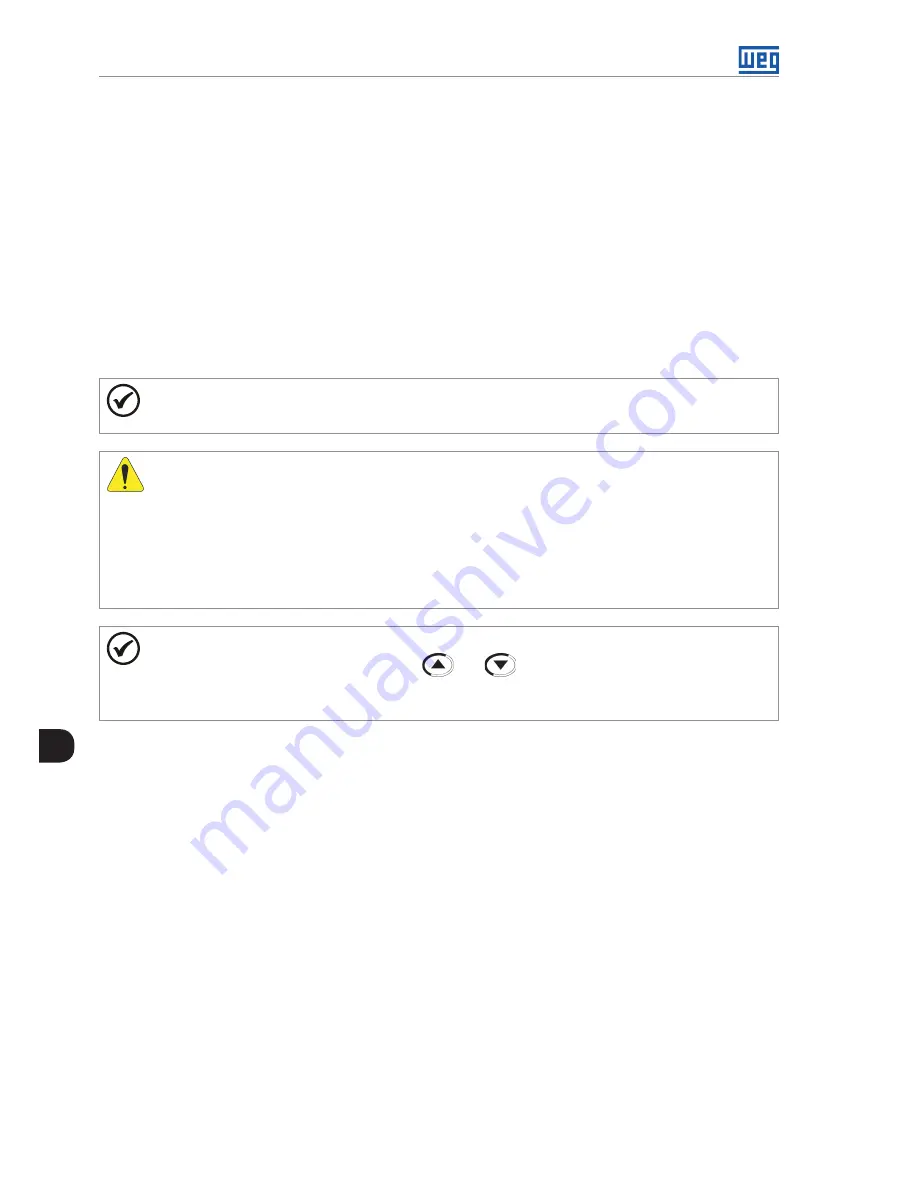
6-16 | MVW3000
6
Installation, Connection and Energization
At this moment the inverter is in undervoltage state (DC link is discharged) and the “ready to start” pilot light (H1)
at the control column door is on, indicating that it is already possible to initiate the inverter pre-charge.
3. Initiate the pre-charge / power section energization.
The MVW3000 inverter pre-charge command must be given manually:
With the ready to energize indicating light turned on, press the ON button.
Wait until the pre-charge is finished (approximately 15 seconds). During the pre-charge the pilot light must
remain on.
Once the pre-charge is successfully completed, the pre-charge indicating light (PRECHARGE) will turn off and
the Energized light will turn on, indicating the input switchgear was successfully closed.
The “inverter ready” message is displayed on the HMI.
NOTE!
The pre-charge procedure must not be repeated before 15 minutes. Doing so may damage the pre-
charge system due to overload.
ATTENTION!
If during the pre-charge any problem occurs, the inverter indicates an error related to it. The possible
errors are:
F0092 – Pre-charge circuit not ready.
F0014 – Fault in the closing of the input switchgear.
F0017 – Input switchgear not ready.
F0020 – Time exceeded in the pre-charge process.
See the description of those faults/alarms in the programming manual available for download on:
www.weg.net
.
NOTE!
The last speed reference value, set via the
and
keys, is saved in the memory (P0120 = 1).
If you want to change this value before enabling the inverter, change it through the parameter P0121
- (Keypad Speed Reference), which stores the keypad speed references.
NOTES:
1. If the motor speed direction is inverted, switch off the inverter following the safe de-energization instructions
and swap two of the motor cables.
The HMI must indicate the same direction seen looking against the motor shaft end.
2. It the current is too high during the acceleration, especially at low speeds, it is necessary to reduce the
acceleration ramp time (P0100 or P0102) or change P0136 - Torque boost setting.
Gradually increase and decrease the P0136 content until reaching an operation with approximately constant
current throughout the entire speed range. In the case above, see the description of the parameters in the
programming manual available for download on:
www.weg.net
.
3. In case some DC link overvoltage fault occurs during the deceleration, it will be necessary to increase the
deceleration time through P0101/P0103 and check P0151.
Summary of Contents for MVW3000 A0040 V023
Page 2: ......
Page 4: ......
Page 5: ...User s Manual Series MVW3000 Language English Document 10004823674 00 Publication Date 03 2017...
Page 6: ...Summary of Reviews Version Review Description R00 First edition...
Page 12: ...1 4 MVW3000 1 Safety Notices...
Page 58: ...6 18 MVW3000 6 Installation Connection and Energization...