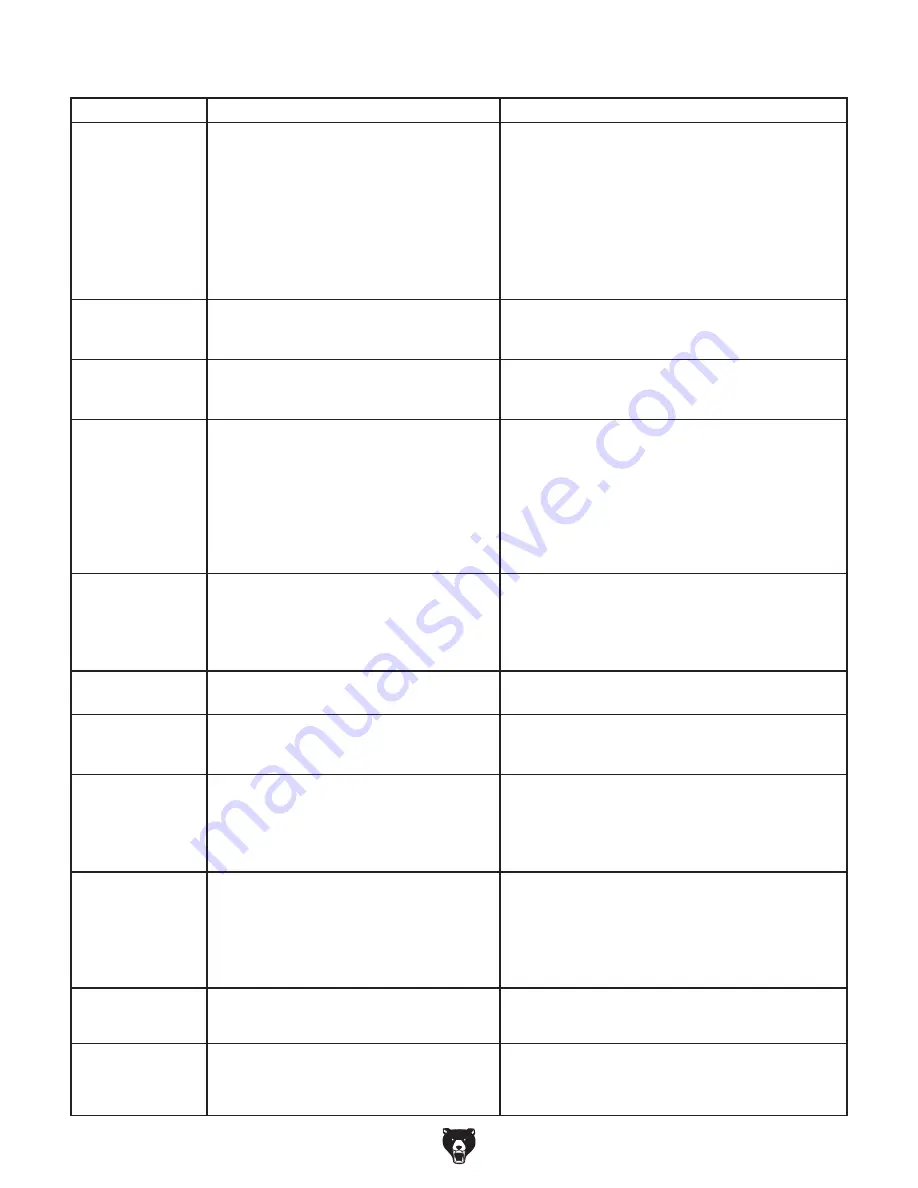
-58-
Model G0841 (Mfd. Since 06/18)
Operations (continued)
Symptom
Possible Cause
Possible Solution
Excessive snipe
(gouge at the end of
the workpiece that is
uneven with the rest
of the cut).
Note:
A small
amount of snipe is
inevitable with all
types of planers.
1. Workpiece not properly supported as it
leaves planer.
2. Chip breaker and/or pressure bar too low.
3. Lower pressure roller(s) too high.
4. Some snipe is inevitable.
1. Ensure workpiece remains properly supported until
cutting operation is complete; use roller stand with
extra long workpieces.
3. Check/adjust chip breaker (
Page 73) and/or
pressure bar (
Page 74) height.
3. Check/adjust lower pressure roller(s) height
(
Page 76).
4. Plane stock longer than your intended workpiece
length, then cut off excess after planing complete.
Uneven cut across
entire bottom side of
workpiece.
1. Lower cutterhead not parallel with table.
2. Lower pressure roller(s) not parallel with
table.
1. Check/align lower cutterhead height (
Page 64).
2. Check/adjust lower pressure roller(s) height
(
Page 76).
Uneven cut across
entire top side of
workpiece.
1. Upper cutterhead not parallel with table.
2. Idler roller and/or serrated roller not parallel
with table.
1. Square headstock (
Page 68).
2. Check/adjust idler roller (
Page 71) and/or serrated
roller (
Page 72) height.
Workpiece
chipping, tear-out,
indentations, or
overall rough cuts.
1. Workpiece not suitable for planing.
2. Operator not feeding workpiece to cut
"with" the grain.
3. Excessive feed rate.
4. Excessive depth of cut.
5. Dull inserts.
6. Dust collection problems.
1. Ensure workpiece is suitable for planing (
Page 34).
2. Turn the workpiece 180° before feeding again.
3. Reduce feed rate.
4. Reduce depth of cut.
5. Rotate/replace inserts (
Page 42).
6. Clear blockages, seal leaks, move machine closer
to dust collector, upgrade dust collector.
Chipping (consistent
pattern).
1. Knots or conflicting grain direction in wood.
2. Excessive depth of cut.
3. Nicked or chipped inserts.
1. Inspect workpiece for knots and grain direction; only
use clean stock, and cut WITH the grain.
2. Reduce depth of cut. (Hardwoods require a
shallower depth of cut than soft woods.)
3. Rotate/replace inserts (
Page 42).
Chipping (incon-
sistent pattern).
1. Chips not properly expelled from around
cutterhead(s).
1. Ensure required CFM at dust ports; clean chips
away from cutterhead(s).
Fuzzy grain in
workpiece.
1. Wood has high moisture content.
2. Dull inserts.
1. Ensure wood moisture content is less than 20%.
Allow to dry if necessary.
2. Rotate/replace inserts (
Page 42).
Long lines or ridges
that run along the
length of the board.
1. Nicked or chipped inserts.
2. Loose or incorrectly installed insert(s).
3. Dirt or debris under inserts.
1. Rotate/replace inserts (
Page 42).
2. Remove/replace insert(s) and install properly
(
Page 42).
3. Remove inserts, properly clean mounting pocket
and re-install (
Page 42).
Uneven cutter
marks, wavy
surface, or chatter
marks across face
of workpiece.
1. Excessive feed rate.
2. Inserts not consistently tightened/torqued.
3. Dirt or debris under inserts.
4. Worn cutterhead bearings.
1. Reduce feed rate.
2. Tighten/torque all inserts consistently when securing
(
Page 42).
3. Remove inserts, properly clean mounting pocket
and re-install (
Page 42).
4. Replace cutterhead bearings.
Glossy surface;
scorching or burn
marks on workpiece.
1. Feed rate too slow.
2. Dull inserts.
1. Increase feed rate.
2. Rotate/replace inserts (
Page 42).
Workpiece remains
concave or convex
along its length after
planing.
1. Workpiece excessively bowed or warped,
and is not suitable for planing.
1. Ensure workpiece is suitable for planing (
Page 34).
Содержание G0841
Страница 84: ......