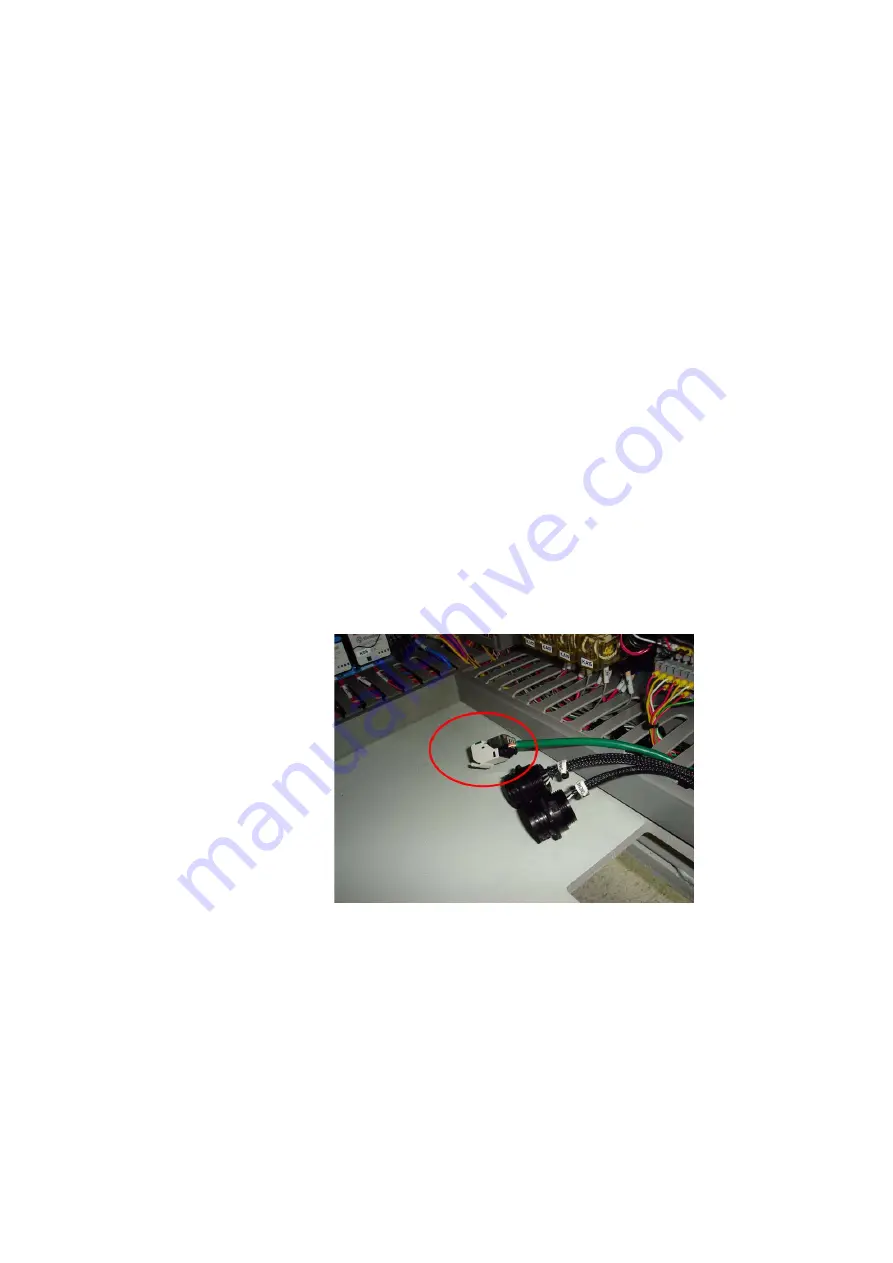
Introduction to the Medalist sj5000
2
Agilent U1840A Medalist sj5000 Hardware Manual
2-15
SMEMA Connections
The SMEMA interface ports are located inside the control panel
of the sj5000. The sj5000 comes equipped with two SMEMA
cables for each conveyor line to connect to equipment upstream
and downstream.
•
The upstream cable (p/n 5186-0614) must be connected to
the SMEMA UP connector.
•
The downstream cable (p/n 5186-0615) is connected to the
SMEMA DOWN connector.
These cables need to be routed through the cut-out at the base
of the system.
The upstream and downstream connections must be made for
the system to function correctly while operating single or dual
lane.
Network Connection (Optional)
If the networking option is included with your system, an RJ45
female connector is provided in the control panel for connecting
the sj5000 to a network.
Contact your system administrator for details of connecting the
sj5000 to the network.
Содержание U1840A Medalist sj5000
Страница 15: ...Safety and Regulatory Information 1 Agilent U1840A Medalist sj5000 Hardware Manual 1 9...
Страница 50: ...3 12 Agilent U1840A Medalist sj5000 Hardware Manual 3 Installation...
Страница 100: ...7 18 Agilent U1840A Medalist sj5000 Hardware Manual 7 Camera and Lighting Calibration...
Страница 134: ...10 18 Agilent U1840A Medalist sj5000 Hardware Manual 10 Setting Up Barcode Readers...
Страница 176: ...11 42 Agilent U1840A Medalist sj5000 Hardware Manual 11 Troubleshooting...
Страница 181: ...Maintenance 12 Agilent U1840A Medalist sj5000 Hardware Manual 12 5 Figure 12 2 Sensors on the conveyor...
Страница 190: ...A 4 Agilent U1840A Medalist sj5000 Hardware Manual A System Specifications...
Страница 192: ...B 2 Agilent U1840A Medalist sj5000 Hardware Manual B Reference Documents...