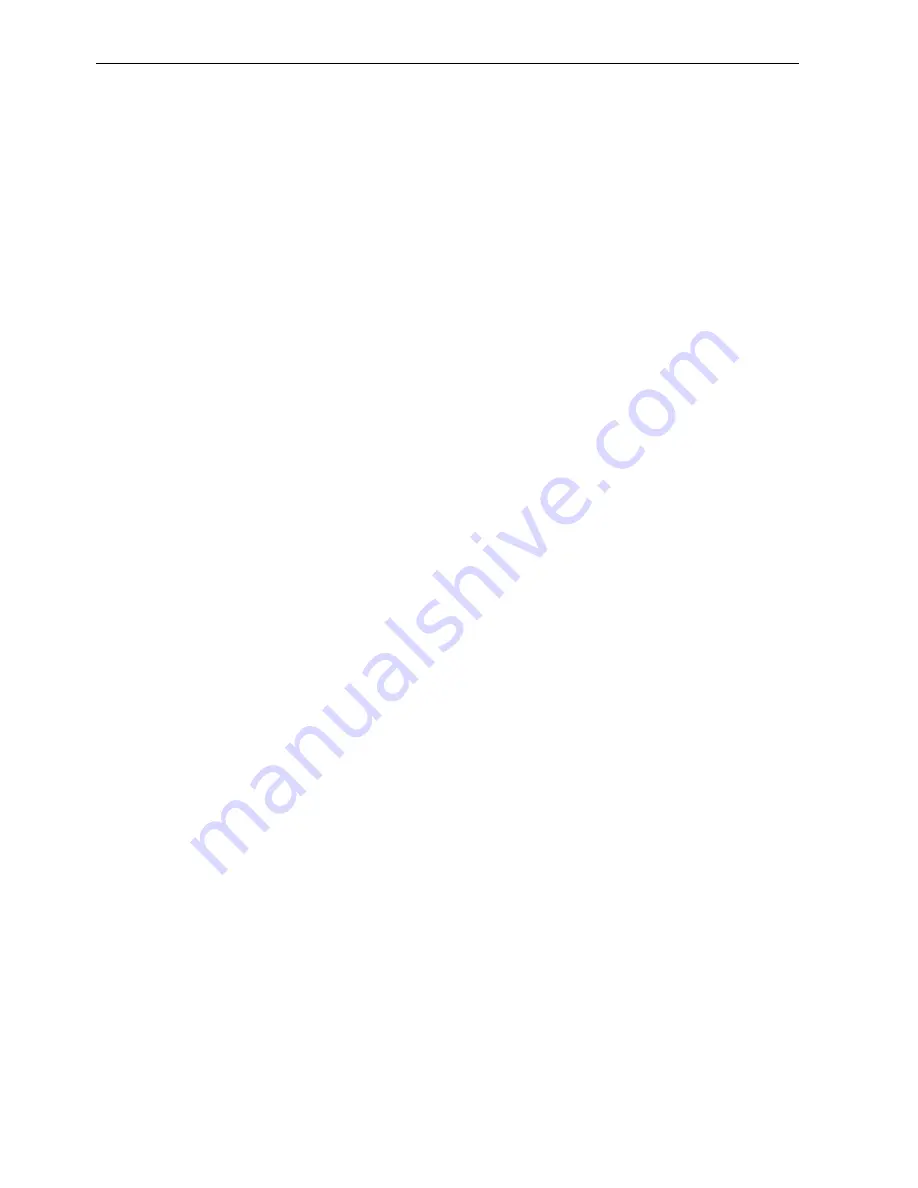
en-76
9
ADJUSTMENTS
9.9
GENERAL INSTRUCTIONS FOR GRAMMER SEATS _______________________
You must not adjust your seat when you drive.
•
After removal of the backrest upholstery, the backrest frame must be held in position with a support before the
backrest adjuster is operated. If you do not secure the frame in position safely, the backrest frame can move
forward suddenly and cause injury.
•
If changes are made to the seat, the changes must be aligned with the series standard of the seat. If
GRAMMER does not approve the parts that are installed in the seat, the seat will not have the correct safety
standards.
•
The functions of the seat will not operate correctly and the safety of the seat is decreased. All changes made
to the seat must be approved by GRAMMER.
During the removal and installation of the GRAMMER driver seat, the instructions supplied by the vehicle
manufacturer must be followed correctly.
•
When you lift the driver seat, do not hold the covers. The covers can break if held when the seat is moved,
which can cause injuries.
•
Before you remove the driver seat, disconnect all plug-in connectors between the seat and the vehicle supply
network. When you replace the plug-in connectors, make sure the connectors are tight so that dust and water
does not enter.
•
To fit new seat belts to the driver seat of the vehicle, the manufacturer must approve of the belts that are
installed. The belts can increase the load in the seat mounting area.
•
To fit new seat belts to the driver seat of the vehicle, the belts must follow local safety regulations and
guidelines. GRAMMER must approve the belts that are installed.
•
Installed seat belts must be fastened before you drive.
•
The seat belt must be replaced after an accident.
•
After an accident with a vehicle that has seat belts installed, the seat and seat mounting must be checked by
the safety
personnel.
•
The fasteners on the seat must be, checked to make sure that the seat is installed in position tightly. If the
seat is not installed tightly, there can be loose bolts or other faults.
•
If the seat does not operate correctly, the seat must be repaired in a workshop. Check the seat for damage to
the seat suspension and bellows or for an incorrect curve in the lumbar support.
•
If you do not correct problems that occur in the seat, the seat can damage your health and increase the risk of
an accident.
•
Before the vehicle is used, the load sensor installed in the seat must be checked to make sure that the sensor
operates correctly. The sensor can stop the operation of mechanical equipment when the driver leaves the
seat.
•
If a problem is found, you must not drive the vehicle. – INCREASED RISK OF ACCIDENT –
•
Do not put the loads on to seats that have a load sensor. A load on the seat can cause the vehicle to start to
move when the driver seat is empty and cause an accident. – INCREASED RISK OF ACCIDENT –
•
If you drive the vehicle and remove the weight from the seat, the vehicle will stop.
•
Do not indent the bellows while there is a load on the driver seat. – RISK OF INJURY FROM BELLOWS –
•
Make sure that dirt and liquids can not get inside the drivers seat.
•
The driver seat is not waterproof and must be protected against water.
•
Any changes or adjustment work done on a GRAMMER driver seat must be done in authorised workshops by
approved personnel. The changes must follow the operation instructions and must be in compliance with all
national regulations.
•
Incorrect installation and assembly hold the risk of personal injury or property damage. The product warranty
will not protect the correct function of the driver seat or the mounted parts.
Содержание Fairway 250 JGZZ250
Страница 8: ...en 7 2 INTRODUCTION NOTES ...
Страница 63: ...en 62 8 MAINTENANCE LUBRICATION 8 2 8 2 8 3 8 4 8 2 8 7 8 8 Fairway 250 Series JZ ...
Страница 73: ...NOTES __________________________________________________________________ ...
Страница 87: ...NOTES __________________________________________________________________ ...