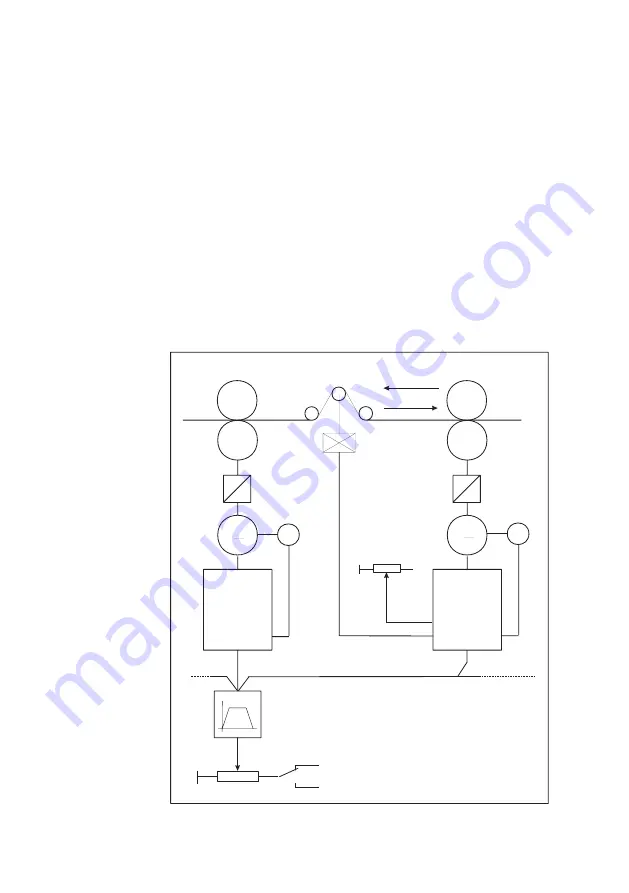
Chapter 7 Appendix • 330
ARTDrive V2 series - Instruction Manual
With such a configuration and having a proportional correction of the line
speed, the PI Block can not position the dancer when the machine is
stopped. In order to carry out the initial phase when the machine is stopped,
it is necessary to act on the PD block.
Set
PD P1 gain %
with a value allowing to position the dancer without big
dynamic stresses.
For example:
PD P1 gain %
= 1%
Use the derivative component as a system “damping” element by setting for
example:
PD D1 gain %
= 1 %
PD der filter
= 20 ms
If it is not needed, leave these parameters = 0.
In case a series of cascade references has to be performed for another
possible Drive, set
PID out mon
on an analog output, for example:
An out 1 src
=
PID out mon
7.5.2 Control of Nip Rolls with Loading Cell
M
M
E
E
0....+10V
+10V
-10V
Feed-forward
Feed-back
-10V
Set
Load cell
Reverse
Forward
Tension set
Forward
Reverse
Line speed
reference
(Internal ramp
master drive)
DRIVE
DRIVE
Line speed
Master
Nip-roll
Figure 7.5.2: Control of Nip Rolls with Loading Cell
Содержание ARTDrive Vector V2 400Vac Series
Страница 1: ...Instruction Manual ARTDrive ARTDrive Vector AC Drives V2 series 400Vac Class 575Vac Class...
Страница 14: ...0 14 Chapter 0 Safety Precautions ARTDrive V2 series Instruction manual...
Страница 40: ...40 Chapter 3 Installation Guidelines ARTDrive V2 series Instruction Manual...
Страница 92: ...92 Chapter 5 Quick Start Up Guide ARTDrive V2 series Instruction Manual...
Страница 358: ...358 Chapter 8 Appendix ARTDrive V2 series Instruction Manual...
Страница 376: ...Chapter 9 Pick Lists 376 ARTDrive V2 series Instruction manual...