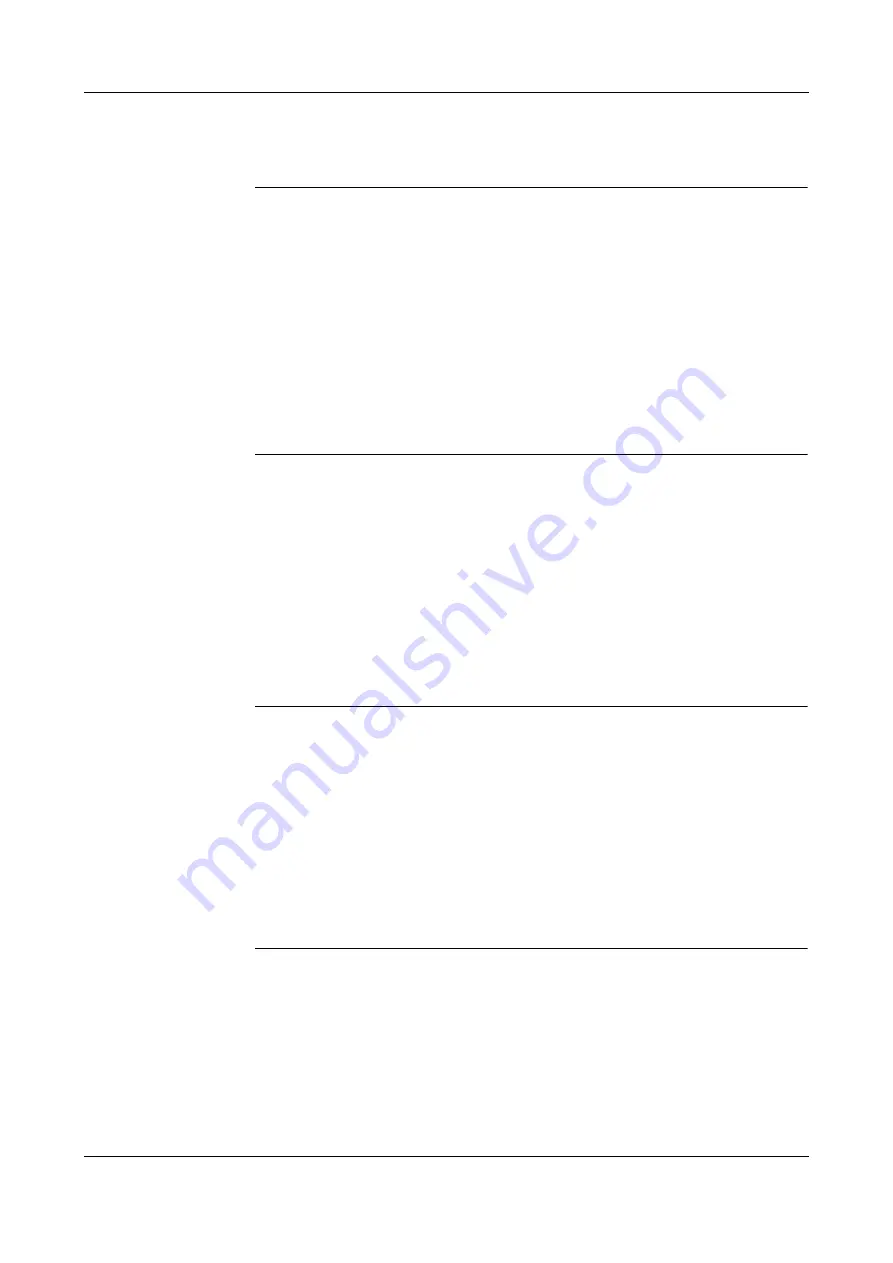
5 Installation and Commissioning
5.4 Robot Safety System Connections
70
Product Manual, Control Cabinet IRC5P
5.4.4 Emergency Stop Chain
General
The emergency stop (emy stop) chain is a dual channel chain where all switches and
relay contacts in the chain must be closed to enable power to be applied to the axis
motors. Breaking the emergency stop chain will cause electric power to be removed
from the robot axis motors and activate the axis brakes (breaking the run chain).
Breaking the chain will also disable the paint system, switch off high voltage and
stop pump motors, etc. After having stopped the robot by breaking the emergency
stop chain, it is required that the emergency stop button is manually pulled out and
that emergency stop reset is activated before power can be re-applied to the robot.
The two chains are called Chain 1 (Ch1) and Chain 2 (Ch2).
A principle diagram of the run chain is shown in
Emergency Stop Chain
Supply
The emergency stop chain 1 and 2 are supplied by the in24VDC in the
control cabinet.
The chain can also be supplied by an ex24VDC supply. The emergency stop
chain in the robot system will then be active also when the control cabinet main
switch is switched ‘off’. This function may be desired if the robot emergency stop
system is connected in the plant emergency stop system.
•
External power for the emergency stop chain can be connected to connections
marked ‘Ext Emy Stop Chain Supply’ in connector SCB-X4 pin 1-2 as shown in
and in principle diagram in
.
External Emergency
Stop (Category 0)
This is a connection where the user may implement one or more normally closed
(positive opening) switches in the robot’s emergency stop chain. This connection is
normally used in single robot installations. In more complex installations, the
General Mode Stop (category 0) or Delayed Stop (Category 1) function is normally
used. Which type to use must be based on risk analyses for the installation.
•
To install Emergency Stop switch(es), remove 2 jumpers (for chain 1 and 2) and
install a 2 pole, normally closed switch at terminals marked ‘Emergency Stop’ in
connector SCB-X1 pin 1-4 as shown in
and in principle diagram in
. The switch must comply with
Emergency Stop Reset
The emergency stop chain must be reset after the chain has been broken. To reset the
system, the cause for the emergency stop must first be removed and then a reset
signal must be applied.
An emergency stop reset signal is automatically applied when pressing the Motor
On button on the control panel, but the signal may also be applied from an external
PLC or reset switch. The emergency stop reset signal is also used to send an
acknowledge signal to various internal and external systems.
Содержание IRC5P
Страница 1: ...The heart of Robotics Product Manual Control Cabinet IRC5P 3HNA009834 001 en Rev 06 ...
Страница 2: ......
Страница 10: ...10 3HNA009834 001 en Rev 06 Product Manual Control Cabinet IRC5P ...
Страница 14: ...2 Safety 14 3HNA009834 001 en Rev 06 Product Manual Control Cabinet IRC5P ...
Страница 30: ...3 System Description 3 4 Pendant Description 30 3HNA009834 001 en Rev 06 Product Manual Control Cabinet IRC5P ...
Страница 218: ...218 3HNA009834 001 en Rev 06 Product Manual Control Cabinet IRC5P Manual Status ...