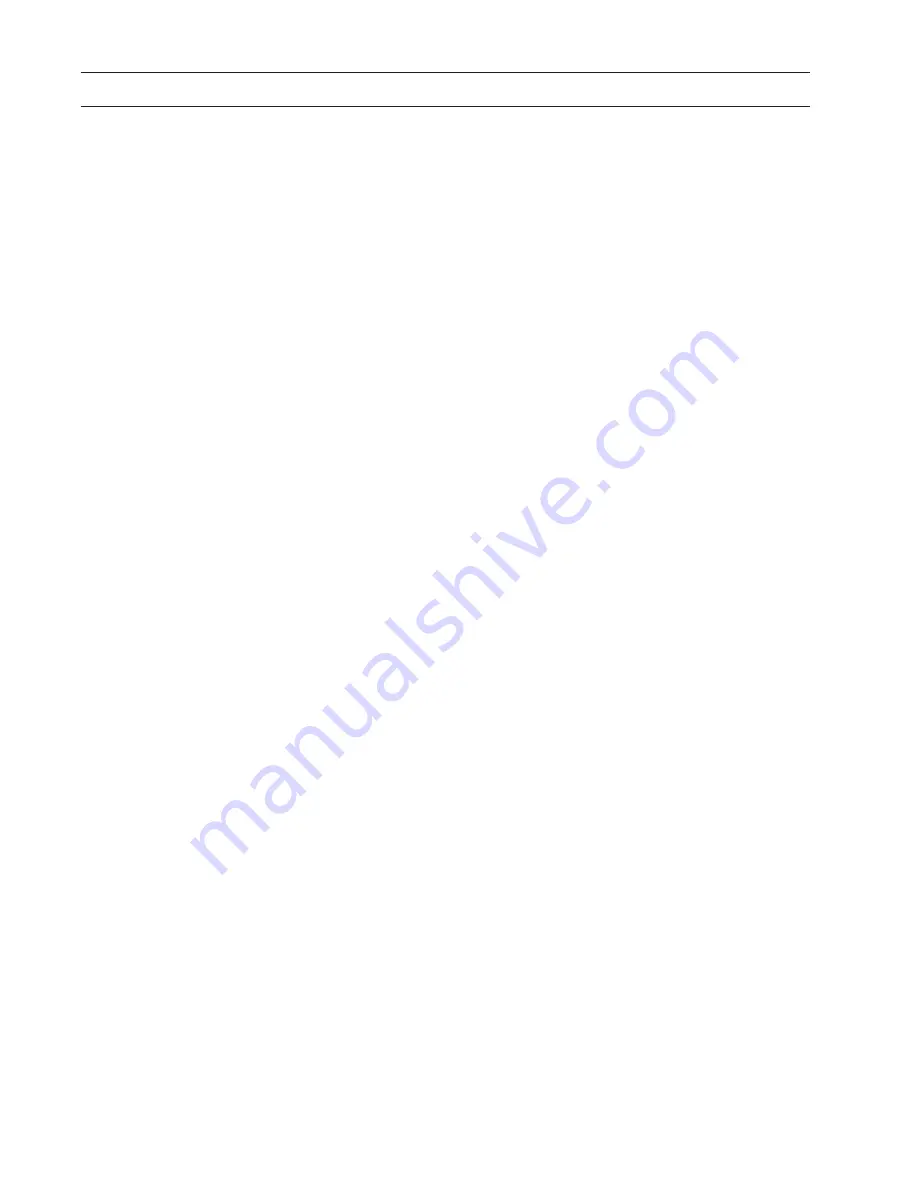
Page 64
Repair Procedures
(RP): System Repair or Expansion
1
Whenever error messages are displayed, imme-
diately write down each message exactly and in
complete form.
2
To determine corrective action, address each indi-
vidual message by referring to the troubleshooting
guide,
[pages 47-56]
and following recommended
procedures. Look for the error code in the message
and match it to an appropriate fl ow diagram.
3
An error message may be accompanied by the
prompt: “CONTINUE?; YES, NO”. Generally,
select yes. This will direct the Spectrum System to con-
tinue operation, but with the malfunctioning component
excluded. An
excluded
Smart Controller, for example,
will invoke the message “STATION NOT AVAILABLE”
if you attempt to dispense a job to one of its ports, but
will otherwise allow normal system operation until a
remedy is completed.
4
Some errors may be cleared by cycling power at
the console to restart the system. This should not
be attempted until a) all active dispense jobs are either
completed or cancelled, and b) an attempt is made to
repair the specifi c reported error per step 2.
5
Some errors may be cleared by re-loading the
console set-up from the Air Smart Controller by
completing the procedure, “System Confi guration”,
[Procedure SP6, Page 43]
.
6
If step 5 fails due to an unsuccessful down load
attempt, the entire system setup must be repeated
by completing the appropriate procedures [SP1
through SP6, pages 36-43]. Consult with Balcrank
customer service before taking this action.
RP16
Troubleshooting SC
Magnetic Polling Errors
1
Use a small magnet for the Smart Controller iden-
tifi cation process; magnets smaller than 1/2-inch
diameter x 3/4” long are preferred. Your Spectrum
Queuing Console is shipped with a screwdriver which
has a suitable magnet on the handle head.
2
Pass the magnet across the “sweet spot” on the
smart controller as shown in
[Figure 26, Page 20]
.
Keep the head of the magnet very close to the face of
the controller. Make multiple passes, back and forth,
until the controller’s center LED blinks twice.
3
Failure of Smart Controllers to respond to magnet
polling is almost always due to a faulty termination
in the Power/Communications cables. Refer to the
procedure “Verifi cation of Communications / Power
Wiring”,
[Procedure RP8, Page 62]
, to eliminate wiring
faults. All segments of Communications / Power Wiring
in the system should be reviewed, not just the wiring
near the problem controller.
4
It may be useful to set up Smart Controllers indi-
vidually using a ground level initializing technique.
Follow the written procedure, “Ground-Level SC
Identifi cation Process”,
[Procedure RP12, Page 64]
.
This method requires a more complex procedure, but
allows Smart Controller set-up which is not infl uenced
by wiring faults in the
Power/Communications cables.
It is therefore easier to isolate and correct installation
problems.
5
When all other methods have failed to allow mag-
netic identifi cation, then replace the Smart Control-
ler and continue with installation. However, remember
that defective Smart Controllers are very rare: the
cause of magnetic polling failure is almost always
associated with a correctable fault in the
Power/Com-
munications cables.
RP17
Troubleshooting
Dispense Quantity Errors
1
When evaluating dispensed amounts, use a
calibrated measuring container only, per “Required
Tools and Materials List”
[Page 12].
Do not use a
metered control handle as a comparison reference.
2
Be sure air is purged completely from the fl uid
lines in your system. Air in the fl uid will cause
incorrect meter readings, causing dispenses of less
than the authorized amount. Be sure the pump is
well-primed and the tank level is not too low. Be sure
all hand valves in the line are open and air is supplied
to the pump.
3
To evaluate dispense accuracy of one of the fl uids,
dispense one gallon of that fl uid into a certifi ed
accurate measuring container. If the dispense quantity