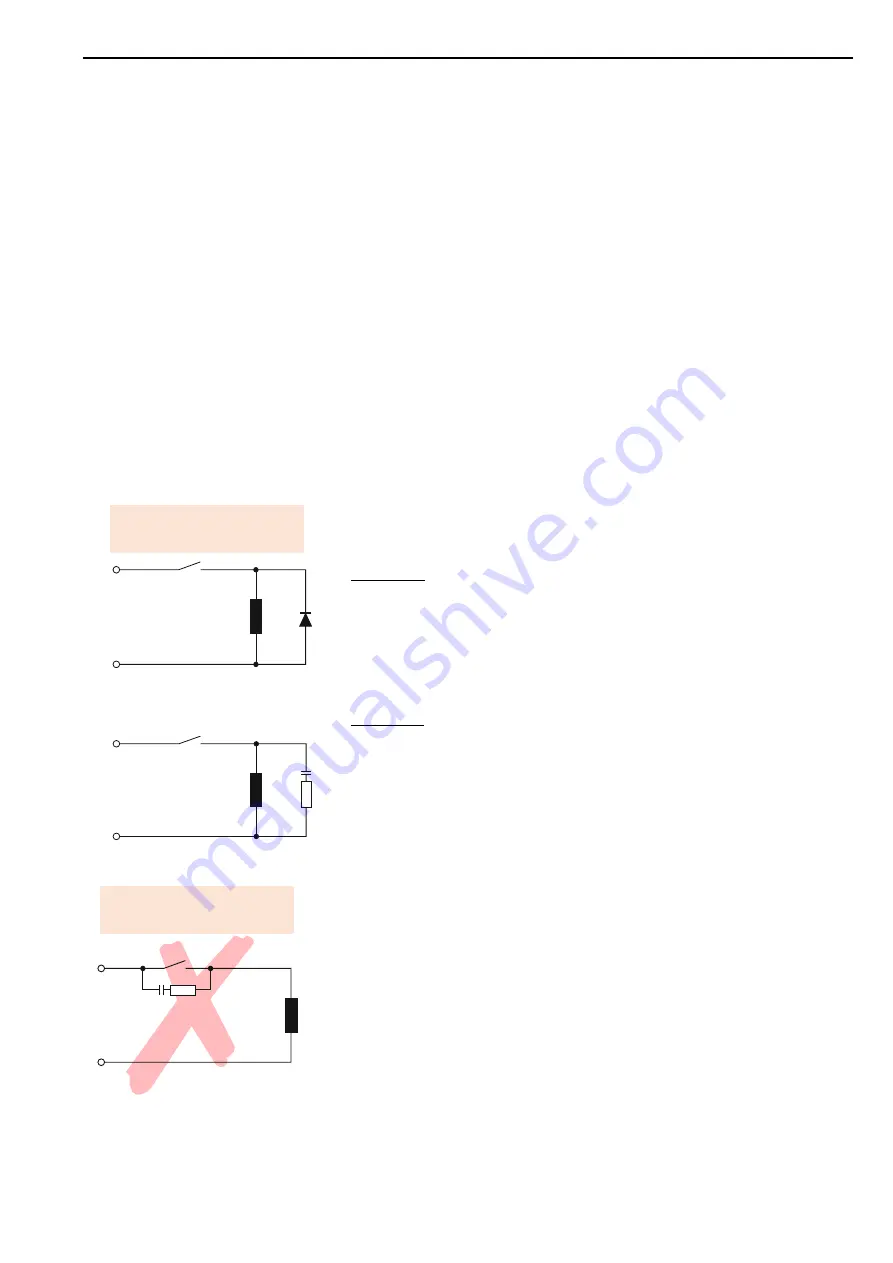
8. Other informations
105466
– TW-31-E - V1.9 - 06.04.2021
Page 69
to section 8.14: General measures when using electronic control systems
b. If specific interference sources cannot be avoided they should at least be kept
at a distance from the regulator system.
c. Capacitive and inductive couplings can cause crosstalk between high-voltage
lines and parallel low-voltage and sensor lines. This distorts measured values
and signals and can disrupt the entire regulatory process. It is therefore recom-
mended that all sensors and signal lines be placed separately from the control
and mains voltage lines.
d. If possible a separate main line should be provided to feed the regulator system.
This helps reduce any interference penetrating the regulator via the mains sup-
ply line. Voltage surges resulting from switching substantial loads will also then
be less of a problem.
e. In the case of contactors, solenoid valves and other inductive consumers the
induction voltage occurring during switching has to be reduced by appropriate
protection methods. The choice of methods depends on whether the consumer
runs on DC or AC voltage.
DC voltage
In the case of d/c voltage systems the induction voltage occurring can, for
example, be limited by using self-induction diodes, varistors or suppresser
diodes. The diagram on the left shows one possibility using a self-induction
diode.
AC voltage
In the case of a/c voltage interference suppression as described above is
not possible. Instead an RC combination must be used. An RC filter must be
connected as directly as possible to the inductance in order to ensure a short
line. In addition the component ratings of the RC combination must be
geared to the inductance. Too low ratings lead to excessive voltage and too
high ratings cause significant losses in the interference suppresser compo-
nent. Another point to note here is that only capacitors which meet VDE 0656
may be used. They must be suited to the mains voltage and designed for
very high switching voltages. The diagram on the left shows inductance in-
terference suppression using an RC filter.
An RC filter should not be fitted directly to the regulator's switching contact
(as shown on the left), as an idle current will flow through the RC combination
even when the switching contact is open. This current may be enough to
mean that a downstream contactor is not de-energised and a closed protec-
tive contact does not reopen.
U +
U -
AC
Right !
Wrong !
Regulator contact
Induktor
Diode
RC-
filter
Regulator contact
Induktor