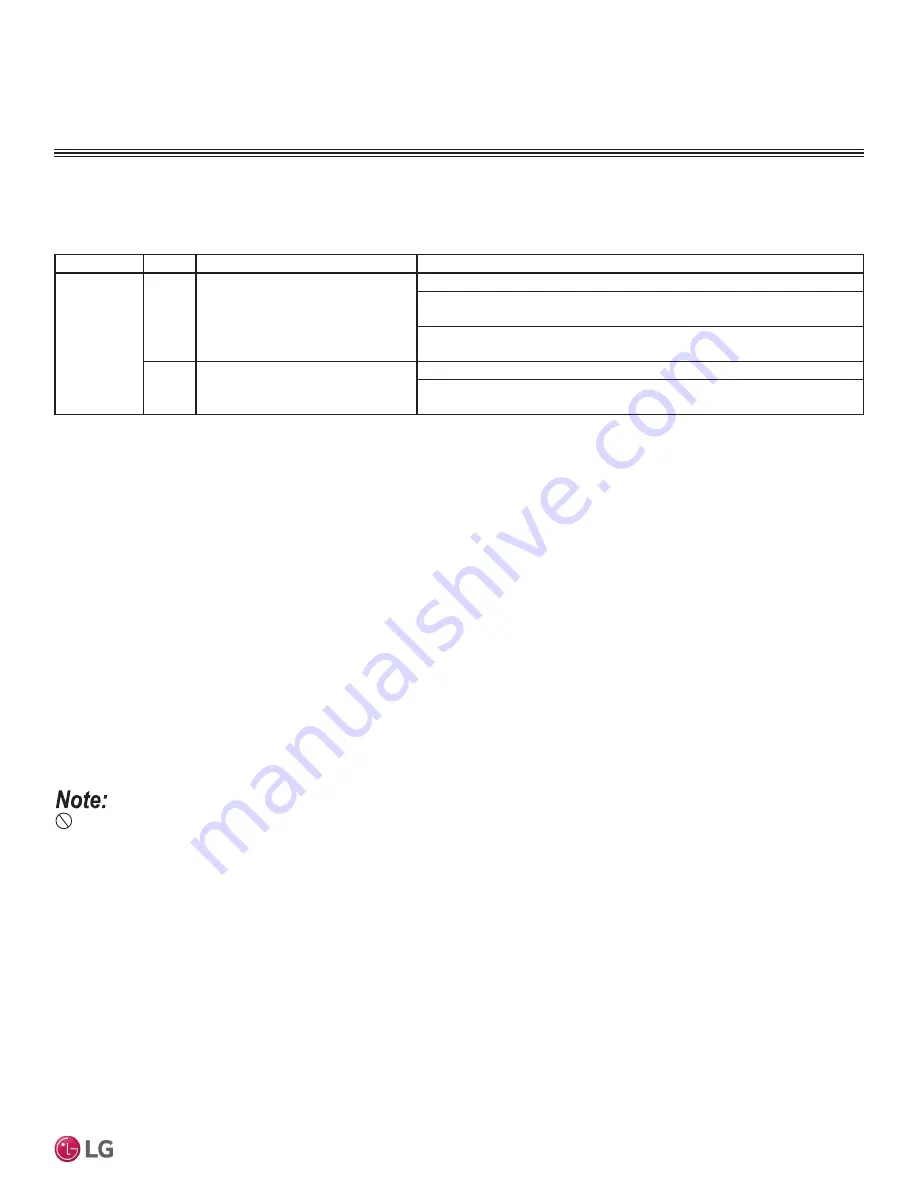
73
W
a
ter System Maintenance
Due to our policy of continuous product innovation, some specifications may change without notification.
©LG Electronics U.S.A., Inc., Englewood Cliffs, NJ. All rights reserved. “LG” is a registered trademark of LG Corp.
WATER SYSTEM MAINTENANCE
Category
Status
Cause
Action
Water source
has
malfunctioned.
CH13
Error detected during flow switch
connection.
Water is not flowing, or water flow
amount is insufficient.
(All operation conditions)
Verify if the water source supply pump is operating.
Check if the water piping is blocked. Strainer needs cleaned, valve is locked,
there is a problem with the valve, there is air in the piping, etc.
Check for a problem with the flow switch. Flow switch is malfunctioning,
unauthorized handling, flow switch is disconnected, etc.)
CH180
Water is not flowing, or water flow
amount is insufficient.
Verify if the water source supply pump is operating.
Check if the water piping is blocked. Strainer needs cleaned, valve is locked,
there is a problem with the valve, there is air in the piping, etc.
Shell-and-Tube Heat Exchanger Maintenance
As scale accumulates, the efficiency of the shell-and-tube heat exchanger may decrease, and / or damage can occur if the flow amount
decreases, causing the heat exchanger to freeze up and burst. It is necessary, therefore, to manage scale accumulation.
1. Before the cooling / heating season, check the following (one [1] time per year).
• Inspect the water quality to see if it falls within standards.
• Clean the strainer.
• Verify that the water flow amount is adequate.
• Check if operation conditions are adequate (pressure, flow amount, water outlet temperature, etc.).
2. To clean the shell-and-tube heat exchanger, follow the procedures below (one [1] time per year).
• Check if a service port is mounted on the water pipe for solvent cleaning.
• A 5% diluted formic acid, citric acid, oxalic acid (water acid), acetic acid, phosphoric acid, etc., are suitable as the solvent for scale cleaning.
'\GURFKORULFDFLGVXOIXULFDFLGQLWULFDFLGHWF7KHVHVROYHQWVKDYHFRUURVLYHSURSHUWLHVWKDWZLOOGDPDJHWKHKHDWH[FKDQJHU
• During the cleaning process, verify that the water inlet and outlet pipe gate valves and drain pipe valves are properly shut.
• Connect the piping for cleaning through water pipe service port, fill the solvent of about 122°F~140°F in the heat exchanger, and circulate
for about two (2) to five (5) hours using a pump. Circulation time may be different according to solvent temperature or amount of scale.
• Closely observe for solvent color changes to decide the circulation time.
• After the solvent circulates, completely drain it out of the heat exchanger. Add 1~2 % concentration sodium hydroxide (NaOH) or hydrocar-
bon sodium (NaHCO3) and circulate for about 15 to 20 minutes to neutralize.
• Flush with clean water. Measure the pH concentration of the water to verify if the solvent is properly removed.
• If another solvent is used, verify that it does not contain any corrosive properties that will damage stainless or copper.
• Contact a local water quality specialist for information regarding cleaning solvents.
3. After cleaning is complete, operate the chiller to see if it functions properly.
Water Management
Troubleshooting Errors that Appear During Test Operation
If CH13 or CH180 occurs during a test run, there is a possibility of the shell-and-tube heat exchanger partially freezing.
Restart the chiller after removing the cause of the partial freezing: Insufficient water flow, a blocked water supply, undercharged system refrig-
erant, foreign particulates inside the shell-and-tube heat exchanger.
Table 39: Water Source Errors.