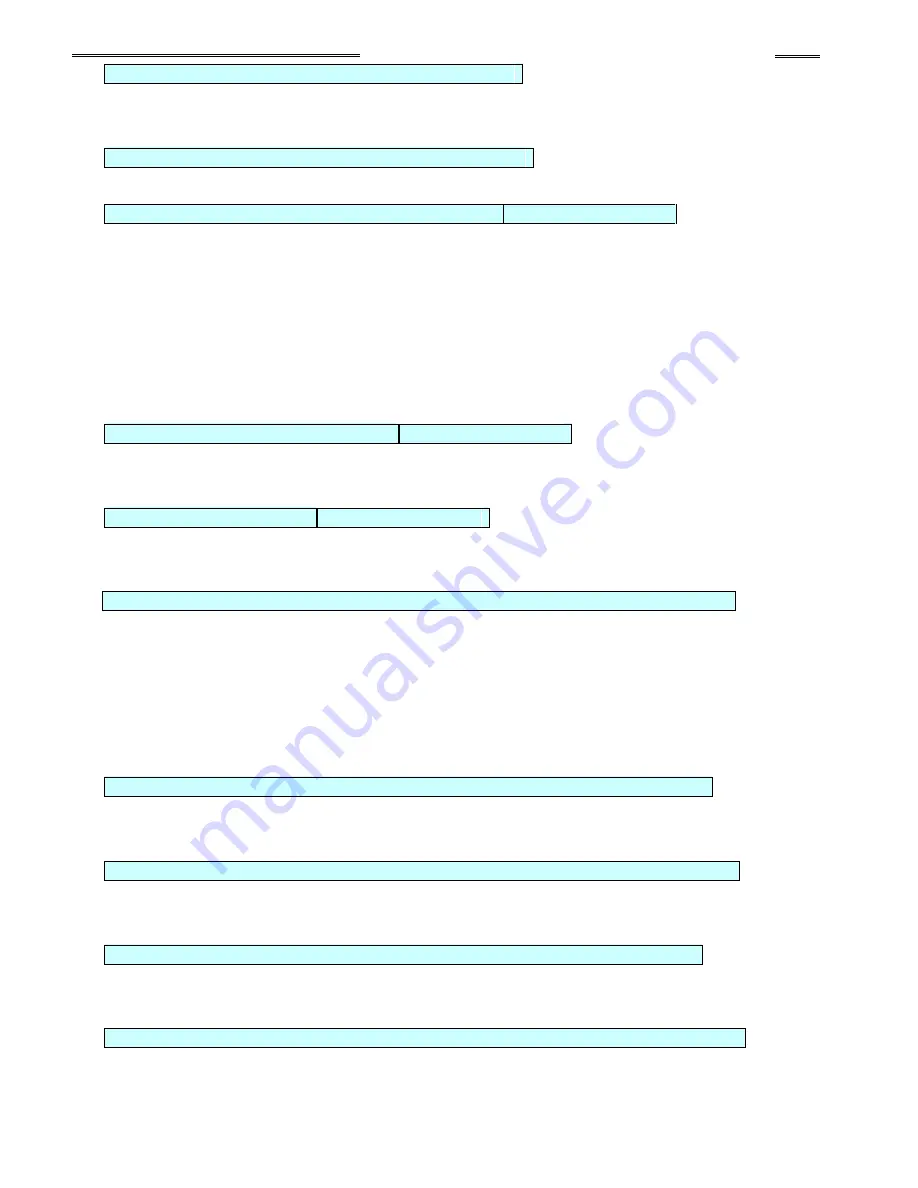
Chapter 5
I/O
Expansion Unit
Page 5-15
REJECT No. # (1 to 32): REJECT Signal of Spindle 1-32
Output when the fastening result is a REJECT. Indicates that the spindle is within fastening limits.
This output remains active until the START signal or RESET signal is input.
BYPASS No. # (1 to 32): BYPASS Signal of Spindle 1-32
Output when the spindle is in BYPASS.
