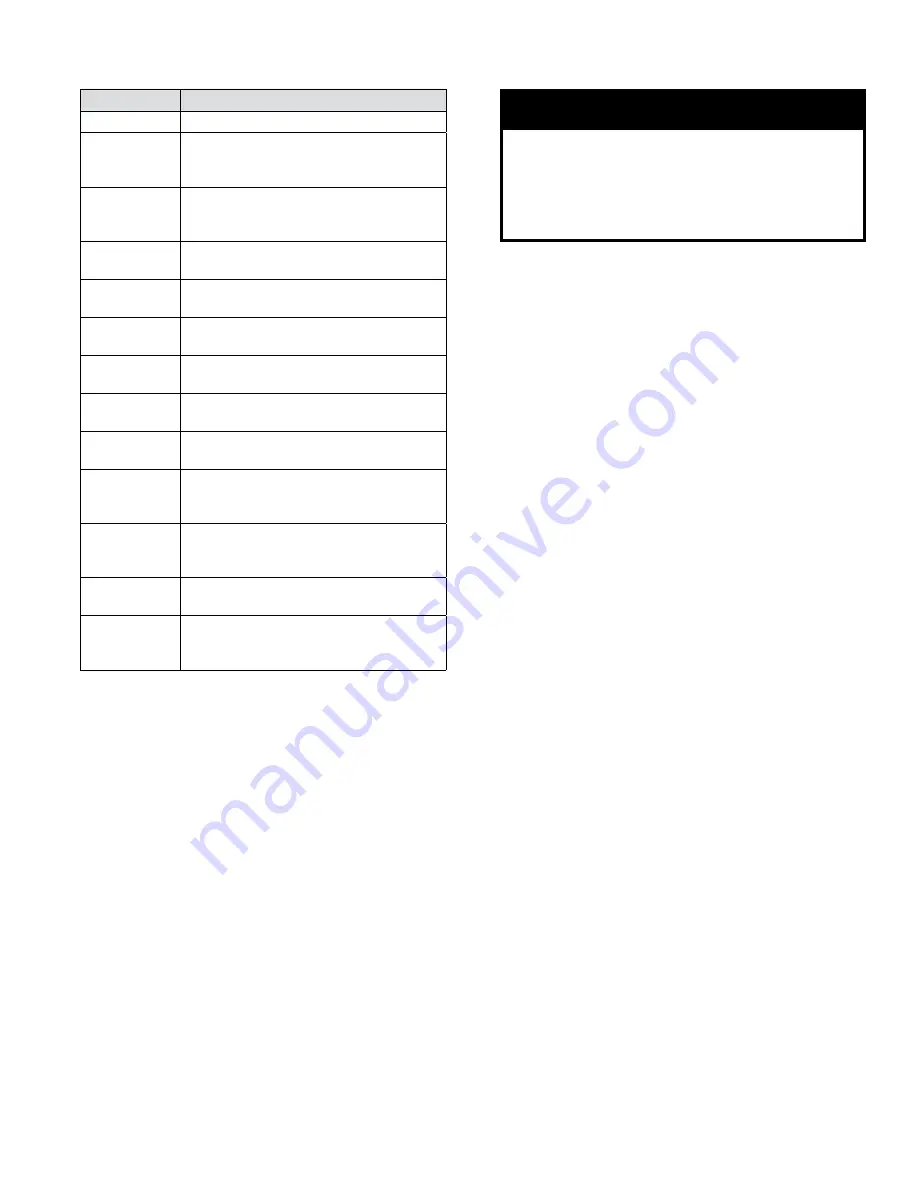
77
H.
Purge Air From Gas Train
Upon initial start-up, the gas train will be filled with air.
Even if the gas line has been completely purged of air,
it may take several tries for ignition before a flame is
established. If more than 5 tries for ignition are needed,
it will be necessary to press the reset button to restart
the boiler. Once a flame has been established for the
first time, subsequent calls for burner operation should
result in a flame on the first try.
I.
Check Burner Flame
Inspect the flame visible through the window. On high
fire the flame should be stable and mostly blue (Figure
52). No yellow tipping should be present; however,
intermittent flecks of yellow and orange in the flame are
normal.
J.
Check Gas Inlet Pressure
Check the inlet pressure and adjust if necessary. Verify
that the inlet pressure is between the upper and lower
limits shown on the rating plate with all gas appliances
on and off.
