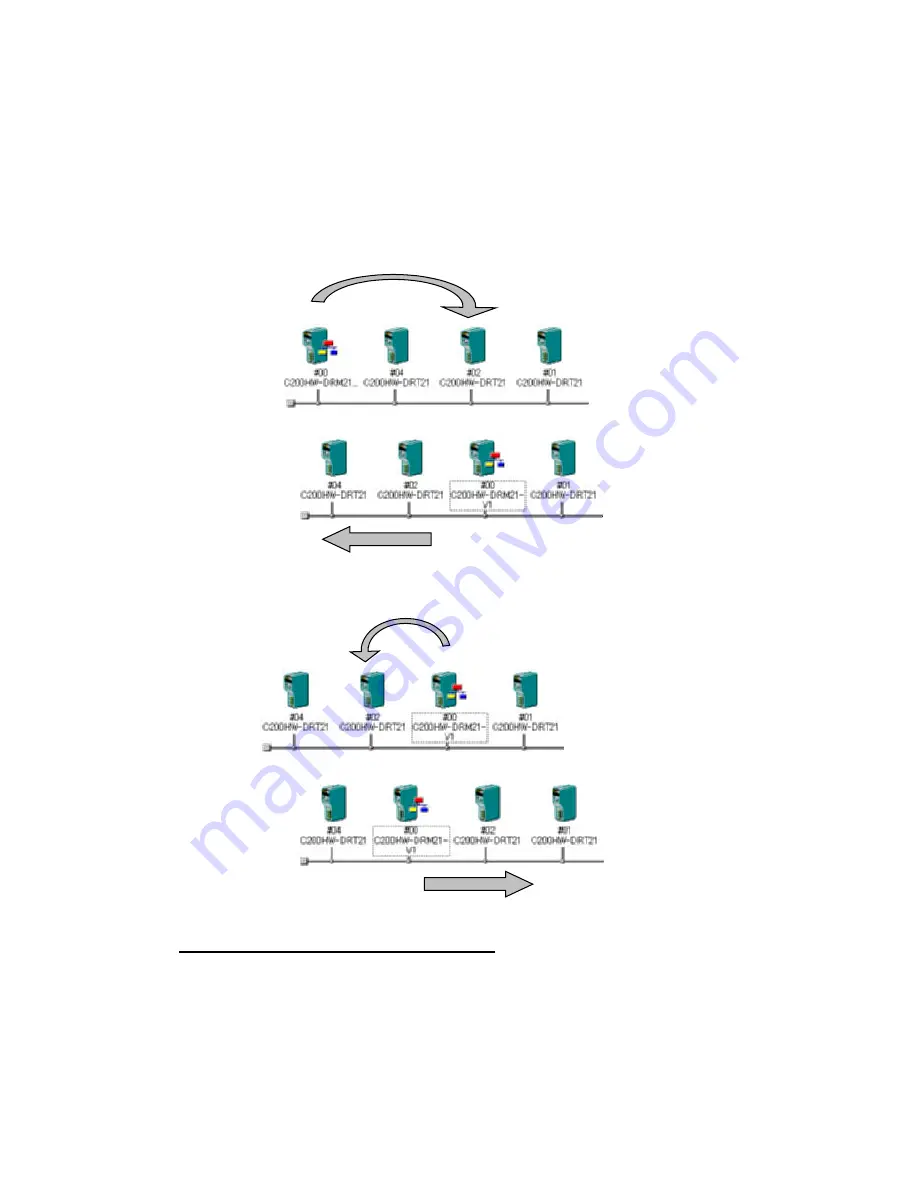
2-5
Creating Virtual Network Configurations Offline
2-5-4 Editing
Components (Devices)
DeviceNet Networks
Use the following procedure to change the display locations of DeviceNet components
in the Network Configuration Window.
1 Right-click the device to be moved and drag it.
2 Drop the device at the new location where it is to be displayed.
3 The new device will be moved to the new display location.
Example 1: Moving Device #00 to the Location of Device #02
Drop.
Drag.
Right-click.
Other devices will move
in this direction.
Example 2: Moving Device #00 to the Location of Device #02
Drop.
Drag.
Right-click.
Other devices will move
in this direction.
Changing DeviceNet Device Comments
Component - Change Device Comment
Comments can be registered for DeviceNet devices registered in a network.
The default comment is the product name.
Use the following procedure to change the device comment.
1 Select the device to be edited.
2 Select
Component - Change Device Comment
.
The Change Device Comment Dialog Box will be displayed.
2-36
Содержание CX-INTEGRATOR - V1.1
Страница 1: ...OPERATION MANUAL CX Integrator Ver 1 1 SYSMAC CXONE AL C E Cat No W445 E1 02...
Страница 2: ...CXONE AL C E CX Integrator Ver 1 1 Operation Manual Revised November 2005...
Страница 3: ...iv...
Страница 5: ...vi...
Страница 13: ...xiv...
Страница 120: ...Communications Section 3 Routing Tables This section describes how to set the routing tables 3...
Страница 200: ...Communications Section 5 Ethernet This section describes the operations specific to Ethernet 5...
Страница 292: ...Communications Section 8 NT Links This section explains the settings and operations specific to the NT Link system 8...
Страница 328: ...Appendices A...
Страница 336: ......