ABNORMAL No. # (1 to 32): System Error/Abnormal Signal of Spindle 1-32
Output when an Abnormal condition occurs. This signal indicates that the System has detected an
internal fault, and can no longer proceed. The fault maybe generated from a connected spindle
during a self-check function. Check the individual spindle status to identify which spindle is reporting
the abnormal condition. (see AFC1500 Operation Manual for troubleshooting) The spindle reporting
an abnormal may be bypassed to resume normal operation, however, the bypassed spindle will be
ignored and not run while in bypass. An Abnormal condition must be corrected before the System
will resume normal operation. The RESET signal clears the abnormal condition
.
READY No. # (1 to 32): Input Enabling Signal of Spindle 1-32
Output when the spindle is in the READY condition. Indicates spindle is ready to operate and inputs
are enabled. This signal is inactive (off) when the BUSY output is active (on)
.
BUSY No. # (1 to 32): Busy Signal of Spindle 1-32
Output after a START signal is received, and remains active until the fastening cycle is complete and
the READY signal is output.
CURRENT WARNING No. # (1 to 32): Current Value Error Warning
Signal of Spindle 1-32
Active when the high current limit has been exceeded. This can be used to identify potential motor
failure before total failure occurs by identifying high current draws over what the typical current draw
is for the application.
Is “ON” when the controller current falls outside the range of the fastening parameter D-No. 522 “High
Current Limit” or the fastening parameter D-No. 521 “Low Current Limit” at the end of fastening.
CAL WARNING No. # (1 to 32): CAL Voltage Error Warning Signal of Spindle 1-32
This is output when a CAL voltage error has occurred in any of the controllers during a CAL check
(When CAL button is pushed or at start of cycle)
ZERO LEVEL WARNING No. # (1 to 32): ZERO Voltage Warning Signal of Spindle 1-32
This is output when a ZERO voltage error has occurred in any of the controllers during a self check
check (When CAL button is pushed or at start of cycle)
SNUG TQ HI REJ No. # (1 to 32): Snug Torque High Limit Signal of Spindle 1-32
The signal is set “ON” if the value of the Snug torque exceeds the fastening parameter D-No. 108
“Snug Torque High Limit.”
REVO. HI REJ. No. # (1 to 32): Rundown Revolution High Limit Signal of Spindle 1-32
The signal is set “ON” if the value of the rundown revolutions exceeds the fastening parameter D-No.
504 “Rundown Revolution High Limit.”
Содержание AFC3000
Страница 1: ...AFC3000E HW 1 ...
Страница 17: ......
Страница 18: ...Chapter 1 Outline PAGE 1 1 Chapter 1 Outline 1 ...
Страница 25: ......
Страница 26: ...Chapter 2 Specifications PAGE 2 1 Chapter 2 Specifications 2 ...
Страница 34: ...Chapter 3 System Description PAGE 3 1 Chapter 3 System Description 3 ...
Страница 64: ...Chapter 4 Installation and Wiring PAGE 4 1 Chapter 4 Installation and Wiring 4 ...
Страница 131: ...Chapter 4 Installation and Wiring PAGE 4 68 Blank Page ...
Страница 132: ...Chapter 5 I O Expansion Unit Page 5 1 Chapter 5 I O Expansion Unit 5 ...
Страница 164: ...Chapter 6 Power up and Initial Checks PAGE 6 1 Chapter 6 Power Up and Initial Checks 6 ...
Страница 168: ...Chapter 7 Fastening Instructions PAGE 7 1 Chapter 7 Fastening Instructions 7 ...
Страница 207: ... Blank Page ...
Страница 208: ...Chapter 8 System Operation PAGE 8 1 Chapter 8 System Operation 8 ...
Страница 259: ...Chapter 8 System Operation PAGE 8 52 ...
Страница 260: ...Chapter 9 Maintenance Inspection PAGE 9 1 Chapter 9 Maintenance Inspection 9 ...
Страница 268: ...Chapter 10 Troubleshooting PAGE 10 1 Chapter 10 Troubleshooting 10 ...
Страница 294: ......