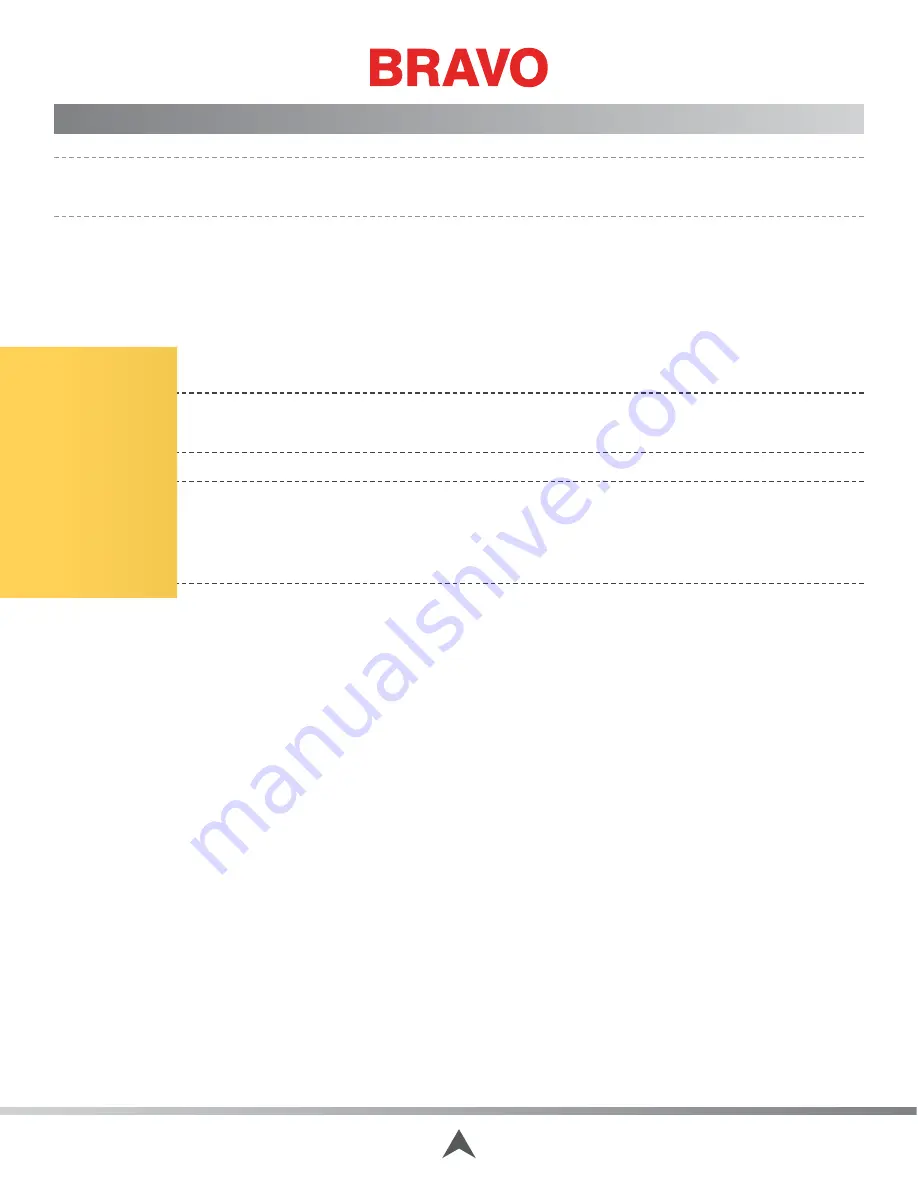
205 of 271
X-Drive Cable Installation
•
This repair requires timing and other adjustments and should be done by an authorized service
technician.
When installing the x-drive cable it is extremely important that you do not damage the protective coat-
ing of the cable, ensure that the windings on the cable spool are correct, that the cable is correctly ten-
sioned, and the installation is done precisely as provided in these instructions.
When replacing the x-drive cable it is strongly recommended that the x-drive cable assembly be ordered
and installed. The precision windings and lengths of the cable extending from the spool is critical and is
best done only at the factory.
CAUTION!!
Use extreme care to avoid damaging the protective coating on the x-drive cable. If
the coating is damaged, the cable will eventually fray and/or corrode.
CAUTION!!
At any time when the machine is either powered down or in E-Stop mode, neither
the X-Carriage nor the X-Beam should be moved at a high rate of speed. If there is a desire to
manually move either the carriage or the beam, they should be pushed or pulled GENTLY to
prevent serious damage to the main control board.
Replacement Parts Needed:
• x-cable assembly (x-cable prewound on spool)
• Order other replacement parts if needed, such as pulleys
• Replacement hardware if any screws or nuts are stripped
X-Cable Assembly Installation:
1. Remove left and right arm covers.
2. Remove the upper arm back cover.
3. Remove the old x-drive cable assembly.
4. Make sure the x-carriage is positioned all the way to the right (as seen from the back of the ma-
chine) at a hard stop.
5. Verify the 8mm bushing is installed on the X-motor shaft.
Table of Contents
Содержание Bravo
Страница 1: ...Technical Manual Rev 082115 ...