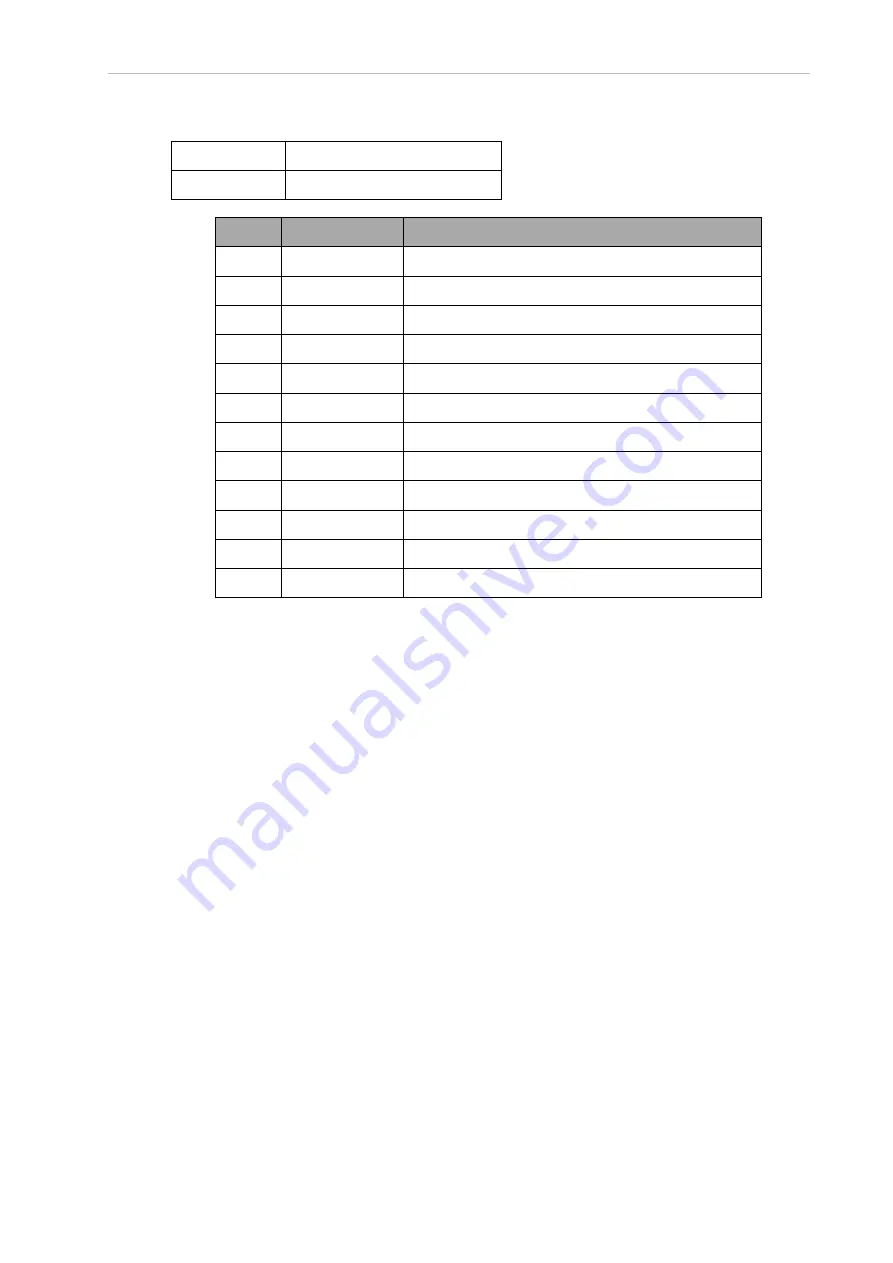
Chapter 6: Connectivity
User Interface
Connector type Mini-Fit
®
7 x 2
Use
Brake release, ON, OFF, E-Stop
Pin No.
Designation
Notes
1, 2, 3
FBAT_ALWAYS
Fused VBAT @ 500 mA
4
ESTOP_USR_1L
Short 4 & 11 to close ESTOP_USR_1
5
ESTOP_USR_2L
Short 5 & 12 to close ESTOP_USR_2
6
ESTOP_OUT_1L
Pins 6 & 13 short when ESTOP_CH1 is closed
7
ESTOP_OUT_2L
Pins 7 & 14 short when ESTOP_CH2 is closed
8
OFF_BUTTON
Short to FBAT_ALWAYS to signal OFF (min 1 s pulse)
9
START_BUTTON
Short to FBAT_ALWAYS to signal ON (min 1 s pulse)
10
MOTOR_BRAKE
Short to FBAT_ALWAYS for manual brake release
11
ESTOP_USR_1H Short 4 & 11 to close ESTOP_USR_1
12
ESTOP_USR_2H Short 5 & 12 to close ESTOP_USR_2
13
ESTOP_OUT_1H Pins 6 & 13 short when ESTOP_CH1 is closed
14
ESTOP_OUT_2H Pins 7 & 14 short when ESTOP_CH2 is closed
NOTE:
An E-Stop jumper or a user-supplied E-Stop button needs to be attached
to the E-STOP port on the User Interface connector for the platform to function.
The jumper is provided as part number 12730-000L. An E-Stop button would be
user-supplied.
NOTE:
Engaging the E-Stop through the external connector or Operator Panel
(faster than 250 ms), will cause motors to re-engage after E-stop is released.
Motor re-engagement occurs because the core is designed to receive a consistent
E-Stop signal for at least 250 ms. Signals that engage and disengage in a time
period shorter than 250 ms, will cause LD to assume that the change was due to
a bumper press, which will automatically re-engage the motors. No signal on the
E-Stop chain can cause the robot to operate while the E-Stop remains engaged.
Thus it is necessary to leave the E-Stop engaged, if the intent is to keep the robot
in a E-Stop state.
14766-000 Rev H
LD Cart Transporter User's Manual
99