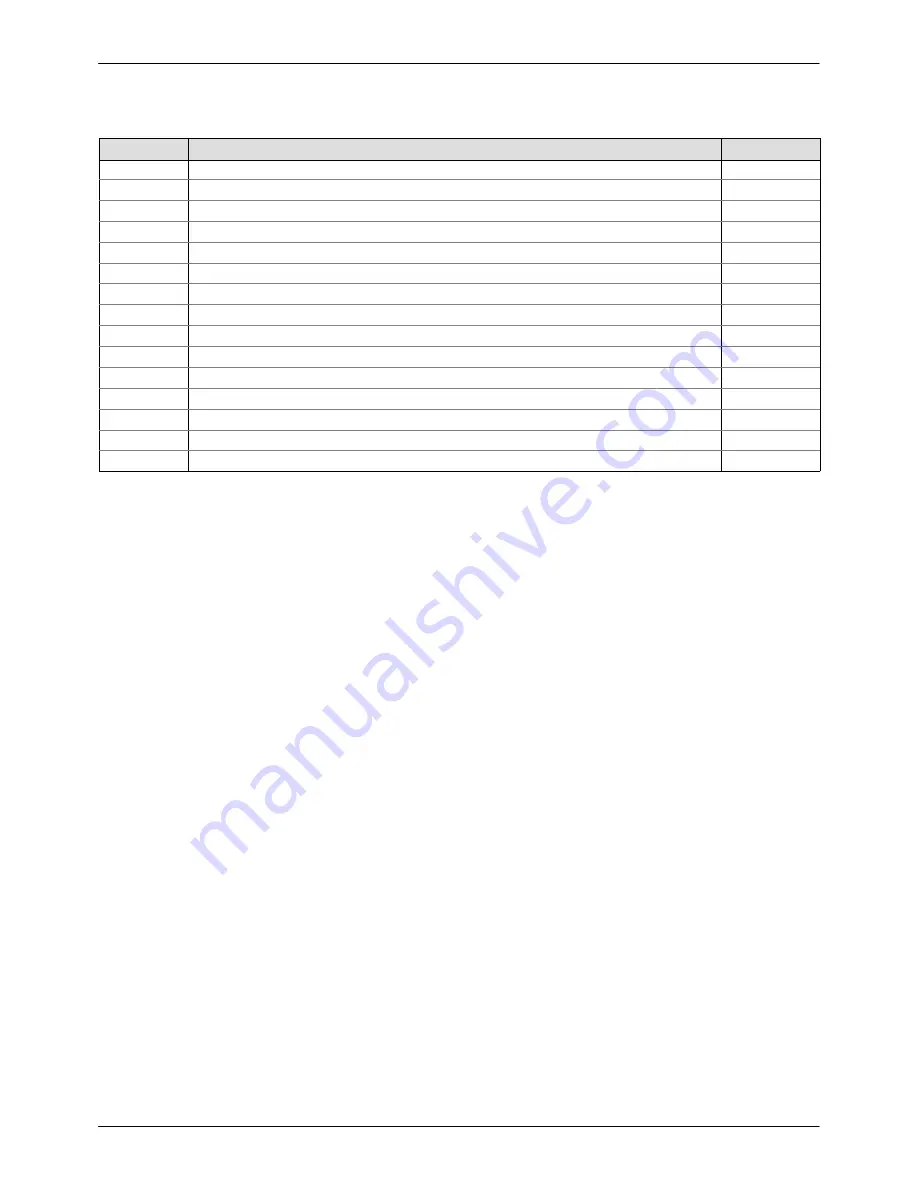
Parts
6-2
Part 1603054-02
E
2015 Nordson Corporation
Console Part Number List
Part
Description
Note
1602177
Controller, iControl, Encore HD, 4 gun
1602178
Controller, iControl, Encore HD, 6 gun
1602179
Controller, iControl, Encore HD, 8 gun
1602180
Controller, iControl, Encore HD, 10 gun
1602181
Controller, iControl, Encore HD, 12 gun
1602182
Controller, iControl, Encore HD, 14 gun
1602183
Controller, iControl, Encore HD, 16 gun
1602184
Controller, iControl, Encore HD, 18 gun
1602185
Controller, iControl, Encore HD, 20 gun
1602186
Controller, iControl, Encore HD, 22 gun
1602187
Controller, iControl, Encore HD, 24 gun
1602188
Controller, iControl, Encore HD, 26 gun
1602189
Controller, iControl, Encore HD, 28 gun
1602190
Controller, iControl, Encore HD, 30 gun
1602191
Controller, iControl, Encore HD, 32 gun
Obsolete
Содержание Encore HD iControl System
Страница 4: ...Change Record ii Part 1603054 02 E 2015 Nordson Corporation O b s o l e t e ...
Страница 8: ...Table of Contents vi Part 1603054 02 E 2015 Nordson Corporation O b s o l e t e ...
Страница 22: ...System Overview 2 10 Part 1603054 02 E 2015 Nordson Corporation O b s o l e t e ...
Страница 40: ...Installation 3 18 Part 1603054 02 E 2015 Nordson Corporation O b s o l e t e ...
Страница 88: ...Parts 6 10 Part 1603054 02 E 2015 Nordson Corporation O b s o l e t e ...
Страница 89: ...Wiring Diagrams 7 1 Part 1603054 02 E 2015 Nordson Corporation Section 7 Wiring Diagrams O b s o l e t e ...
Страница 90: ...Wiring Diagrams 7 2 Part 1603054 02 E 2015 Nordson Corporation O b s o l e t e ...
Страница 92: ...O b s o l e t e ...