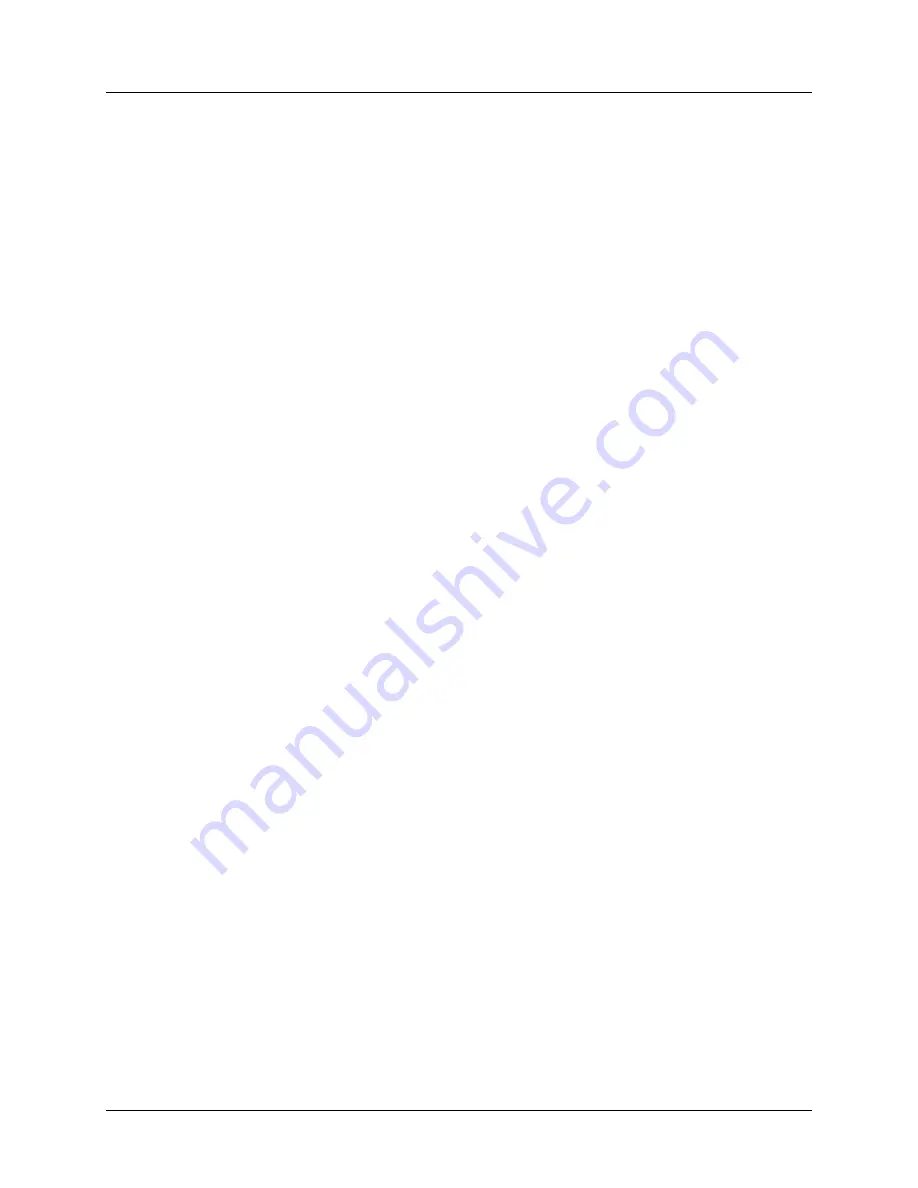
Installation & Operation Manual - Model AVR6000
Contents of this Manual are Subject to Change Without Notification
Page 29
6.5.3.1.6.1.1
AVR PI Control Loop Glossary of Terms
SETPOINT
: This is the setpoint value provided from the system application logic.
SETPOINT LIMITS
: The setpoint limits are values that are applied to the setpoint
to provide boundries that are not to be exceeded based on the design
requirements of the controlled space. The setpoint limits used for the airflow
control loops must be within the working range of the airflow control valve.
OFFSET
: The offset is provided in the room temp control loops for applications
that use the ARS Room temperature with the optional setpoint adjustment
slider. The position of the slider and the adjustment range provides an offset
value that is applied against the heating and cooling setpoints. When the slider
is in the middle position, the OFFSET = “0”. When the slider is in the uppermost
(max) position the OFFSET = (+ offset range). When the slider is in the
lowermost (min) position the OFFSET = (- offset range).
CONTROL SETPOINT
: The control setpoint is the setpoint that is used by the PI
control loop.
MEASURED
: This is the measured process variable used by the PI control loop.
ERROR
: This is the difference between the measured process variable and
control setpoint.
% DB
: The dead-band is a configurable parameter whose purpose is to improve
control loop stability by holding the control output constant until the calculated
error exceeds the % DB value. The dead-band also serves to extend the life of
the actuator by eliminating unnecessary actuator movements.
TUNING
: The AVR utilizes parallel PI algorithms which include two configurable
tuning parameters, “P” (Proportional Gain) and “I” (Integral). Both parameters
act in parallel on the ERROR and are combined to generate the control output
signal. Increasing the “P” term makes the control loop more sensitive and less
stable. The “I” term, sometimes referred to as “automatic reset”, increases the
control output by the integral of the error. Increasing the “I” term makes the
control loop more sensitive and less stable. Both the “P” and “I” terms can vary
based on the valve size and operating parameters. The factory default values for
P & I temperature and airflow control loops will accommodate the requirements
of most applications, however they can be adjusted if desired.
OUTPUT LIMITS:
The output limits are configurable parameters which are
essentially clamps for the control output. Normally the lower limit is set to 0%
and the upper limit is set to 100%. The output limits are only used for
applications that would benefit from limiting the control output thereby
preventing the valve from fully closing and/or fully opening.
CONTROL OUTPUT:
The control output manipulates the process variable to
reduce the error. The control output in the airflow control loops manipulate the
airflow control valve actuator, while the control output in the heating control
loops manipulate the reheat actuator.