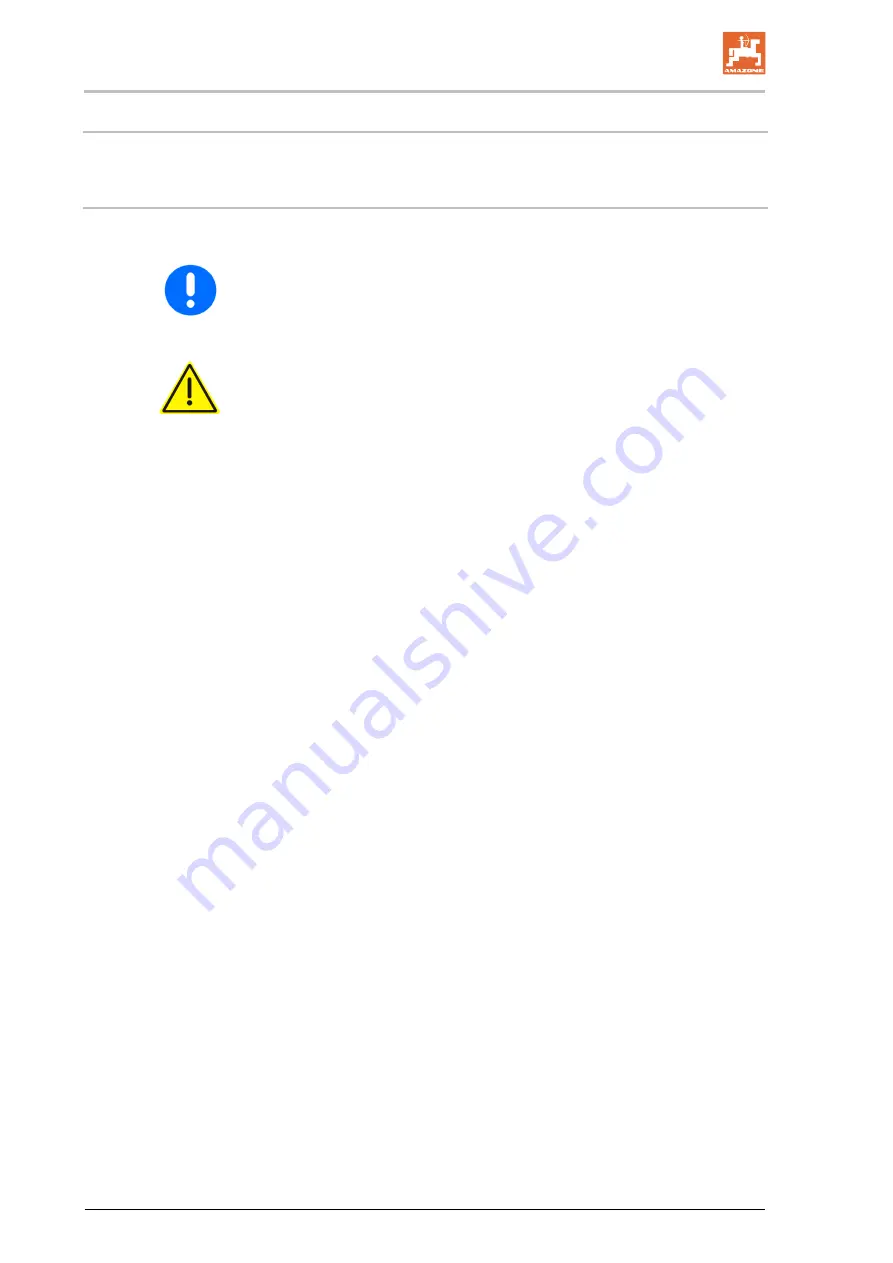
Maintenance and repairs
188
AD 3000 Super BAH0107-0 02.20
12.5
Maintenance
12.5.1 Visual inspection of the upper and lower link pins
Adhere to the inspection intervals,
see section "Maintenance schedule", page 175.
WARNING
Risk of contusions, catching, and knocks when the implement
unexpectedly releases from the tractor!
Check the upper and lower link pins for visible defects whenever the
implement is coupled.
Replace worn top and lower link pins.
Содержание AD 3000 Super Classic Line
Страница 2: ......
Страница 9: ...AD 3000 Super BAH0107 0 02 20 9 ...
Страница 77: ...Structure and function AD 3000 Super BAH0107 0 02 20 77 Fig 72 ...
Страница 196: ......
Страница 197: ......