Warning
The outlet pressure for the gas valve has been
factory set and requires no field adjustment. This
setting is satisfactory for both natural gas and
propane. attempting to adjust the outlet pressure
may result in damage to the gas valve and cause
property damage, personal injury or loss of life.
K.
For LP Gas,
perform procedure as described in
Paragraph R “Field Conversion From Natural Gas to LP
Gas” before starting Paragraph L “Checking/Adjusting
Gas Input Rate”.
For natural gas
, proceed to Paragraph L “Checking/
Adjusting Gas Input Rate”.
L.
Checking /Adjusting Gas Input Rate
1. Turn off gas supply to all appliances other than gas-
fired boiler.
2. Light main burner by adjusting thermostat to highest
setting.
3. Clock gas meter for at least two (2) revolutions
of the dial typically labeled ½ or 1 cubic foot per
revolution on a typical gas meter.
4. Determine gas flow rate in Cubic Feet per Hour
based on elapsed time for two revolutions.
Example:
Using a meter with dial labeled 1 cubic foot per
revolution, measured time is 72 Seconds for (2)
Revolutions, i.e. 36 seconds per 1 cubic foot.
Calculate hourly gas flow rate:
3600 sec/hr
÷
36 sec/cu ft = 100 cu ft/hr
5. Obtain gas-heating value (Btu per cubic foot) from
gas supplier.
6. Multiply hourly gas flow rate by gas heating value
to determine the boiler input rate, BTU/hr
Example:
Natural gas heating value provided by local gas
utility is 1050 Btu per cubic foot.
Measured and calculated hourly gas flow rate is 100
cu ft/hr.
Measured boiler input rate is:
100 cu ft/hr * 1050 BTU/ cu ft = 105, 000 BTU/hr
7. Compare measured input rate to input rate value
stated on rating label. Strive to adjust the boiler
input rate within 88% to 100% of the value listed on
the boiler rating label.
8. If measured input is too high, reduce input rate by
rotating gas valve throttle screw clockwise (see
Figure 53) in ¼ turn increments and checking the
rate after every adjustment until the measured
input rate value falls within 88% to 100% of the
iX. System Start-up
(continued)
Status
Control action
Initiate
Power-up
Standby Delay
This state is entered when a delay is
needed before allowing the burner control
to be available and for sensor errors.
Standby
Boiler is not firing. There is no call for
heat or there is a call for heat and the
temperature is greater than setpoint.
Safe Startup
Tests flame circuit then checks for flame
signal.
Drive Purge
Driving blower to purge rate setting and
waiting for the proper fan feedback.
Prepurge
Purges the combustion chamber for the
10 second purge time.
Drive Light-off Driving blower to light-off rate setting and
waiting for the proper fan feedback.
Pre-ignition
Test
Tests the safety relay and verifies that
downstream contacts are off.
Pre-ignition
Energizes the igniter and checks for
flame.
Direct
Ignition
Opens main fuel valve and attempts
to ignite the main fuel directly from the
ignition source.
Running
Normal boiler operation. Modulation rate
depends on temperature and setpoint
selections and modulating control action.
Postpurge
Purges the combustion chamber for the
30 second purge time.
Lockout
Prevents system from running due to a
detected problem and records fault in
Lockout History.
Содержание Apex APX399
Страница 7: ...7 I Product Description Specifications and Dimensional Data continued Figure 1A Apex Model APX399 ...
Страница 8: ...8 Figure 1B Apex Model APX500 I Product Description Specifications and Dimensional Data continued ...
Страница 9: ...9 I Product Description Specifications and Dimensional Data continued Figure 1C Apex Model APX800 ...
Страница 65: ...65 VIII Electrical continued Figure 43 Ladder Diagram ...
Страница 66: ...66 VIII Electrical continued ...
Страница 67: ...67 Figure 44 Wiring Connections Diagram VIII Electrical continued ...
Страница 110: ...110 1P 3 1P 2 1P 1 XIII Repair Parts continued 1C 1D 1E ...
Страница 116: ...116 XIII Repair Parts continued ...
Страница 118: ...118 XIII Repair Parts continued ...
Страница 129: ...129 SERVICE RECORD DATE SERVICE PERFORMED ...
Страница 130: ...130 SERVICE RECORD DATE SERVICE PERFORMED ...
Страница 131: ...131 SERVICE RECORD DATE SERVICE PERFORMED ...