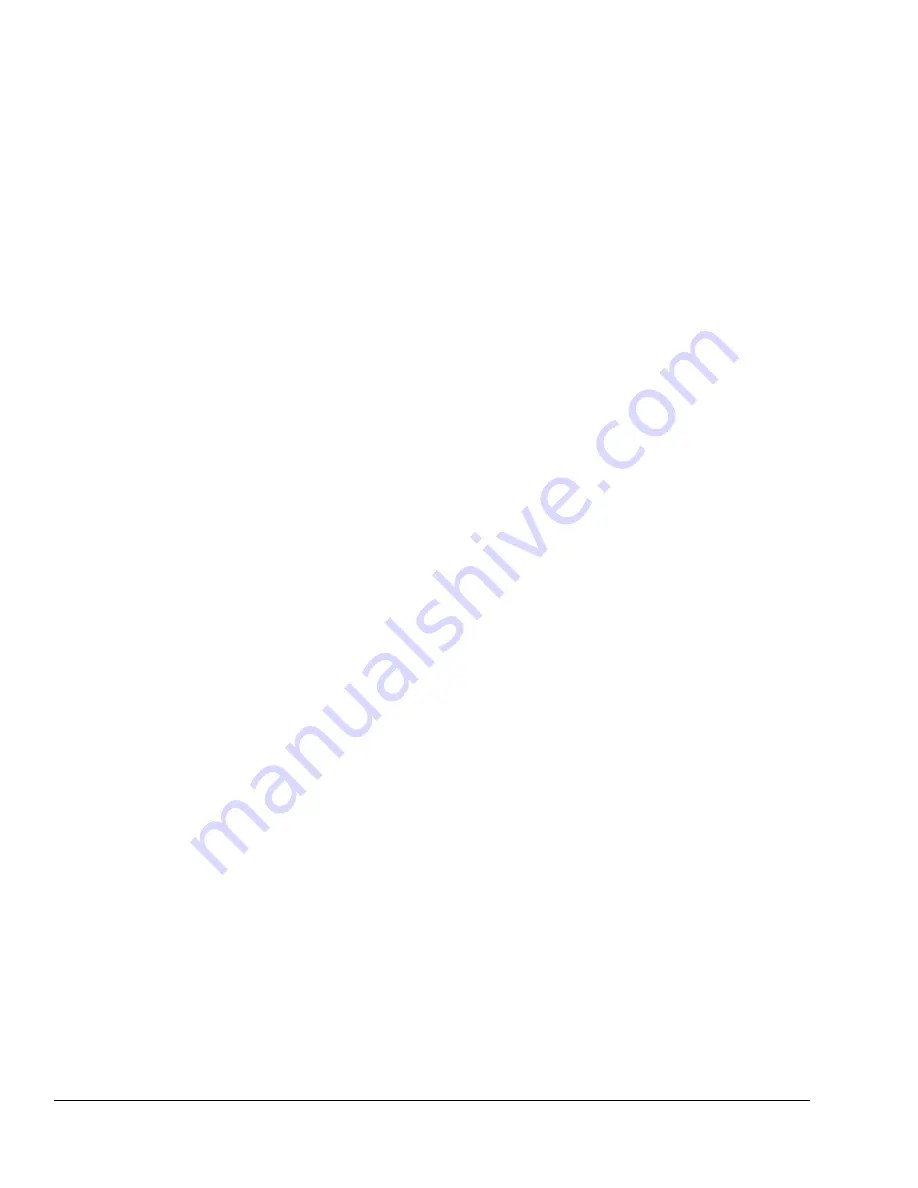
April 17, 2000
Man ual Versio n 1.0
5.8
Pressure can be set in one of two ways. First, if the air system was correctly configured, the desired
force which the pressure is to create can be entered in the “Force Setpoint” row on the air pressure
screen. Second, if preferred, the desired air pressure in psi may be entered into the “pressure setpoint”
row.
For counterbalances, the “Die Weight Set” is the weight of the upper die that attaches to the slide. (The
counterbalance must also offset the weight of the press slide, but since this is a constant accounted for
when the system is configured, only the upper die weight need be entered). The upper die weight, which
is required by OSHA to be stamped on the die, can be entered in the force setpoint row.
For cushions, the “Cush Force Set” is the amount of “push” that is exerted by the air pressure times the
cylinder area.
For hydraulic overloads, the “Press Trip Set” is the value, usually in tons, at which you wish the
hydraulic overload system to trip.
Note that pressure, die weight, cushion force, and trip points are restricted items as defined in section 2.
The RUN/PROG key, a user code, or both may be required to change them. If a force setpoint is
entered, the proper pressure in psi will be calculated and applied to the system. Likewise if pressure is
entered, the force setpoint will be calculated and displayed.
Section 5.2.3 Air System Fault and Status
The last fault and current status of the air system are displayed for diagnostic and informational
purposes. Under normal conditions the “Fault” message should be “None”. If there is a problem with
an air system, it will be reported on the “Fault” line. “Status” gives the current state of the system such
as “At Pressure”, “Filling”, “Dumping” etc. For the most part these messages will be self explanatory.
See section 6 for a complete list of fault and status messages with explanations.
Section 5.3
Job Storage and Recall Issues
There are a few things to keep in mind for job storage and recall:
a) A store operation must be done for the current air pressure and slide adjust setpoints to be stored
in the job number. If you recall a job and then change one or more of the recalled setpoints, the
changed setpoints will
not
be stored for later recall
unless
you store the job again while the
setpoints are set at the new value.
b) Since one or more cushions may or may not be used with any given die, the On/Off status of
each cushion system is stored with the job. For example, Job #1 is stored with “Cushion #1"
turned off. Next, Job #2 is stored with “Cushion #1" turned on. Every time Job #1 is recalled,
“Cushion #1" will be turned off. Every time Job #2 is recalled, “Cushion #1" will be turned on.
Note that if the cushion system is in manual mode then the above does not apply!
c) If a job is recalled when the press is not at the top, the slide adjust system will display a status of
Содержание OmniLink 5000
Страница 5: ...April 17 2000 Manual Versio n 1 0 iv...
Страница 38: ...April 17 2000 Manual Versio n 1 0 4 14...
Страница 63: ...April 17 2000 Manual Versio n 1 0 B 2 Figure B 2 Typical Cushion Wiring Diagram...
Страница 64: ...April 17 2000 Manual Versio n 1 0 B 3 Figure B 3 Conceptual Dual Resolver Mounting...
Страница 65: ...April 17 2000 Manual Versio n 1 0 B 4 Figure B 4 Typical AMCI Dual Resolver Wiring Diagram...
Страница 66: ...April 17 2000 Manual Versio n 1 0 B 5 Figure B 5 Typical GEMCO Dual Resolver Wiring Diagram...
Страница 67: ...April 17 2000 Manual Versio n 1 0 B 6 Figure B 6 Conceptual Linear Transducer Mounting...
Страница 68: ...April 17 2000 Manual Versio n 1 0 B 7 Figure B 7 Typical GEMCO Linear Transducer Wiring...
Страница 69: ...April 17 2000 Manual Versio n 1 0 B 8 Figure B 8 Typical MTS Temposonics II Linear Transducer Wiring...
Страница 71: ...April 17 2000 Manual Versio n 1 0 B 10...
Страница 73: ...April 17 2000 Manual Versio n 1 0 C 2...