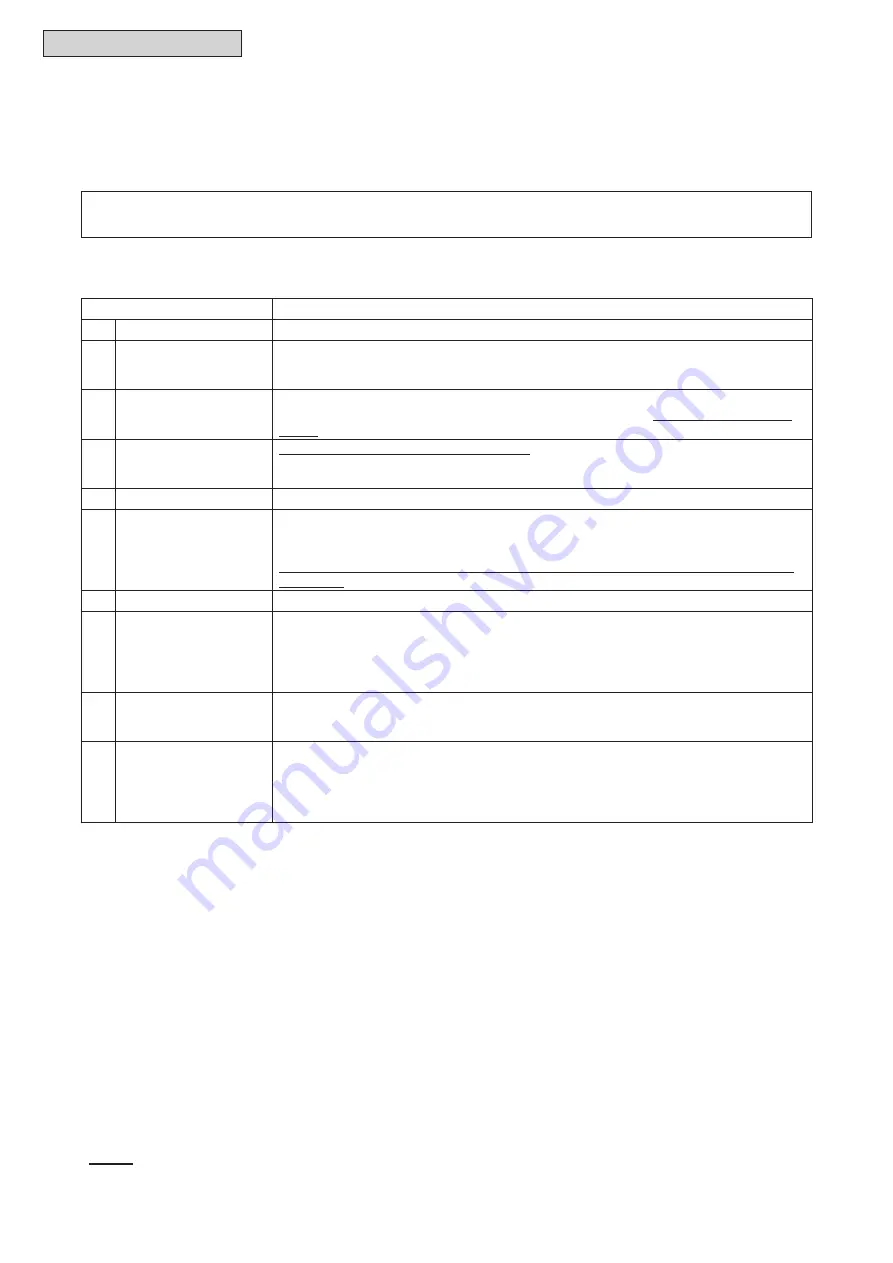
3-44
SM-16005-rev.2
TROUBLESHOOTING
3.3 Procedures for Checking
Refer to the Service Manual for Outdoor Unit.
3.4 Test Run
Check Item
Contents
1
Damage
Are the unit appearance and inside of the unit damaged?
2
Fan Motor
Is the fan motor runner installed in the center of the casing?
Is the fan motor installed away from the casing?
(The fan motor should NOT be touched by the casing.)
3
Fasteners
Are the screws loose due to vibration during transportation?
Check that the fasteners are secured firmly during installation,
especially for electrical
wiring.
