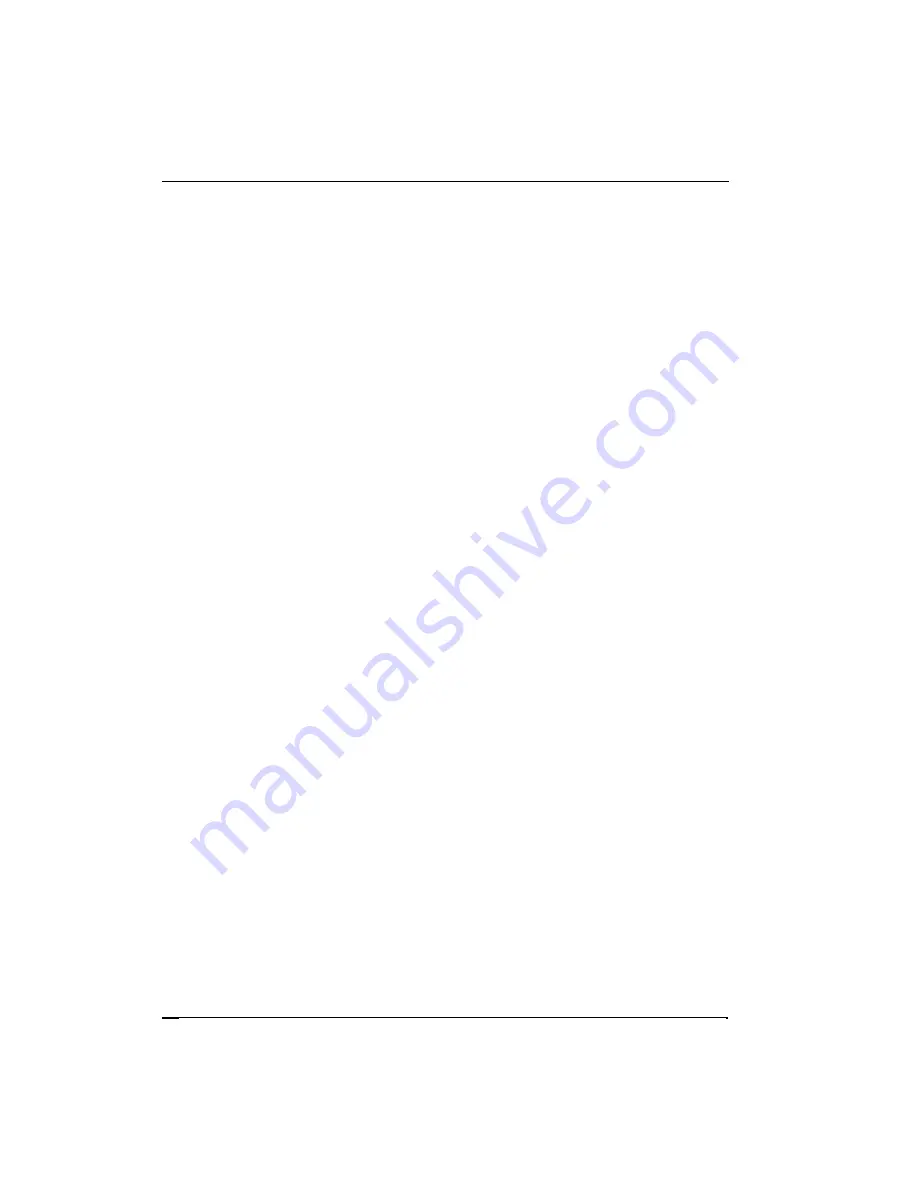
Cryo-con Model 24C
Basic Setup and Operation
Autotuning
The Autotune Process
In performing autotuning, the Model 24C applies a generated waveform to the heater
output and analyzes the resulting changes in process temperature. This is used to
develop a process model, then a PID solution.
It is important to note that a range of PID combinations exist, which provide accurate
control for a given process. Furthermore, process modeling is a statistical method
affected by noise and system non-linearity.
Consequently, multiple autotuning of the same process may yield different results.
However, if the process model has not corrupted, any of the generated results will
provide equally stable temperature control.
For further explanation, the different PID solutions generated by autotuning vary only
in the resultant closed loop bandwidth. Low bandwidth solutions are slower to
respond to changes in setpoint or load disturbances. High bandwidth solutions are
responsive but can exhibit overshoot and damped oscillation.
The Model 24C attempts to generate minimum overshoot solutions since many
cryogenic temperature control applications require this. If the process is noisy,
bandwidth is minimized as much as possible. If the process is very quiet, a more
aggressive solution is generated subject to the minimum overshoot requirement.
The autotune algorithm produces a heater output waveform in order to force the
process model to converge. In general, a large amplitude waveform will provide the
best possible signal-to-noise ratio, resulting in a faster and more accurate solution.
However, it is important in some systems for the user to constrain the amplitude and
duration of the heater output waveform by using the DeltaP and Timeout parameters.
Small values for DeltaP force the use of small changes in heater power. This makes
the process model more susceptible to corruption by noise.
Large values of DeltaP will allow the use of large heater power swings, but this may
also drive the process into non-linear operation, which also corrupts the tuning result.
Worse, it may allow the application of too much heater power, which causes an over
temperature condition.
Experience indicates that most cryogenic systems autotune properly using a DeltaP
of 5% whereas a noisy system requires 10% or more. A common example of a noisy
cryogenic system is one where a Silicon diode sensor is used with a setpoint near
room temperature.
80