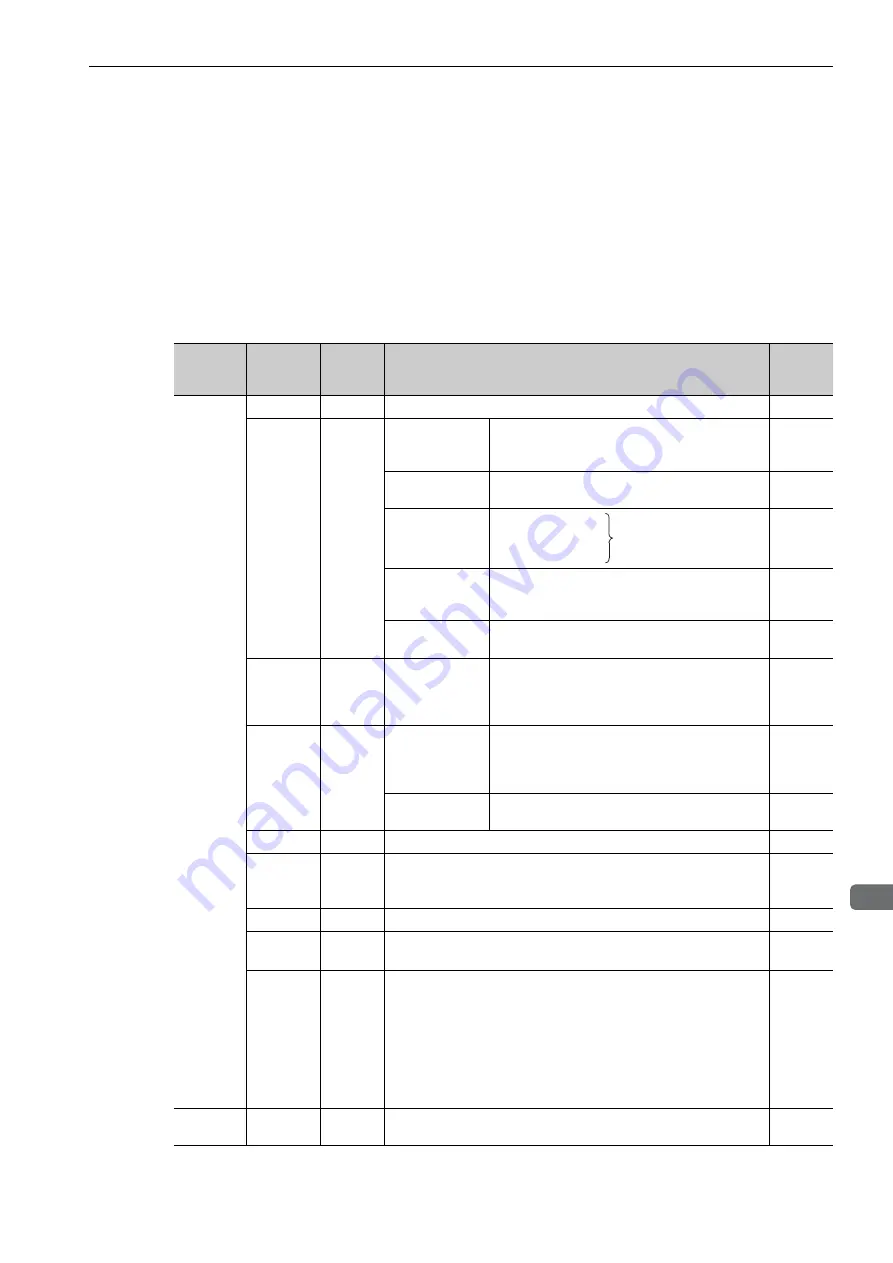
3.3 I/O Signal Connections
3-15
3
Wi
ring and
C
onne
ctio
n
3.3
I/O Signal Connections
This section describes the names and functions of I/O signals (CN1) on the multi-winding drive unit and the
safety function signals (CN8) on the SERVOPACK. Also connection examples are provided for different con-
trol methods.
3.3.1
Names and Functions for Multi-Winding Drive Unit I/O Signals (CN1)
The following tables give the names and functions of the I/O signals (CN1) on the multi-winding drive unit.
(1) Input Signals
Control
Method
Signal
Name
Pin No.
Function
Refer-
ence
Section
Common
/S-ON
40
Servo ON/OFF: Turns ON/OFF the servomotor.
5.2.1
/P-CON
41
Proportional con-
trol reference
Switches the speed control loop from PI (propor-
tional/integral) to P (proportional) control when
ON.
6.7.4
Rotation Direc-
tion reference
With internal set speed control selected: Switches
the servomotor rotation direction.
5.6.1
Control switch-
ing
5.7.2
Zero-clamp refer-
ence
With speed control with zero-clamp function
selected:
Reference speed is zero when ON.
5.3.5
Reference pulse
block
With position control with reference pulse stop
selected: Stops reference pulse input when ON.
5.4.8
P-OT
N-OT
42
43
Forward run
prohibited,
Reverse run
prohibited
With overtravel prevention: Stops servomotor
when movable part travels beyond the allowable
range of motion.
5.2.3
/P-CL
/N-CL
45
46
Forward external
torque limit,
Reverse external
torque limit
Activates/deactivates external torque limit func-
tion.
5.8.2
5.8.4
Internal set speed
switching
With internal set speed control selected: Switches
the internal set speed settings.
5.6.1
/ALM-RST 44
Alarm reset: Releases the servo alarm state.
−
+24VIN
47
Control power supply input for sequence signals.
Allowable voltage range: 11 to 25 V
Note: The 24 VDC power supply is not included.
3.5.2
SEN
4 (2)
Initial data request signal when using an absolute encoder.
5.9.2
BAT (+)
BAT (-)
21
22
Connecting pin for the absolute encoder backup battery.
Do not connect when the encoder cable with the battery case is used.
3.7.2
5.9.1
/SPD-D
/SPD-A
/SPD-B
/C-SEL
/ZCLAMP
/INHIBIT
/G-SEL
/PSELA
Signals
that can
be allo-
cated
The following input signals can be changed to allocate functions:
/S-ON, /P-CON, P-OT, N-OT, /P-CL, /N-CL, and /ALM-RST.
3.4.1
5.3.5
5.4.3
5.4.8
5.6.1
5.7.1
6.6.1
3.9.4
Speed
V-REF
5 (6)
Inputs speed reference. Input voltage range:
±
12 V max.
5.3.1
5.5.4
Position
↔
speed
Position
↔
torque
Torque
↔
speed
Enables control switching.