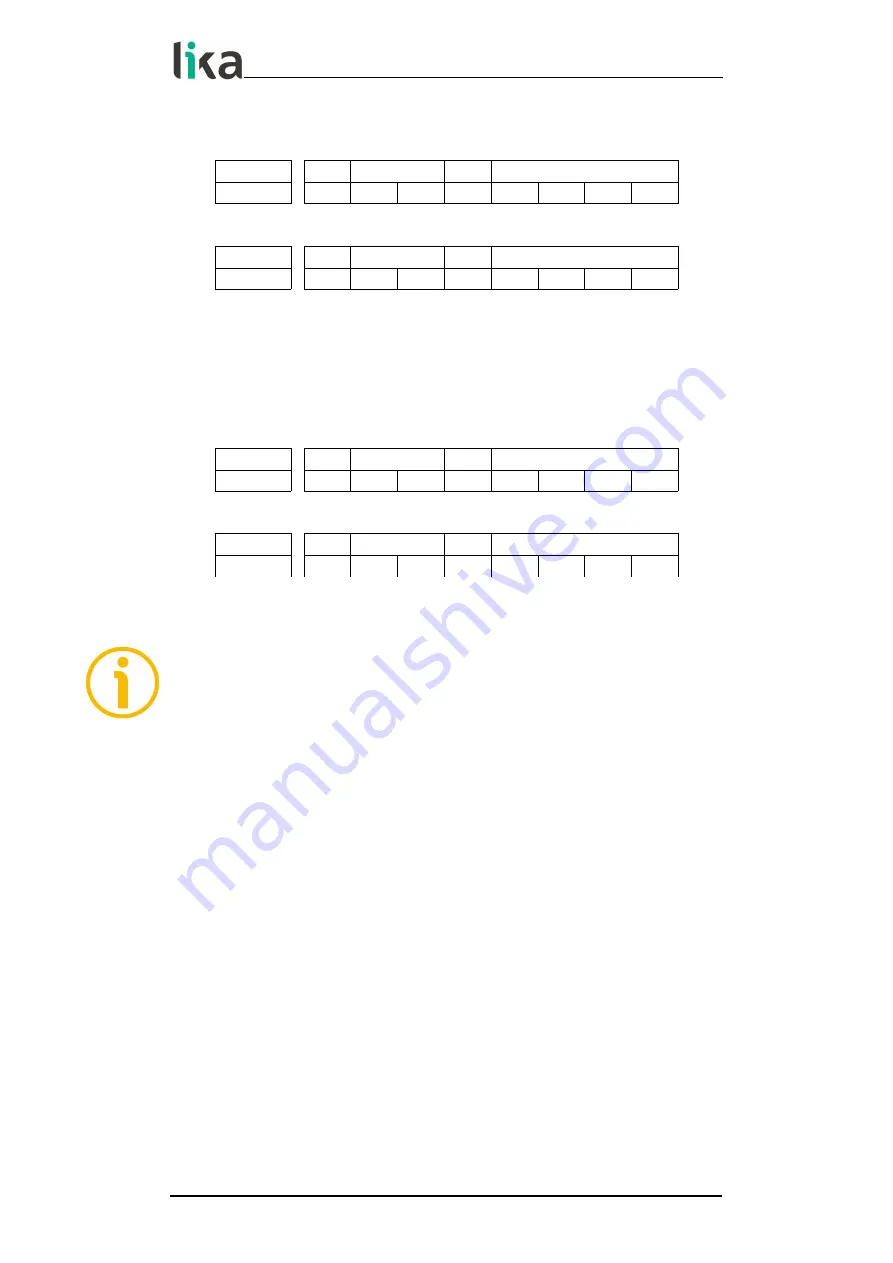
IF55 ROT CANopen®
Read COB-ID used by PDO1 (
sub 1):
Master
Slave (Req request)
COB-ID
Cmd
Index
Sub
Process data
600+ID
40
00
18
01
-
-
-
-
Slave
Master (Req reply)
COB-ID
Cmd
Index
Sub
Process data
580+ID
43
00
18
01
B0
B1
B2
B3
COB-ID used by PDO1 = ( (B3<<24) | (B2<<16) | (B1<<8) | B0 )
set the most significant bit to 0:
B3 &= 0x7F;
Set new COB-ID used by PDO1 (
sub 1):
Master
Slave (Set request)
COB-ID
Cmd
Index
Sub
Process data
600+ID
23
00
18
01
B0
B1
B2
B3
Slave
Master (Set confirmation)
COB-ID
Cmd
Index
Sub
Process data
580+ID
60
00
18
01
00
00
00
00
NOTE
Save the new values using the store parameters function (see the
object). If the power is turned off or in case of
Reset node
and
Restore node
commands, the parameters not saved are lost.
MAN IF55 ROT CB E 1.2.odt
7 - Setting-up
84 of 88
Содержание IF55 ROT CB
Страница 87: ...This page intentionally left blank ...