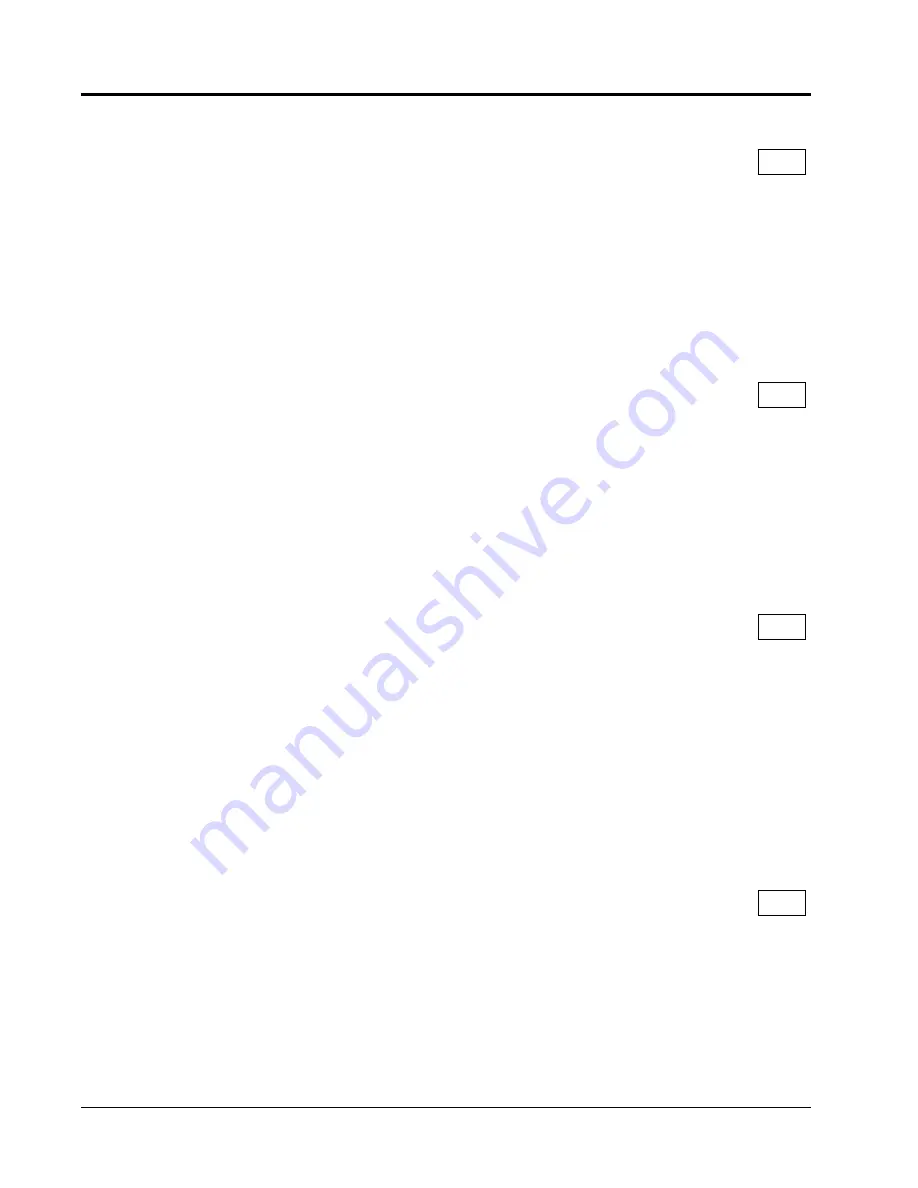
20
VS-616PS5 Programming Manual
Setting Range:
0.00 to 360.0s
Factory Default:
1.00s
The integral calculation sums the deviation over time which forces the deviation to
become zero. Thus, the feedback will match the desired setpoint. The integral time
determines how quickly the integral gain increase is added to the control loop. Too
high a setting will result in slow response. Too low a setting may result in rapid oscil-
lations (instability).
Setting Range:
0.0 to 100.0%
Factory Default:
100.0%
The integral limit is used to limit the range of the integral term. In some applications it
may be desirable to limit the integral term to improve system response. Otherwise,
the integral value may become large and overshoots may result when the integral
value takes a long time to integrate in the opposite direction. This value is set as a
percentage of maximum motor speed
(E1-06)
.
Setting Range:
0.00 to 10.00s
Factory Default:
0.00s
The derivative calculation attempts to control the remaining overshoot left over after
the proportion and integral calculations. If the system is approaching the intended
value very rapidly, the derivative control produces a strong braking action to prevent
overshoot. If the system is already stable with very little deviation change, derivative
control has very little effect. The derivative time is used to dampen oscillations and
reduce overshoot, thus improving stability. Setting the derivative time to a larger
number produces more braking action in the control system.
Setting Range:
0.0 to 100.0%
Factory Default:
100.0%
The PID limit places a limit on the PID signal output, limiting the output frequency ref-
erence. Normally this is set to 100% to allow unrestrained operation of the PID func-
tion. This value is set as a percentage of maximum motor speed
(E1-06)
.
B5-03 PID Control Integral Time
A
B5-04 PID Control Integral Limit
A
B5-05 PID Control Derivative Time
A
B5-06 PID Control Limit
A
Section B: Application Parameters
B5 PID Control