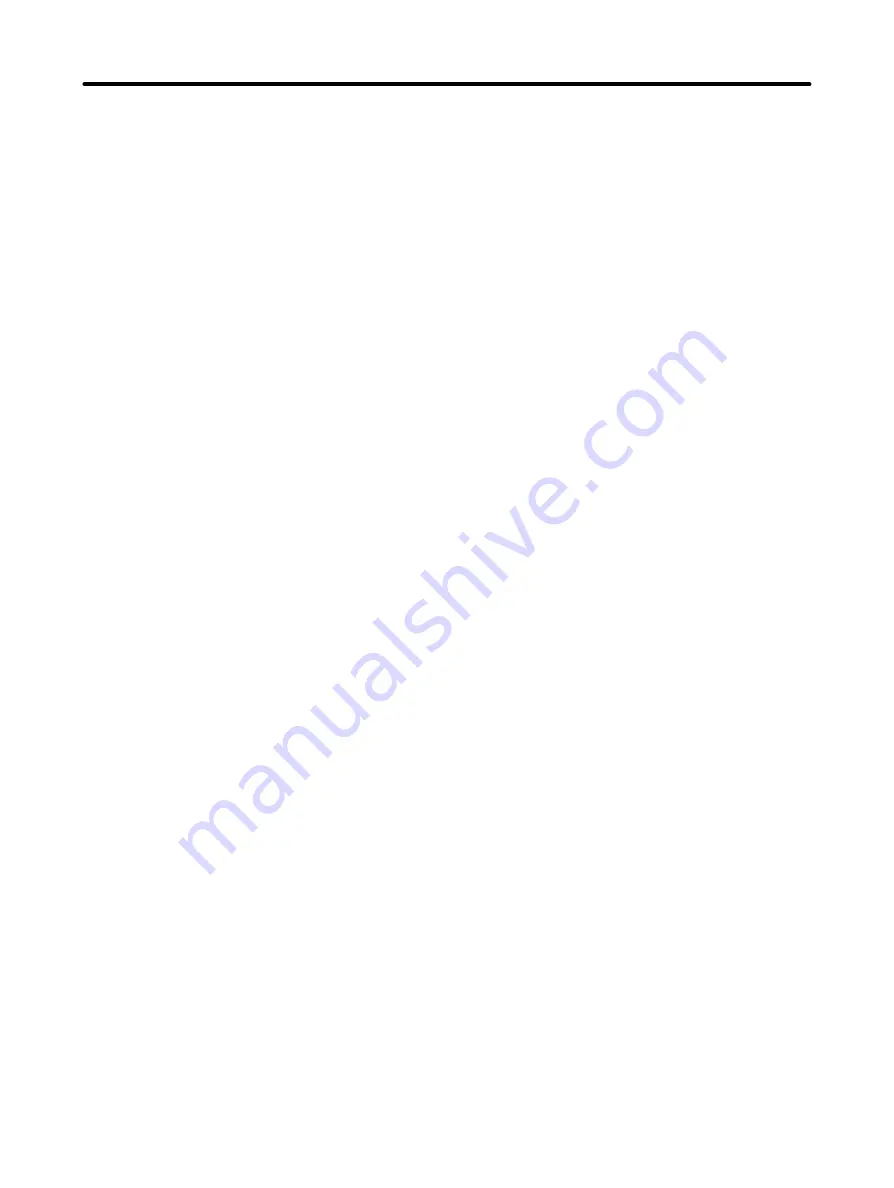
5-25
If the run command turns off , a servo error occurs, or the main-circuit power supply turns off during
operation of a Servomotor with a brake, the dynamic brake comes on (setup parameter Cn-01 bit no. 6 =
0) and Servomotor rotation speed is decreased. When the speed drops to the level of the value set for
the brake command speed (Cn-15), the brake interlock output (BKIR: CN1-7) turns OFF.
Even if the speed does not drop to the level of the value set for the brake command speed (Cn-15), the
brake interlock output (BKIR: CN1-7) turns OFF after the time set for brake timing 2 has elapsed. (This
time setting is made for the purpose of preventing damage to machinery or the Servomotor holding
brake.)
D
Torque Command Filter Time Constant: Cn-17
This sets the low-pass filter time constant for the torque command. The setting range is 0 to 250 (
×
100
µ
s), and the factory setting is 4 (
×
100
µ
s).
The relationship between the filter time constant and the cut-off frequency can be found by means of the
following formula:
fc (Hz) = 1 / (2
πΤ
)
:
Τ
= Filter time constant
If
Τ
= 400 (
µ
s), fc will be approximately 400 (Hz).
When the characteristic vibration of the machinery is within the response frequency of the servo loop,
Servomotor vibration will occur. In order to prevent this sympathetic vibration based on the characteris-
tic vibration of the machinery, set the torque filter time constant to a value that will eliminate the vibration
(i.e., set it to a high value).
D
Forward Rotation External Current Limit: Cn-18
Reverse Rotation External Current Limit: Cn-19
These set the Servomotor output torque limits for the forward and reverse directions. They are valid
when the forward/reverse current limits (PCL/NCL CN1-11/12) are input. This function can’t be used if
the input command mode is set to “internal speed control settings.” The setting range is 0 to the maxi-
mum torque, and the factory setting is for the 100 (%).
D
Position Loop Gain: Cn-1A
Adjust the position loop gain to the rigidity of the machine. Set to between 50 and 70 (1/s) for general NC
machine tools, to between 30 and 50 (1/s) for general and assembly machines, and to 10 to 30 (1/s) for
industrial robots.
Load alarms will be caused by machine oscillation if the position loop gain is increased for systems with
low rigidity or systems with intrinsically low-frequency vibration.
The setting range is 1 to 500 (1/s), and the factory setting is 40 (1/s).
D
Positioning Completed Range: Cn-1b
This sets the deviation counter value for outputting the positioning completed output (INP). When the
deviation counter value falls below this setting, the positioning completed output turns ON. The setting
range is 0 to 250 (command units), and the factory setting is 3 (command units).
D
Bias Rotational Speed: Cn-1C
This is the setting for position control bias. Use this setting according to the load conditions in order to
shorten positioning time. The setting range is 1 to 450 (r/min), and the factory setting is 0 (r/min).
Specifications
Chapter 5
Содержание OMNUC 88D-UP20HA
Страница 11: ...Warning Labels for Models Conforming to EC Directives Warning label 1 Warning label 2...
Страница 31: ...2 8 D R88A PR03U 54 57 5 15 6 9 System Design and Installation Chapter 2...
Страница 188: ...5 53 H Mounting Dimensions D R88A TK01U D R88A TK02U Two M5 Three M5 Specifications Chapter 5...