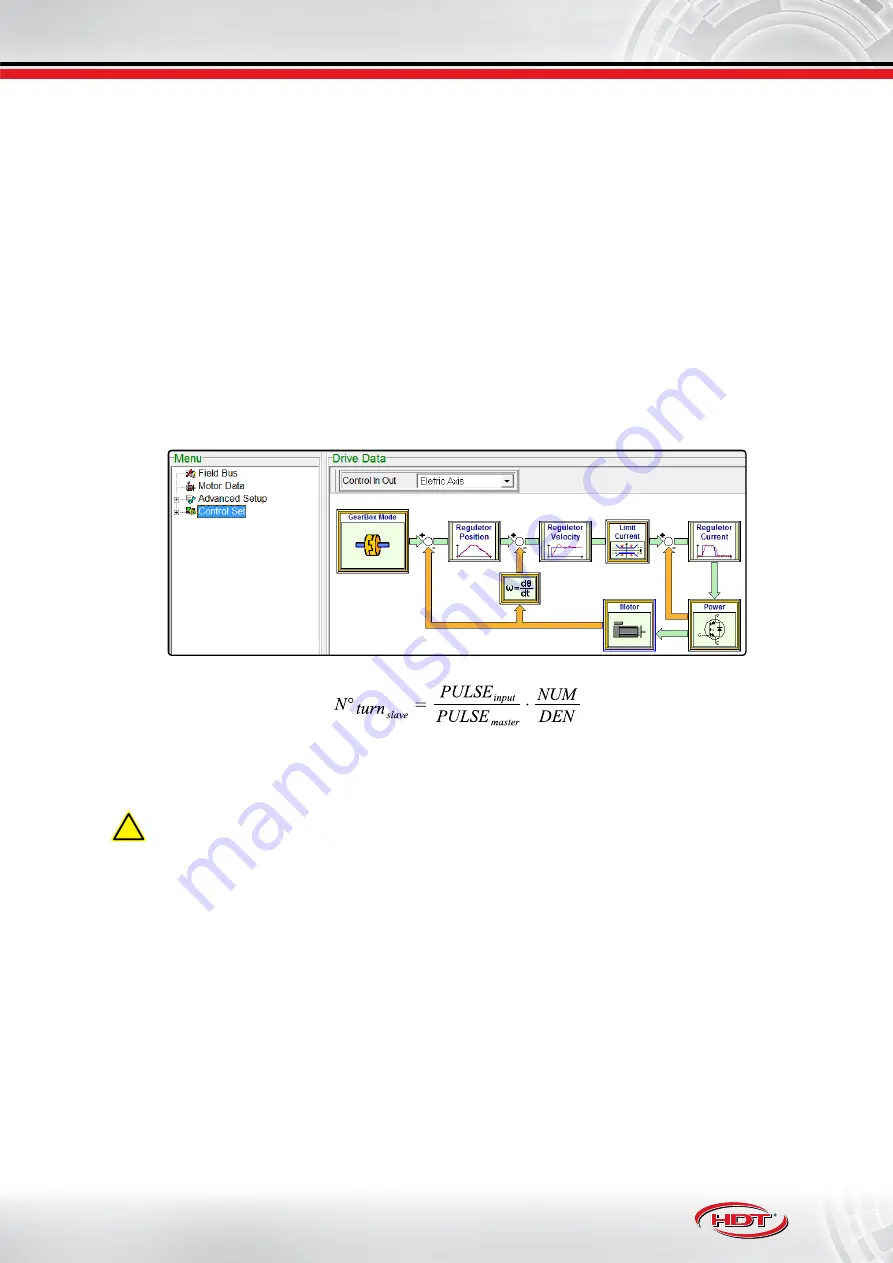
103
NTT 240/460
Operation mode
Installation and user guide
Rev: 4.0
6.15.4 Position control: electronic gearbox mode
Operation conditions:
•
control is available with any supported motor type and with any supported feedback, except for sensorless (Hall
sensor feedback is not recommended).
•
main position reference can be only frequency reference: CHA-CHB, Pulse-Direction and CW-CCW.
•
control is available for I/O, Modbus RTU, Canopen and Ethercat operation mode.
•
about regulation, position/speed/current regulators are available.
•
brake motor management is available.
•
trapezoidal ramps are available.
The following image shows an example of I/O setting, then you can set:
•
axis ratio: numerator (NUM) and denominator (DEN).
•
master device pulse number (PULSE
master
): it provides to slave the information about master device pulse number.
•
engage, disengage and phase shift for slave axis parameters and also Homing and JOG parameters.
•
optimal PID regulators for application.
•
desired digital I/O.
Therefore, number per turn performed by slave device, depending on frequency signal received, is shown below:
Ratio between pulse number, read by slave drive (PULSE
input
), and set master pulse number (PULSE
master
) provides
information about axis position of master device, whereas ratio between NUM and DEN provides information about
percentage axis position in turn of slave device related to master position in turn.
!
In order to obtain a correct operation, please ensure to perform Factors calculation procedure: please see
.
See
“Ch. 5 Wiring and connections” pag. 26
for more details about connectors:
»
J5-6 connector
: for feedback connection, see:
1.
“6.03.2.e Incremental encoder with/without HALL sensors” pag. 57
2.
“6.03.2.g SSI absolute encoder” pag. 58
3.
»
J3 and J7-8-9 connector
:
1. provide the main position reference (pins 1 to 6 of J7). For details about input reference, please see
.
2. for fieldbus operation modes, connect J3 connector and see related fieldbus manuals for information about all
control topology parameters.
3. connect the appropriate input and output signals (please see
).
Содержание NTT 240
Страница 129: ......