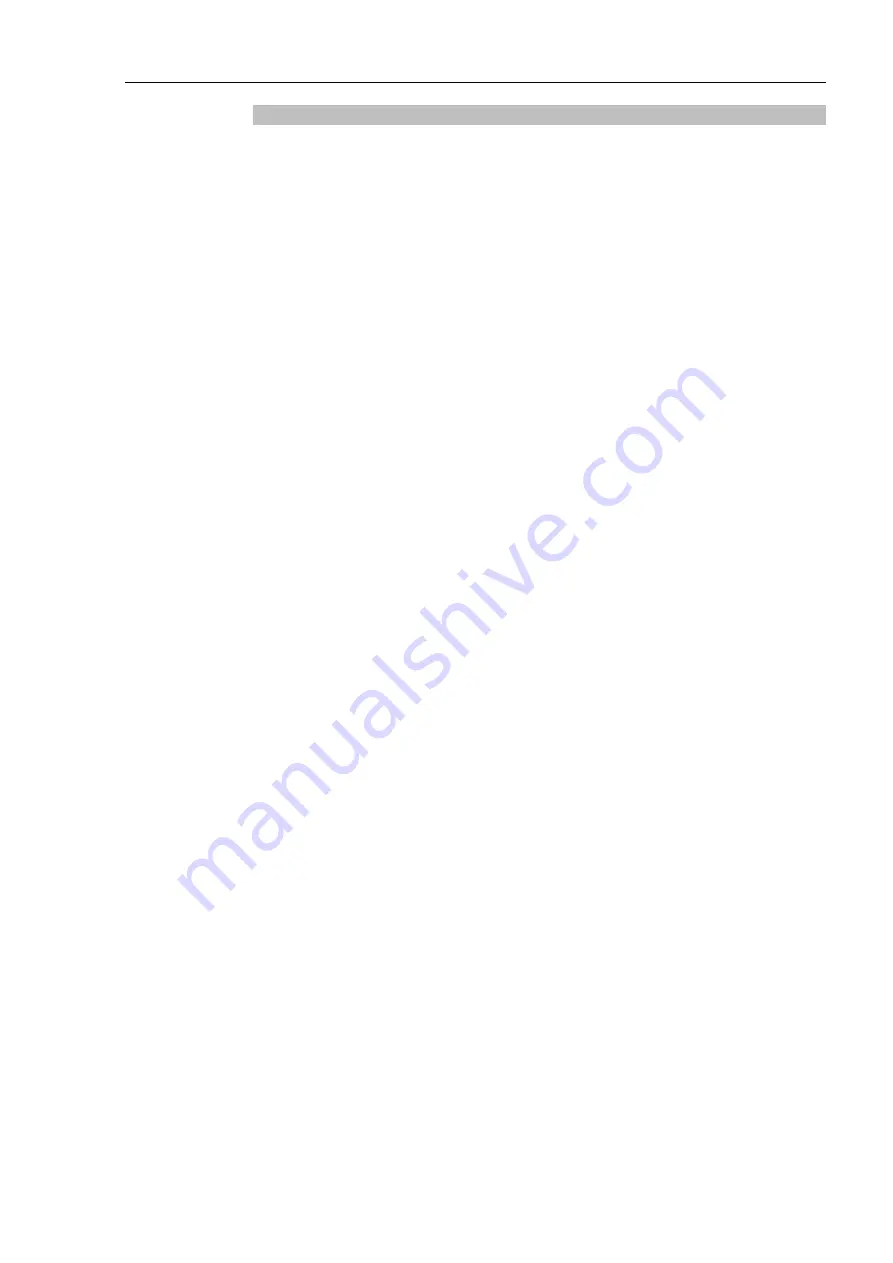
Installation 2. Installation
RC700-D Rev.2
21
2.6.7 Emergency Stop
Each robot system needs equipment that will allow the operator to immediately stop the
system’s operation. Install an emergency stop device that utilizes emergency stop input
from the Controller and all other equipment.
Use the emergency switch which has safety function more than PLd.
The safety function of Emergency Stop Input: Category 3, PLd (reference ISO13849-1
2015)
The Stop category of Emergency Stop Input: Category 1 (reference IEC60204-1 2016)
The controller is equipped with an emergency stop input terminal. If the normally closed
emergency stop circuit is broken, the control is stopped. Then the power supplied to all motors
will be shut off.
The path that the robot will follow from the time the emergency stop switch is pressed until
the device stops, as well as the stop position itself, cannot be positively determined.
In many cases, the stop position will not exceed the target position for the operation prior
the emergency stop. Depending on the robot’s loading condition and operation speed,
overruns are inevitable. Taking this into consideration, be sure the layout for the peripheral
equipment includes extra space.
The emergency stop circuit should also remove power from all external components that
must be turned off during an emergency. Do not assume that the robot controller will turn
off all outputs if configured to. For example, if an I/O card is faulty, the controller cannot
turn off a component connected to an output. The emergency stop on the controller is
hardwired to remove motor power from the robot, but not external power supplies.
However, do not press emergency stop switch during normal operation. Pressing
emergency stop switch may cause collision with the peripheral equipment because the
operation path of manipulator until stops is different from normal operation path.
Do not press the Emergency Stop switch unnecessarily while the Robot is operating.
Pressing the switch during the operation makes the brakes work. This will shorten the life
of the brakes due to the worn friction plates.
Normal brake life cycle: About 2 years (when the brakes are used 100 times/day)
Also, the Emergency Stop during operation applies impact on the reduction gear unit, and
it may result in the short life of the reduction gear unit.
Following may result in the short life when stopping the operation by pressing emergency
switch in the manipulator working properly.
Brakes
Reduction gear unit
To place the robot system in emergency mode during normal operation, press the
Emergency Stop switch while the Manipulator is not moving.
Refer to the Controller manual for instructions on how to wire the Emergency Stop switch
circuit.
Содержание RC700-D
Страница 1: ...Control Unit RC700 D Original instructions Rev 2 EM221C5146F ROBOT CONTROLLER RC700 D Manual ...
Страница 2: ...ROBOT CONTROLLER RC700 D Manual Rev 2 ...
Страница 8: ...vi RC700 D Rev 2 ...
Страница 16: ...Table of Contents xiv RC700 D Rev 2 ...
Страница 18: ......
Страница 80: ...Installation 5 Second Step 64 RC700 D Rev 2 ...
Страница 82: ......
Страница 87: ...Functions 1 Specifications RC700 D Rev 2 71 1 3 Outer Dimensions Unit mm ...
Страница 182: ...Functions 14 Option Slots 166 RC700 D Rev 2 14 8 6 Circuit Overview EUROMAP67 Board EUROMAP67 Board System diagram ...
Страница 190: ......
Страница 202: ...Regular Inspection 3 Alarm 186 RC700 D Rev 2 ...
Страница 203: ...187 Appendix ...
Страница 204: ......