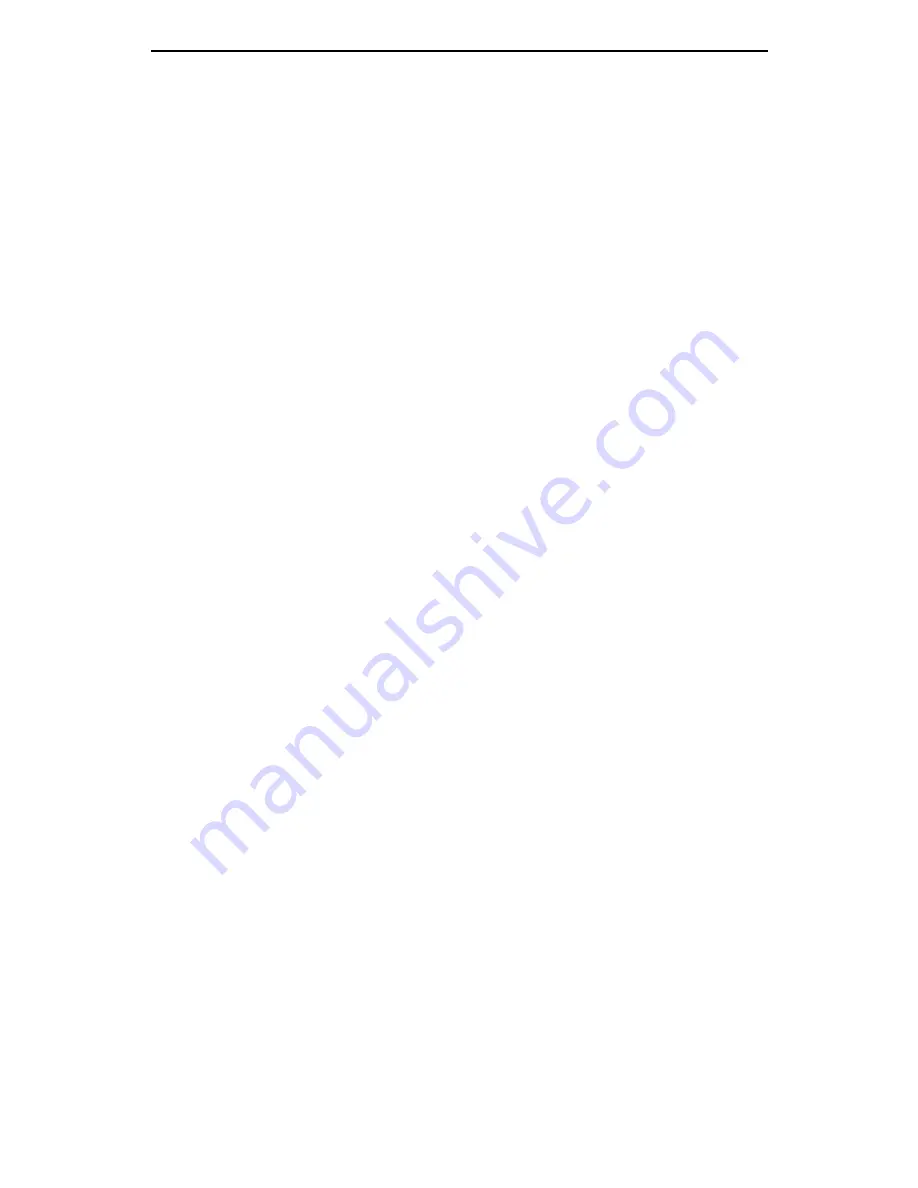
Operation Manual of INVT CHS100 AC Servo Drive 5 Running and operation
43
wiring instruction, please refer to chapter 4.5.2;
Be sure to connect the diode with correct polarity. Otherwise the protection
circuit may not be work normally. If the internal 24V power supply is used,
the sum of the external relays current the should be less than 100mA. For
detailed wiring instruction, please refer to chapter 4.5.5;
fault alarm terminal (ALM) transistor is ON in normal (no fault) cases.
5.1.2 Powering on for the first time
Before powering on, be sure to check the following items:
1) Wiring
The power (R, S, T, r, t) of the servo drive must be connected correctly;
The output (U, V, W) phases of the servo drive must be consistent with the
phases of the servo motor;
There must be no short-circuit between the output (U, V, W) and the input
(R, S, T);
All wirings comply with the standard wiring diagram shown in chapter 5.1.1;
Ensure the external servo enabling terminal (SON) is in OFF state;
The servo drive and the servo motor must be grounded reliably;
When the external braking resistor is used, the shorting wire between B2
and B3 on terminal X2 must be removed;
Connector CN1 cannot be applied with a voltage higher than DC24V;
The stress on the cables is within the specified range.
2) Environment
There is no wire piece, metal chip and other foreign objects which can
cause short-circuit of the signal lines and the power lines in the
surrounding.
3) Mechanical parts
The installation and the connection of shaft and mechanism must be
reliable;
The servo motor and its connected machinery must be ready for operation;
Do not operate the motor with a negative load. The so-called negative load
means the output torque direction of the motor is opposite to the direction
of the motor speed.