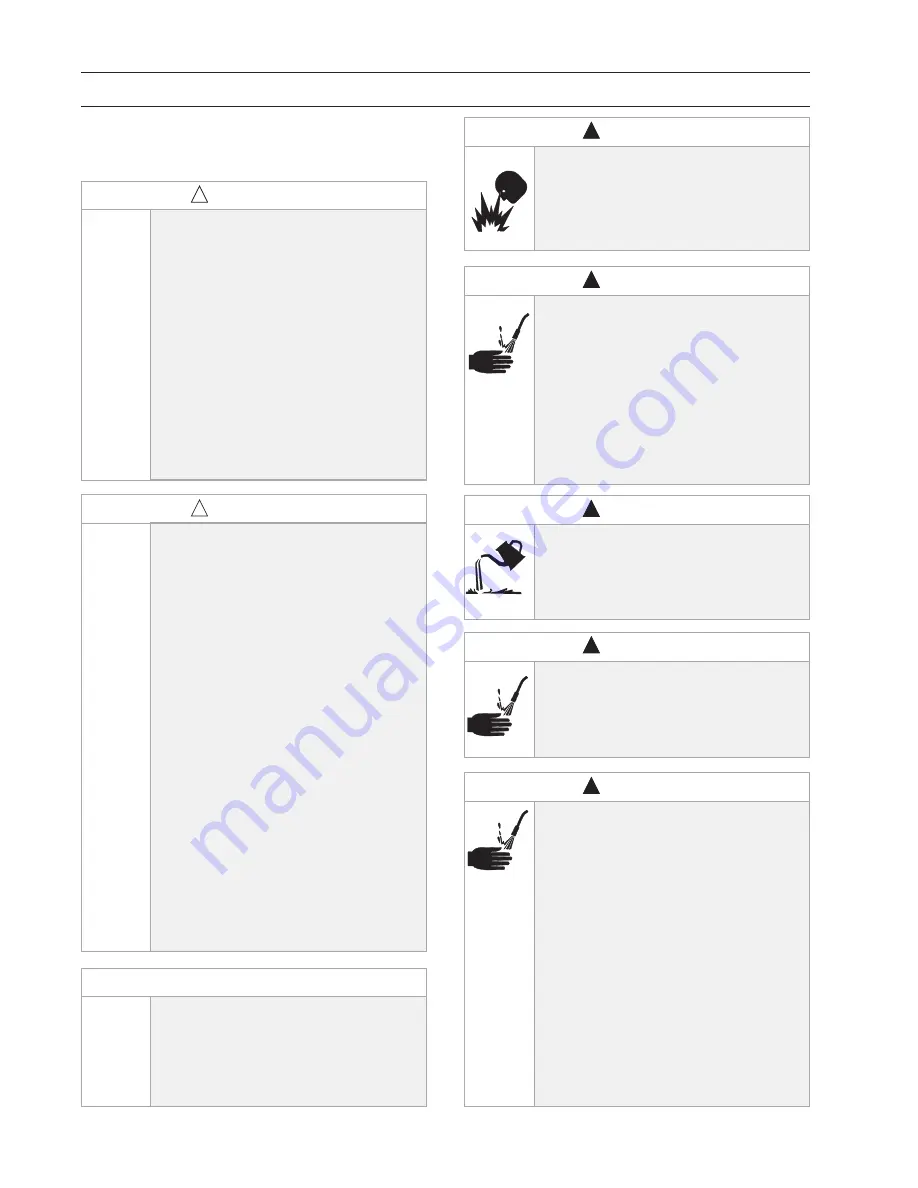
Page 2
Safety:
General Notes, Warnings, and Precautions
Thoroughly read and understand this manual before
installing, operating or servicing described equip-
ment.
DANGER: Not for use with fl uids that
have a fl ash point below 100 Deg F (38
Deg C, examples: gasoline, alcohol).
Sparking could result in an explosion
which could result in death.
!
WARNING
Turn off power at the Queuing Console
TM
at the end of each workday to eliminate
the hazard of oil spills during unattended
periods.
!
WARNING
Fluid emitted under high pressure from
leaks and/or ruptured components can
penetrate the skin and cause extremely
serious bodily injury. If any fl uid appears
to penetrate the skin, apply emergency
medical care at once. Do not treat the
penetration as a simple cut. Tell your
physician exactly what type of fl uid was
injected into your skin.
!
WARNING
!
Because The Spectrum
TM
System
controls pressurized oil delivery, the
following safety precautions should be
observed:
1) Check equipment regularly and repair
or replace worn and damaged parts. Be
sure fl uid connections are tight before
operating this equipment.
2) Adhere to limits of intended use as
described on page 4. Read all limitations
which apply to fl uid types, facility limits
and installation confi guration.
3) Relieve pressures built up in the
system before any service or repair is
begun. See pressure relief procedure,
this page.
4) Never alter or modify any parts of this
product; doing so may cause damage
and/or personal injury.
CAUTION
Failure to load fl uid meter calibration
factor (pulses per gallon) for each meter
into Spectrum
TM
operating software will
result in substantial dispense volume
errors. See pages 37-38.
NOTE
Do not place your hand or fi ngers over
the dispensing nozzle and/or aim the
nozzle at a person at any time. Personal
injury may result.
!
WARNING
Always use the following Pressure
Relief Procedure whenever shutting
off, cleaning, or in any way checking or
servicing pressurized components:
1) Disconnect compressed air line or
turn off power supply at the fl uid pump.
2) Point the control handle outlet into
a waste container and open trigger to
relieve pressure.
3) Open any bleed-type supply air
valves and fluid drain valves in the
system.
4) Leave the drain valves open until
you are ready to re-pressurize the
system.
!
WARNING
!
DO NOT TURN OFF CONSOLE IF
JOBS ARE IN QUEUE !
Doing so can result in error, “Station not
Available”. Before turning off power to
console, dispense all jobs or delete all
jobs in queue by using Basic Procedure
BP5: Job Deletion.
If “Station not Avaiable” message
appears, refer to Diagnostic Error Mes-
sage and Code (pg 55); “No Code”
“Station not Available” for recovery
procedures.
CAUTION