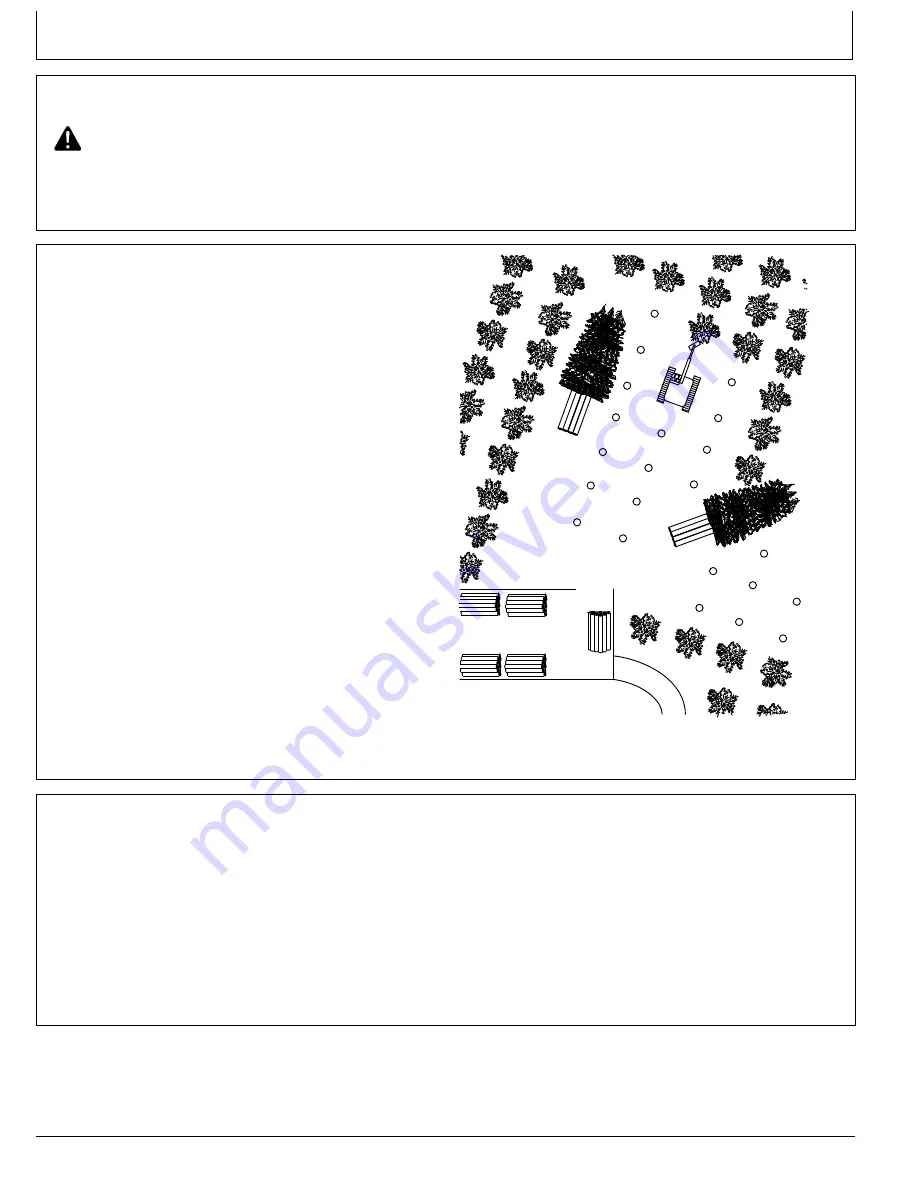
Operation: General
AM24480,000033B -19-29FEB16-1/1
AM24480,000033C -19-29FEB16-1/1
AM24480,000033D -19-06SEP21-1/1
Before starting work
CAUTION: The felling head should only be
operated by individuals who have been properly
trained. Allowing non- or improperly-trained
personnel to operate the machine will increase
the risk of serious injury.
Efficient operation of this felling head is directly informed by
practice and experience. If the felling head is not correctly
adjusted and/or the delimbing knives are not properly
sharpened, the head will not operate to its full potential.
Planning the work area
Mechanised timber felling requires appropriate planning,
the success of which rests upon previous experience.
Establish a management system that includes work site
procedures to limit personnel access during tree felling.
The following elements are important when formulating a
felling plan:
•
Terrain or area to be harvested
•
Ground conditions (including: water ways; soil type;
and erosion control)
•
Tree species
•
Stem density, stem form, and undergrowth
•
Site access, roading, and boundaries
•
Historic sites
•
Environmental areas
•
Transmission lines, gas lines, public access, storage
sites, and landings
•
Staff or team members’ abilities and experience
•
Hauling distance
Before felling begins, the site must be inspected.
Supervisors should ensure all team members are aware
of the constraints, hazards and requirements of the felling
operation.
Site meetings need to be held regularly, to ensure the
conditions of the plan are being upheld and to address
any elements not accommodated for in the plan.
TX1050356
—UN—29OCT08
Preparation
It is strongly recommended that the operator possesses
previous experience with operating this make of felling
head before starting the felling process.
In addition, before starting felling, it is recommended that:
•
The carrier is in a good condition, and that all windows
are clean.
•
You inspect the cutting unit to ensure all its elements
are in good condition (for example, the unit has been
sharpened).
•
You test all controls.
•
The carrier’s “automatic idle” function is switched off;
failing to do so may result in the carrier idling down
when the saw chain is in use.
•
The location of all roads, waterways, and boundaries
have been noted/recorded.
•
You check for any additional hazards.
•
You run all functions to ensure the hydraulic functions
have been properly warmed up.
2-1-1
090621
PN=32
Summary of Contents for FL85
Page 4: ...Introduction 090621 PN 4...
Page 79: ...Index Index 3 090621 PN 79...
Page 80: ...Index Index 4 090621 PN 80...