4
Refrigerant Leaks
Check that there are NO refrigerant leaks.
The tightening part of the pipe (flare part) may be loose because of vibration during
transport.
5
DSW Setting
Check that the DSW setting is the same as the factory setting. (Refer to Section 3.1.3.)
6
Insulation
*1)
Measure resistance between electrical component terminal and ground with a tester.
It is normal if the resistance is 1M
W
and over.
If 1M
W
or less, do not perform the operation due to insulation failure of electrical parts.
Do NOT apply electricity to the terminal board of operating line. (Control PCB may be
damaged.)
7
Stop Valve Fully Open
Prior to test run, check that the stop valve of the outdoor unit is completely open.
8
Power Supply Phase
The operation is NOT possible with the incorrect power phase order or lacking phase.
• Alarm “05” is indicated on the LCD of the wired controller.
• “05” is indicated on the 7-segment display of the outdoor unit.
Check the power supply phase according to the caution label attached close to the
outdoor unit terminal block or inside of the service cover.
9
Turn ON Crankcase
Heater
*2)
After completion of item checks 1 to 8, turn ON the power supply of the outdoor unit.
Apply power to the outdoor unit(s) at least 12 hours prior to operation of the system for
preheating of the compressor oil..
10 Indoor and Outdoor
Temperature
<For Use in both Cooling and Heating Operation>
Is indoor temperature DB80
o
F (27
o
C) or less during heating operation?
(Heating operation may not be operated due to the activation of the overload operation
prevention under the ambient temperature of 66
o
F (19
o
C) or over.)
To perform the test run, set the test run mode with the wired controller.
*1): Insulation Resistance
l
If the unit has been turned OFF for long periods, insulation resistance may decrease to 1M
W
or less because
the refrigerant is retained in the compressor. Check the following points.
(a) Disconnect the cables of the compressor and measure the insulation resistance of the compressor itself.
If the resistance is 1M
W
or less, an insulation failure of another electrical charge part has occurred.
(b) If the resistance is 1M
W
or less, reconnect the compressor and turn ON the main power supply.
The compressor warms up automatically. Check the insulation resistance again after applying current for at
least three hours. (Preheating time depends on the air condition, piping length or refrigerant condition.)
l
Before the leakage breaker is activated, check the rated capacity.
*2): Stoppage of Compressor Operation
The compressor may NOT be operational for a maximum of four hours if the power supply is NOT turned ON in
advance.
At this time, the stoppage Code (d1-22) is displayed on the LCD of wired controller and the forced Thermo-OFF
function starts.
If operation of the compressor is necessary, turn ON the power supply of the outdoor unit, wait for 30 seconds
and press PSW5 on the outdoor unit PCB for at least three seconds. The forced Thermo-OFF function (d1-22)
is canceled and the compressor operation is available.
NOTE:
Thermo-ON: The outdoor unit and some indoor units are running.
Thermo-OFF: The outdoor unit and some indoor units stay on, but don't run.
Before the test run, check that the unit is appropriately installed according to the Installation and Maintenance
Manual. After that, inspect the following items.
Turn OFF all the power supply switches.
Use a tester and make sure that all the switches are turned OFF.
Summary of Contents for IDM030B21E Series
Page 2: ......
Page 10: ...viii SM 16005 rev 2...
Page 14: ......
Page 15: ...SM 16005 rev 2 1 1 INSTALLATION 1 Installation...
Page 19: ...SM 16005 rev 2 2 1 OPERATION 2 Operation...
Page 22: ......
Page 23: ...SM 16005 rev 2 3 1 TROUBLESHOOTING 3 Troubleshooting...
Page 70: ......
Page 71: ...SM 16005 rev 2 4 1 MAINTENANCE 4 Maintenance...
Page 130: ......
Page 131: ...SM 16005 rev 2 6 1 FIELD WORK INSTRUCTIONS 6 Field Work Instructions...
Page 140: ...6 10 SM 16005 rev 2 FIELD WORK INSTRUCTIONS 6 8 Mollier Chart for R410A f t 3 l b...
Page 141: ...SERVICE PARTS LIST SM 16005 rev 2 7 1 7 Service Parts List...
Page 143: ......
Page 144: ...2016 Johnson Controls Inc SM 16005 rev 2 Code No LIT 12012293 Revised February 2019...