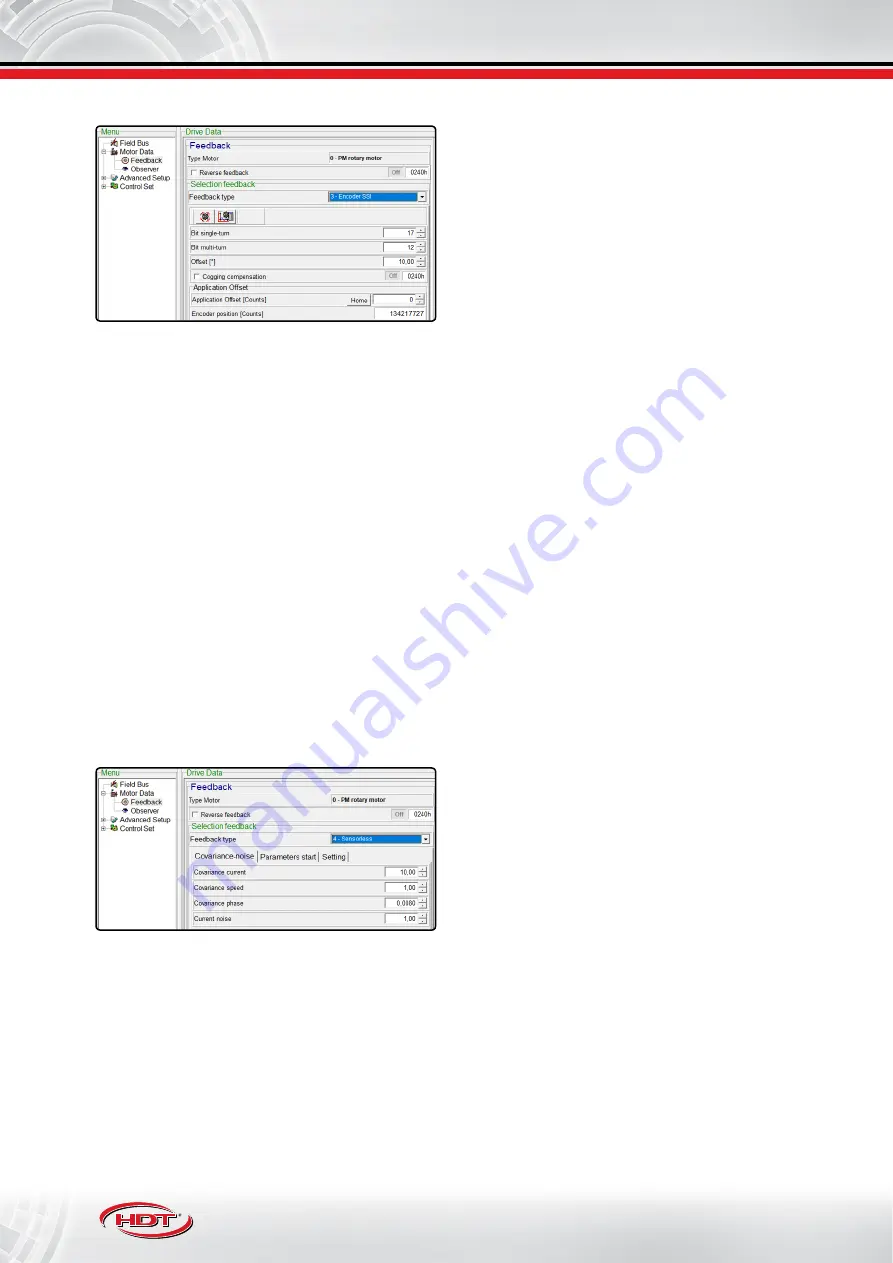
58
Installation and user guide
Rev: 4.0
NTT 240/460
Operation mode
6.03.2.g
SSI absolute encoder
It’s necessary to set correctly:
•
Bit single-Turn
•
Bit multi-Turn
(if present).
•
Offset
: offset encoder.
Other parameters are:
•
Reverse Feedback
: encoder counter is reversed related to
motor rotation.
•
Cogging compensation
: motor cogging mapping.
If SSI absolute encoder is used, it’s mandatory to correctly set offset-encoder parameter, set to 0° for all H.D.T.
motors; otherwise, perform the autophasing procedure if third part motor is used (
).
For single-turn absolute encoders, set
Bit multi-Turn
to 0.
It’s possible to set the “application offset” parameter related to encoder absolute 0 position: keep motor on desired
position and press ‘Home’ key into sub-menu
Feedback
inside
Drive Data
, to store the offset (this parameter is
mapped in every operation mode supported).
Besides, it’s possible to connect encoders having single-turn and multi-turn resolutions higher than 16bit and
15bit respectively; if single-turn and multi-turn bit sum is higher than 31bit, drive provides an error. If single-
turn bit are higher than 16bit, drive performs an automatic truncation of excess bits; by the way drive operates
correctly, affecting offered resolution, limiting it to 16bit. Istantaneous real value for encoder absolute position is
always visible.
Motor cogging map is available.
Connection is located into J5 connector (please see
“5.08 J5 connector: Feedback 1” pag. 36
):
1. V power to the feedback of used motor: +V (pin 10) and 0L (pin 11) and sensing pin if available (pin
9-18), otherwise leave them not connected for feedback at +5V or short-circuit them for feedback up to +9V.
2. connect signals: CK+ (pin 5), CK - (pin 6), D - (pin 12) e D+ (pin 13).
3. if available, it’s possible to connect the incremental signals: A+ (pin 1), A- (pin 2), B+ (pin 3), B- (pin 4).
4. if available, connect motor temperature sensor PTC (pin 7-8).
6.03.2.h
Sensorless
It’s necessary to perform a correct sensorless tuning to
obtain desired performances for applications.
Other parameters are:
•
Reverse Feedback
: encoder counter is reversed related to
motor rotation.
If brushless encoder is used, drive performs a start procedure with V/hz sensorless control to engage rotor position;
then predictive FOC control is used.
If asynchronous motor is used start procedureis not managed.
All sub-window include sensorless parameters usefull for motor regulation and application desired performances:
•
current, speed and phase covariance.
•
current noise.
•
start procedure set.
•
zero crossing speed and rotor lock current parameters.
For further information about sensorless loop tuning, please see
Содержание NTT 240
Страница 129: ......