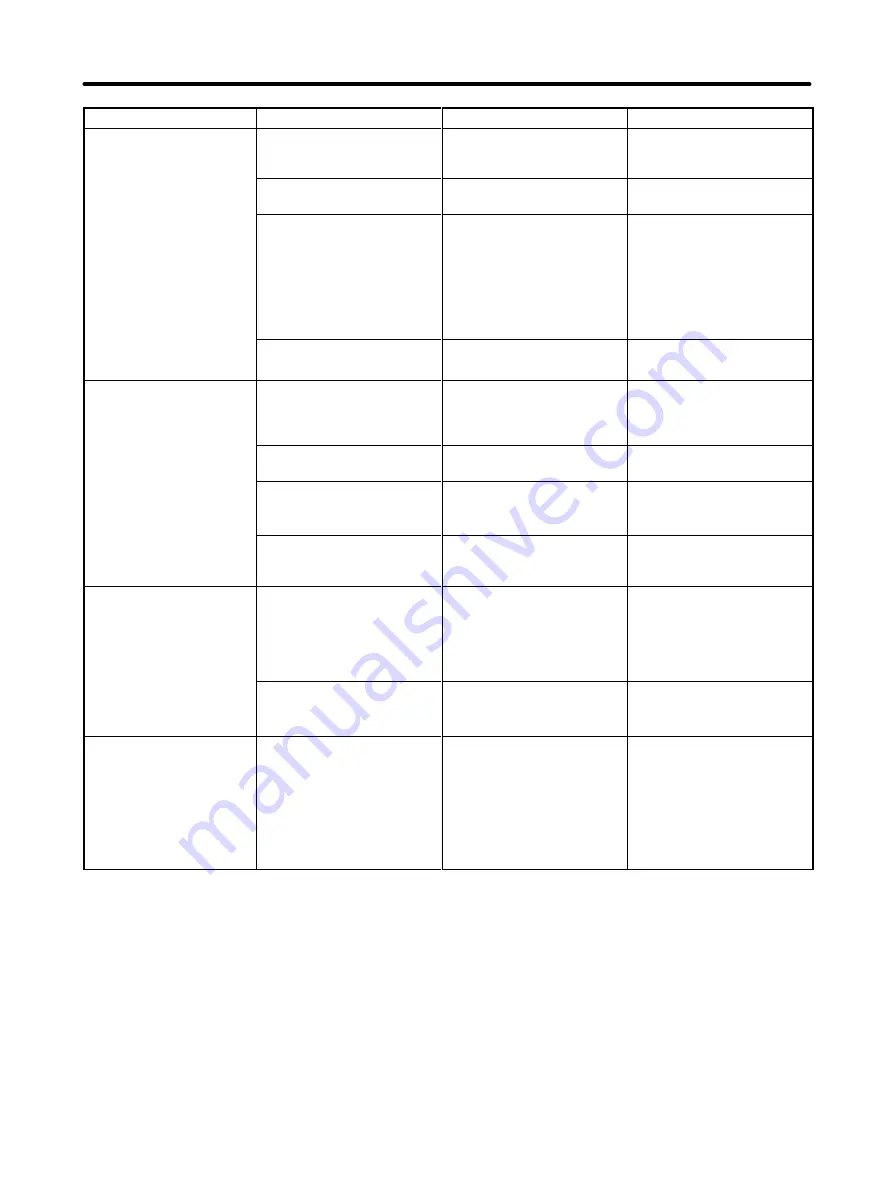
4-16
Symptom
Countermeasures
Items to check
Probable cause
Servomotor operation is
unstable.
The Servomotor power lines
or encoder lines are wired
incorrectly.
Check the Servomotor pow-
er line U, V, and W phases,
and the encoder line wiring.
Correct the wiring.
The settings for the bias
function are not correct.
---
Adjust bias revolutions and
positioning completed range.
There are eccentricities or
looseness in the coupling
connecting the Servomotor
shaft and the mechanical
system, or there are load
torque fluctuations according
to how the pulley gears are
engaging.
•
Check the machinery.
•
Try operating the Servo-
motor without a load.
Adjust the machinery.
Gain is wrong.
---
•
Use auto-tuning.
•
Adjust the gain manually.
Servomotor is overheating. The ambient temperature is
too high.
Check to be sure that the
ambient temperature around
the Servomotor is no higher
than 40
°
C.
Lower the ambient tempera-
ture to 40
°
C or lower. (Use a
cooler or fan.)
Ventilation is obstructed.
Check to see whether any-
thing is blocking ventilation.
Ensure adequate ventilation.
There is an overload.
Check the torque command
value by means of monitor
mode.
•
Lighten the load.
•
Change to a larger capac-
ity Servomotor.
The correspondence be-
tween the Servo Driver and
the Servomotor is incorrect.
Check the models.
Combine models that corre-
spond correctly.
There are unusual noises.
The machinery is vibrating.
Inspect the machinery to see
whether there are any for-
eign objects in the movable
parts, or whether there is
any damage, deformation, or
looseness.
Fix any problems causing
vibration.
The speed loop gain adjust-
ment is insufficient.
---
•
Use auto-tuning.
•
Adjust the gain manually
(speed loop gain).
Vibration is occurring at
the same frequency as the
applicable power supply.
Inductive noise is occurring.
•
Check to see whether the
Servo Driver control signal
lines are too long.
•
Check to see whether con-
trol signal lines and power
supply lines are too close
to each other.
•
Shorten the control signal
lines.
•
Separate control signal
lines from power supply
lines.
•
Use a low-impedance
power supply for control
signals.
Application
Chapter 4
Содержание OMNUC 88D-UP20HA
Страница 11: ...Warning Labels for Models Conforming to EC Directives Warning label 1 Warning label 2...
Страница 31: ...2 8 D R88A PR03U 54 57 5 15 6 9 System Design and Installation Chapter 2...
Страница 188: ...5 53 H Mounting Dimensions D R88A TK01U D R88A TK02U Two M5 Three M5 Specifications Chapter 5...