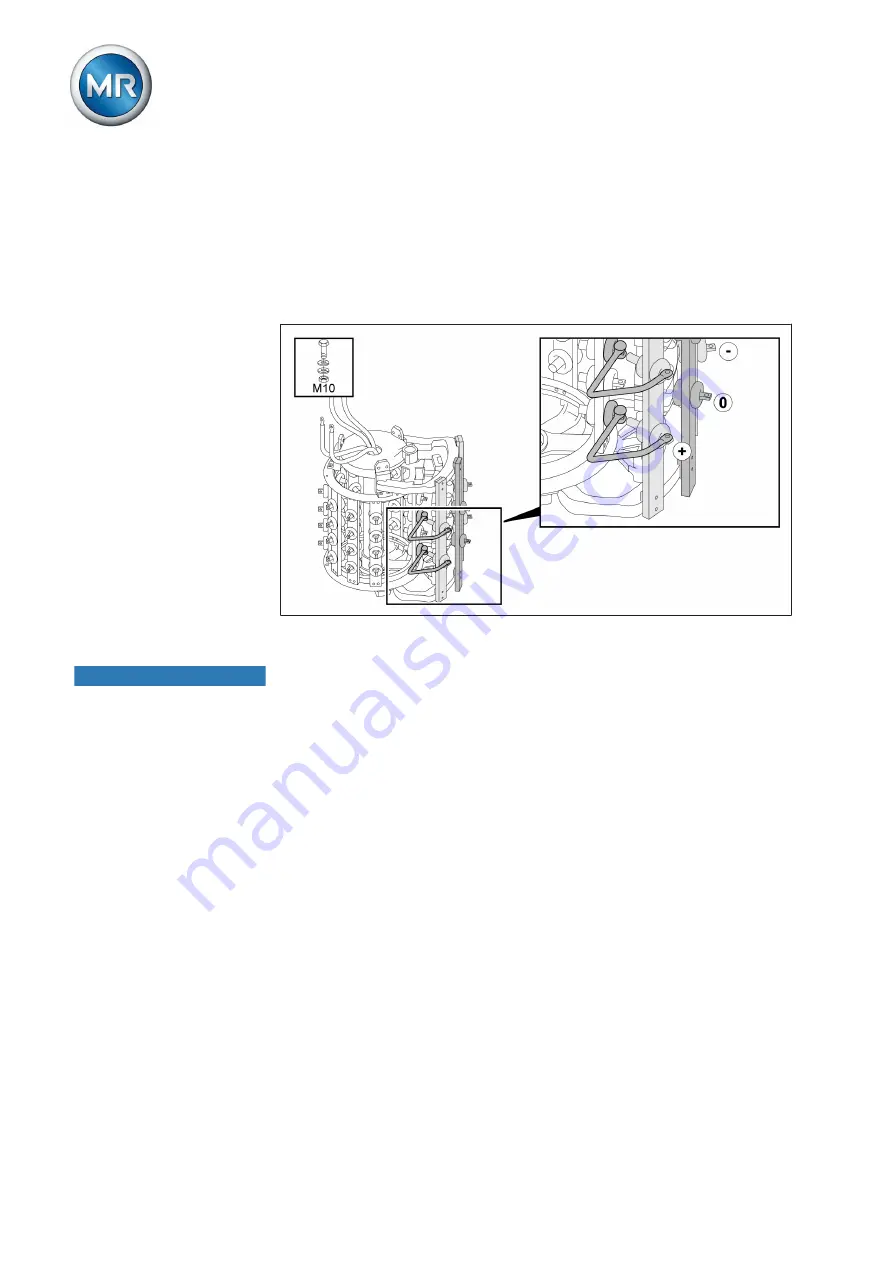
5 Assembly: Standard design
Maschinenfabrik Reinhausen GmbH 2015
56
4349315/00 EN
VACUTAP® VR®
Change-over selector connection contacts for coarse tap
selector connection VRC/VRE
With coarse tap selector connection, the (+) and (-) change-over selector
connection contacts are secured to the respective laminated paper bars of
the coarse change-over selector. Their external appearance is identical to
the fine tap selector contacts (through-hole for M10 screws, always in verti-
cal position).
Figure 41: Change-over selector connection contacts for coarse tap selector connec-
tion
NOTICE
Damage to the on-load tap-changer!
Connection leads situated too close to the change-over selector's moving
parts block the change-over selector and therefore result in on-load tap-
changer damage!
► Connection leads in the area of the change-over selector have to be
routed such that they are at a sufficient distance from the change-over
selector's moving parts.
5.3.4
Содержание VACUTAP VR
Страница 1: ...On Load Tap Changer VACUTAP VR Installation and Commissioning Instructions 4349315 00 EN ...
Страница 246: ...14 Appendix Maschinenfabrik Reinhausen GmbH 2015 246 4349315 00 EN VACUTAP VR ...
Страница 248: ...14 Appendix Maschinenfabrik Reinhausen GmbH 2015 248 4349315 00 EN VACUTAP VR ...
Страница 266: ......
Страница 267: ......