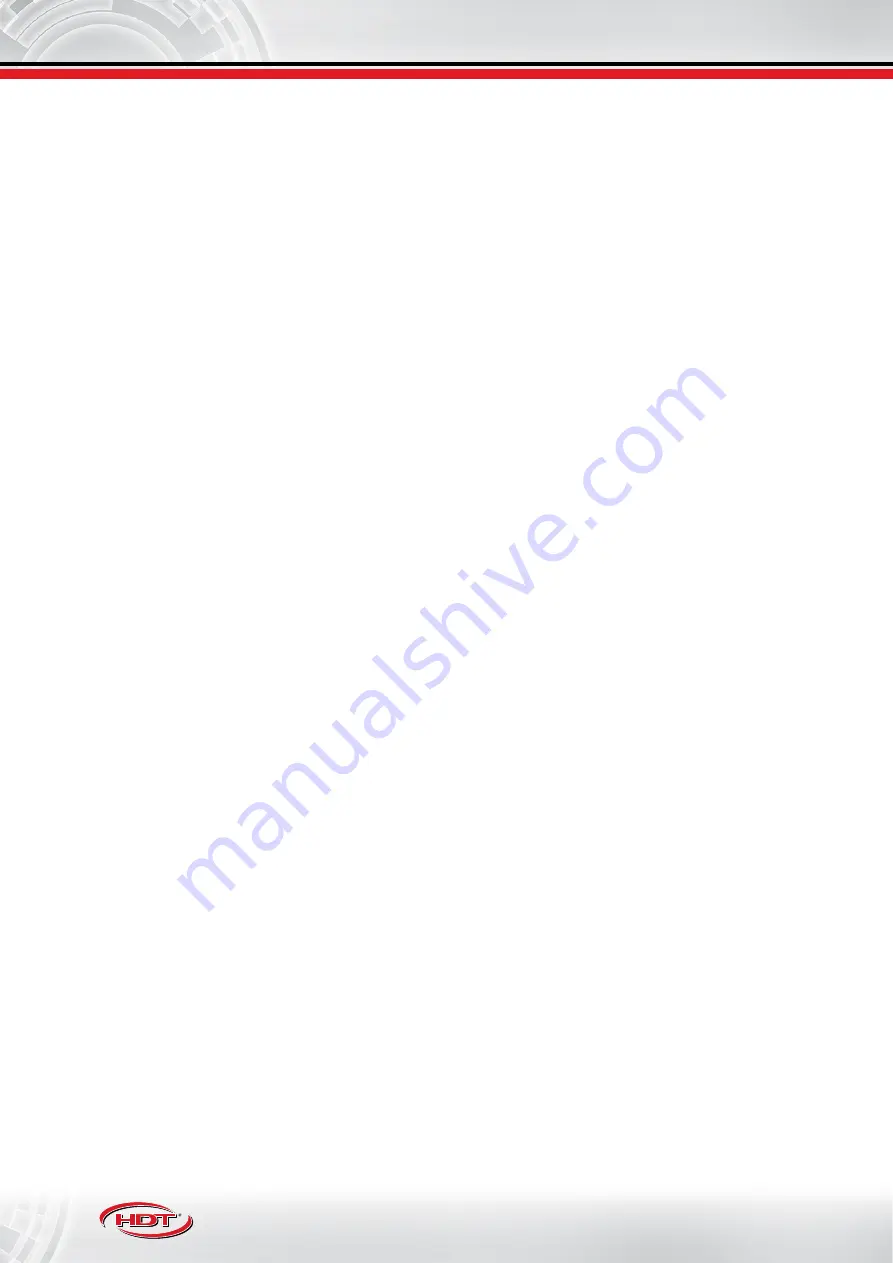
72
Installation and user guide
Rev: 4.0
NTT 240/460
Operation mode
6.04.2 HALT function
HALT function is achieveable via digital input or via fieldbus operation mode and it’s available only when
DRIVE
OK
(o
WARNING
) condition is active.
Settings for this function are shown below:
•
Inertia stop: drive goes immediatly into
SWITCH-OFF
status disabling power to motor.
•
Ramp controlled stop, setting related ramp parameter, then drive goes into
SWITCH-OFF
status disabling
power to motor.
•
Ramp controlled stop, setting related ramp parameter, then drive goes into
SWITCH-ON
status providing
current to motor in standstill.
•
Limit torque stop, setting related torque limit parameter then drive goes into
SWITCH-OFF
status
disabling power to motor.
During fieldbus operation mode, in addition to HALT, other emergency stop functions are available managing
them via fieldbus that allow to set drive behaviour during particular operating conditions.
These function are shown below:
•
QUICK STOP, set via fieldbus control word, with slow and quick ramp, and managing the SWITCH-ON o
SWITCH OFF status.
•
COMUNICATION TIMOUT for managing the emergency stop when fieldbus comunication timeout
occures.
Some settings are not available depending on operation mode.
For further information about fieldbus emergency stop, please see related manuals available at enterprise website:
6.04.3 Safe Torque Off safety stop function
Safe Torque Off hardware safety function is realized with IEC EN 61800-5-2 law reference conformal, 0 stop category,
and with IEC61508 law reference for SIL3.
The Safe Torque-Off (STO) feature of NTT 240/460 drive is made of a redundant electrical circuit designed to bring
a drive to a state of safe torque absence. It is a feature used to prevent unexpected motor rotation in case of
emergency without the necessity to interrupt power supply. When STO function is active, the servodrive and the
motor are in a state of functional safety, which means that is impossible to cause an active rotation of motor shaft
or, if it is alredy rotating, it stops by inertia.
The safety stop category 0 is achieved with the immediate disconnection of electronic components (IGBT) capable
of system energization, that cause an uncontrolled stop of the axis, by inertia.
For further information about this function, please see
Содержание NTT 240
Страница 129: ......