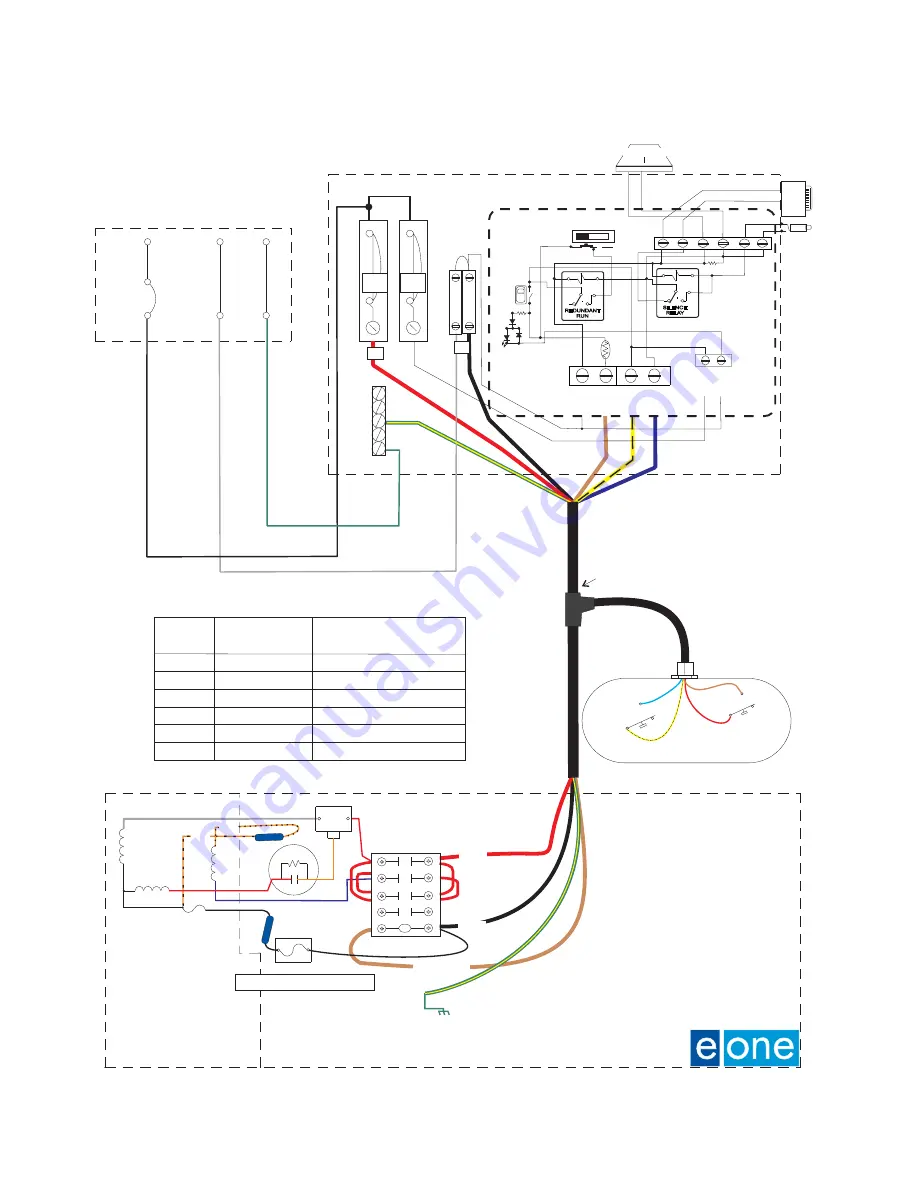
Troubleshooting 2–14
Figure 2-4b, Wiring Schematic, 120V, May 2015 & Earlier (Serial Number 531883)
CAPACITOR
BLEED
RESISTOR
MOTOR
COMPARTMENT
START
GRN-G
MAIN
MAIN
1
3
2
1
3
GRAY
RED
BLU
PROTECTOR
PROTECTOR
THERMAL
THERMAL
SWITCH
SMART
BLK
CONTROL COMPARTMENT
MOTOR section
CONTROL COMPARTMENT
COVER section
TO MOTOR
GROUND
MOTOR CONTACTOR
120 VOLT
GRINDER PUMP CORE
BRN-L1 Control
BLK-N
RED-L1
EQD
Pin #
Wire Color
Function
1
Brown
Manual Run
2
Red
L1
3
Black
Neutral
4
Ground
5
Yellow
Alarm Power Feed
6
Blue
Alarm Power Return
Green w/ Yellow Stripe
120VAC
NEUTRAL
L1
AMP
30
MAIN SUPPLY PANEL
N
G
120VAC 60Hz
SINGLE POLE - HARDWIRE
GROUND
(RECOMMENDED WIRING CONFIG,
NOT SUPPLIED BY E/ONE)
PUMP
BREAKER
20
15
ALARM
BREAKER
L1
N
YEL
ORN
Note: “A1” & “A2” are
for the contactor coil
1
3
2
(ALARM)
SWITCH
2
1
3
(ON-OFF)
SWITCH
Level Control Compartment
Tray Cable
HARD WIRE OPTION
Alarm Yellow and Blue wires go to the alarm panel only
Motor Control Red and Brown wires go to both alarm panel and motor contactor
ALARM LAMP
REDUNDANT
RUN
COIL
COM
N.O.
N.C.
Basic Alarm
Board
(PC1139G01)
SILENCE
RELAY
COIL
COM
N.O.
N.C.
PTC
RESIST
OR
AUT
O-RESET
FUSE
Resistor
LED
GREEN
RUN
SER
VICE
NEUTRAL
MANUAL
RUN
ALARM
FEED
ALARM
RETURN
BUZZER
SILENCE
SWITCH
MANUAL
RUN
SW
.
Resistor
PUMP
L2
ALARM
L1
WIRED
WIRELESS
LEVEL CONTROL
ALARM/DISCONNECT
Using the EXTREME color Scheme
NA0035P12 REV. A
2
4
6
14
A2
T1
T2
T3
NO
A1
13
5
3
1
NO
I3
L2
L1
Содержание Extreme Series
Страница 1: ...Service Manual E One Extreme Grinder Pumps 240V 60 Hz Hardwired Controls...
Страница 2: ......
Страница 32: ...Pump End 5 8 Figure 5 9a D Series Pump Exploded View...
Страница 33: ...Pump End 5 9 Figure 5 9b W Series Pump Exploded View...
Страница 34: ...Pump End 5 10 Figure 5 9c Gatorgrinder GH Series Pump Exploded View...
Страница 35: ...Pump End 5 11 Figure 5 9d IH091 Pump Exploded View...
Страница 36: ...Pump End 5 12...
Страница 58: ...Level Sensor 8 10 Figure 8 35 Level Sensor Assembly Exploded View all hardwired pumps...
Страница 70: ...Mechanical Seal Assembly 11 2...
Страница 75: ......