.03
PID output
feature selection
0
:
PID output is positive
. When the feedback signal
exceeds the PID reference value, the output frequency of
the inverter will decrease to balance the PID. For example,
the strain PID control during wrapup
1: PID output is negative.
When the feedback signal is
stronger than the PID reference value, the output frequency
of the inverter will increase to balance the PID. For
example, the strain PID control during wrapdown
0
○
P09.04
Proportional
gain (Kp)
The function is applied to the proportional gain P of PID
input. P determines the strength of the whole PID adjuster.
The parameter of 100 means that when the offset of PID
feedback and reference value is 100%, the adjusting range
of PID adjustor is the Max. Frequency (ignoring integral
function and differential function).
Higher value can reach the target control value faster, but it
may cause oscillation
The setting range: 0.00~100.00
1.00
○
P09.05 Integral time (Ti)
This parameter determines the speed of PID adjustor to
carry out integral adjustment on the deviation of PID
feedback and reference. When the deviation of PID
feedback and reference is 100%, the integral adjustor
works continuously after the time (ignoring the proportional
effect and differential effect) to achieve the Max. Frequency
(P00.03) or the Max. Voltage (P04.31). Shorter the integral
time, stronger is the adjustment. If the value is reduced,
response will be faster but setting too low may lead to
controller oscillation.
Setting range: 0.00~10.00s
0.10 s
○
P09.06
Differential time
(Td)
Set the output value to the variation of the error. If
differential time is set to 0.01 s and the percentage variation
of error per 1s is 100%, 1% per 10 ms is output.
Setting range: 0.00~10.00s
0. 00 s
○
P09.07
Sampling cycle
(T)
This parameter means the sampling cycle of the feedback.
The modulator calculates in each sampling cycle. The
longer the sapling cycle is, the slower the response is.
Setting range: 0.001~10.000s
0.100 s
○
P09.08
PID control
deviation limit
The output of PID system is relative to the maximum deviation of
the close loop reference. As shown in the diagram below, PID
adjustor stops to work during the deviation limit. Set the function
properly to adjust the accuracy and stability of the system.
0.0 %
○
Содержание CV50-008-4F
Страница 1: ...USER MANUAL INVERTER CONTROLVIT CV50 ...
Страница 2: ......
Страница 84: ...84 144 Function Parameters ...
Страница 101: ...Fault Tracking 101 144 8 6 4 Undervoltage fault 8 6 5 Abnormal motor heat ...
Страница 102: ...102 144 Fault Tracking 8 6 6 Inverter overheating 8 6 7 Stall during the acceleration of the motor ...
Страница 131: ...Dimension Drawings Appendix B 131 144 18 5 30kW flange mounting 37 110kW flange mounting 132 200kW flange mounting ...
Страница 142: ... ...
Страница 143: ... ...