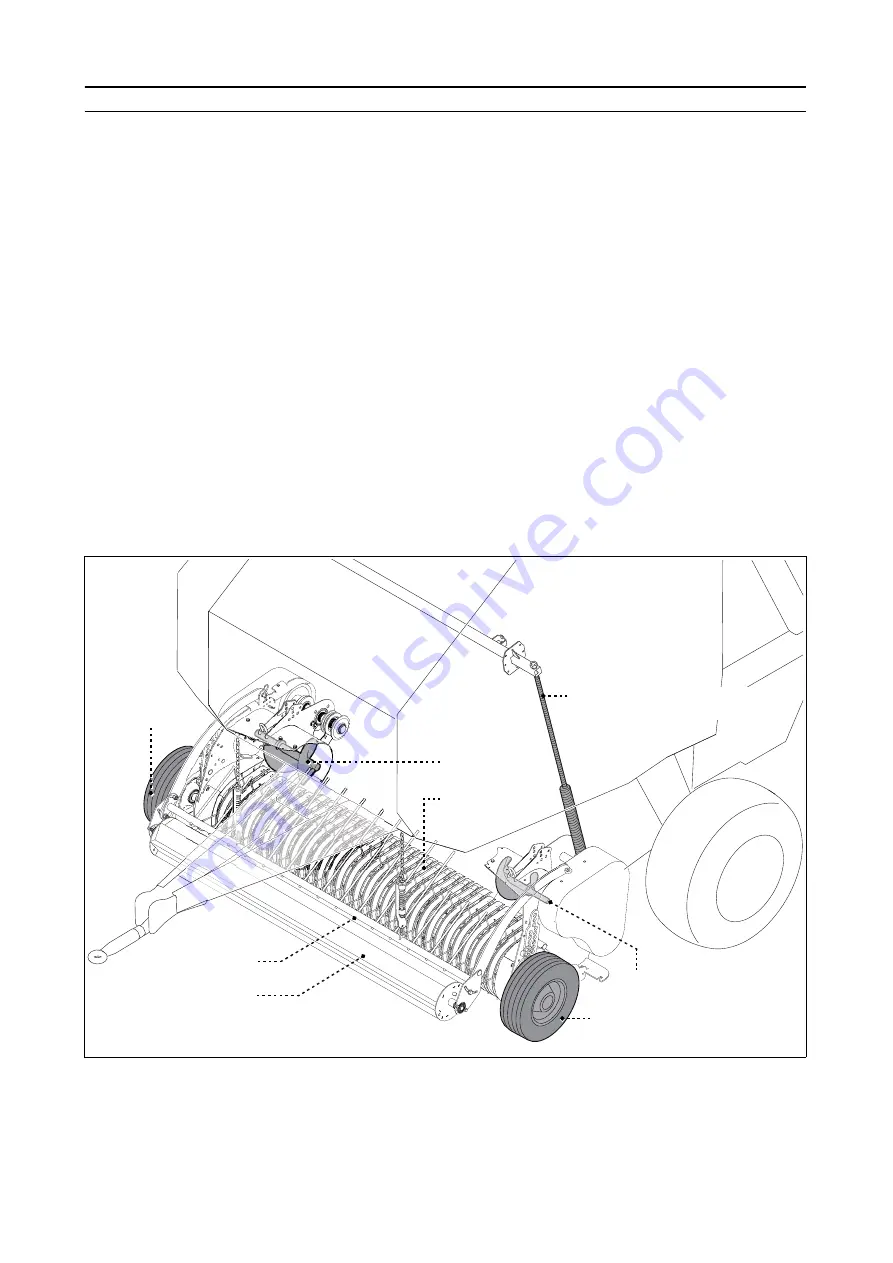
4
8
3
-0
0
8
-0
.f
m
ID
M
-
95 -
English
Part 4
▬▬▬▬▬▬▬▬▬▬▬▬▬▬▬▬▬▬▬▬▬▬▬▬
Pick-up unit (extra-large type)
GENERAL DESCRIPTION
78
The pick-up unit picks the product in the windrow and conveys it into the
machine feeding area.
The functions of the unit parts are activated by the main motor drive of
the machine where it is installed.
Unit is equipped with clutch that, in case of clogging, automatically
releases itself to avoid damaging the machine.
After having restored normal working conditions of the unit, the
clutch automatically re-inserts itself.
–
"Reel" device (A)
: it makes the product pick-up operation easier,
and is equipped with two cams that guide the tine-holder rods.
–
Baffle plate (B)
: it allows a more regular feeding of the product, even
in case of short and chopped products.
In the machines equipped with a rotor or cutting device , roller
(B1)
is also installed, which further improves the feeding of the product.
–
Auger (C)
: there are two augers (one on each side), which convey
and adapt the product to the width of the baling chamber.
–
Wheel (D)
: there are two wheels (one on each side) and, thanks to a
shock absorber system
(E)
, they allow the pick-up unit to adapt itself
to the different conformations of the ground.
Baffle plat
(B)
"Reel" device
(A)
Roller
(B1)
Wheel
(D)
Spiral conveyor
(C)
Spiral conveyor
(C)
Wheel
(D)
Suspension device
(E)
ID
M
4
8
3
0
0
8
0
0
1
0
0
d
f
Summary of Contents for RV 4116
Page 2: ......
Page 44: ...IDM 21720307900 pdf General information about the machine 483 004 0 fm IDM English 38 Part 2...
Page 131: ...483 004 0 IDM 125 English Part 8 Attachments...
Page 133: ...IDM 48300401100 pdf 483 004 0 IDM 127 Attachments English Part 8 ESD A01...
Page 137: ...483 004 0 IDM 131 Attachments English Part 8 ESD A05 CAN CABLE 1 IDM 48300101800 pdf...
Page 151: ...483 004 0 IDM 145 Attachments English Part 8 IDM 48300401700 pdf HSD A01...
Page 153: ...483 004 0 IDM 147 Attachments English Part 8 IDM 48300401800 pdf HSD A02...
Page 155: ...483 004 0 IDM 149 Attachments English Part 8...
Page 162: ......
Page 164: ......
Page 168: ...483 011 0IX fm IDM English 2...
Page 192: ......