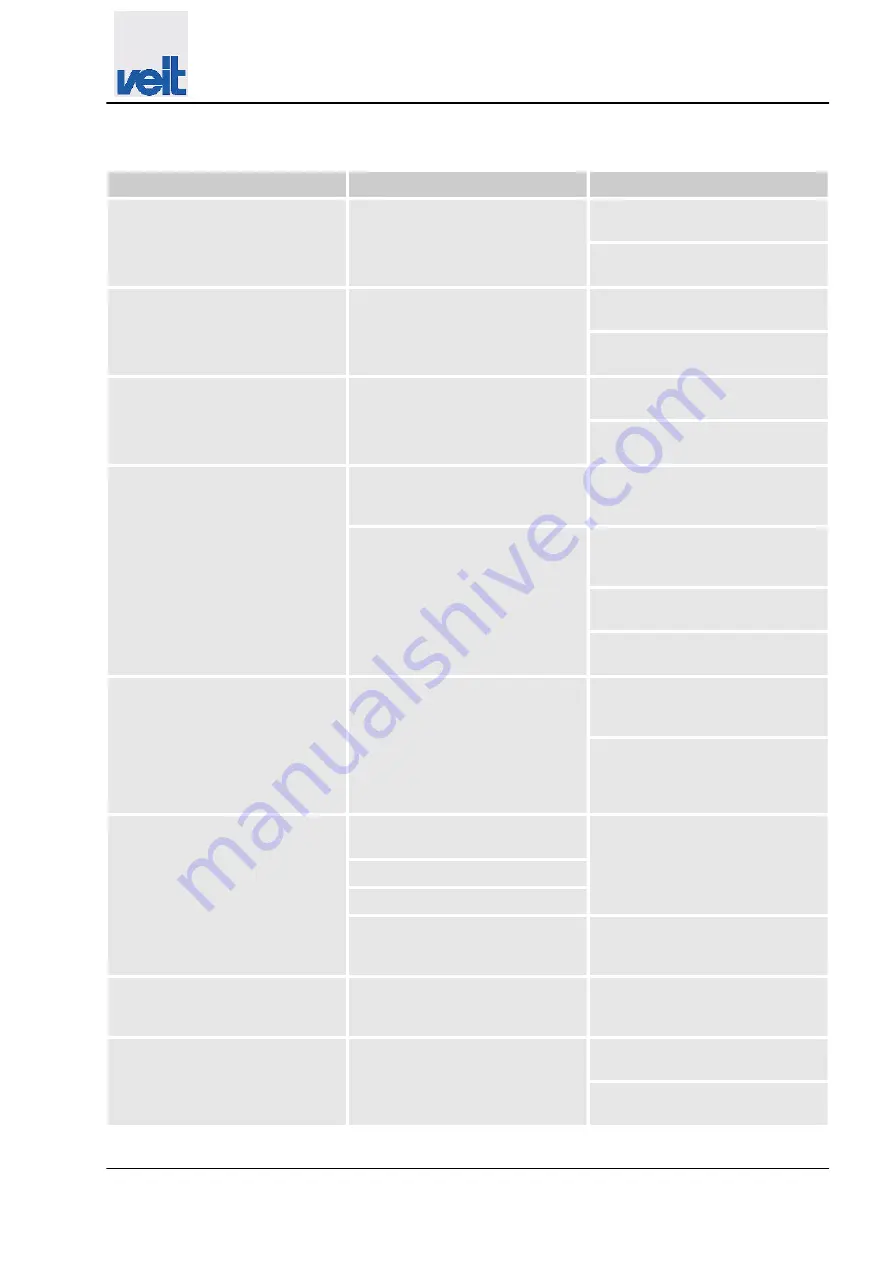
Error message
Cause
Remedy
12 Error condensate temp. MFP
KT2
Temperature sensor signal of con-
densate connection for external
cuff tuck press faulty.
Check the temperature sensor
and replace if necessary.
Check the wiring of the tempera-
ture sensor.
13 Error condensate temp. heat.
reg. KT1
Temperature sensor signal of con-
densate connection for solenoid
valve faulty.
Check the temperature sensor
and replace if necessary.
Check the wiring of the tempera-
ture sensor.
14 Error condensate temp. heat.
reg. KT0
Temperature sensor signal of con-
densate connection for internal
heating register faulty.
Check the temperature sensor
and replace if necessary.
Check the wiring of the tempera-
ture sensor.
15 Error analog value moisture
Insert for detecting the residual
moisture (in the front clamp) not
connected.
Connect the insert to the residual
moisture control system.
Signal of the residual moisture
control system faulty.
Check the residual moisture con-
trol system and replace, if neces-
sary.
Replace the insert for detecting
the residual moisture.
Check the wiring of the residual
moisture control system.
16 Error moisture activation
threshold
The current moisture threshold
value is out of range of plausible
values.
Calibrate the residual moisture
control system (see manual
mode).
If this error occurs after calibration
and subsequent error acknowl-
edgement, please contact your
VEIT subsidiary.
18 Error motor energy recycling
Winding temperature of the motor
too high.
Check the fan wheel for ease of
movement.
Motor load too high.
Motor blocked.
Insufficient cooling.
Clean the motor (remove deposits
of dirt and dust, particularly on the
fan plate).
19 Error frequency inverter U1
Numerous error causes
Read the error code on the fre-
quency inverter; please contact
your VEIT subsidiary.
20 Emergency Switch
Emergency stop device was acti-
vated.
Release the emergency stop
device.
Acknowledge the error message
with the "Stop" button.
Remedy of faults/elimination of defects
Alarm messages on the touch screen > Error messages
18.07.2017
Shirt finisher VEIT SF26
79
Summary of Contents for SF26
Page 85: ...12 1 Spare parts list Spare parts Spare parts list 18 07 2017 Shirt finisher VEIT SF26 85 ...
Page 86: ...Fig 31 From 10 2016 Spare parts Spare parts list 18 07 2017 Shirt finisher VEIT SF26 86 ...
Page 87: ...Fig 32 From 10 2016 Spare parts Spare parts list 18 07 2017 Shirt finisher VEIT SF26 87 ...
Page 90: ... with 3ph version only Spare parts Spare parts list 18 07 2017 Shirt finisher VEIT SF26 90 ...
Page 91: ...Spare parts Spare parts list 18 07 2017 Shirt finisher VEIT SF26 91 ...
Page 92: ...Spare parts Spare parts list 18 07 2017 Shirt finisher VEIT SF26 92 ...
Page 93: ...Spare parts Spare parts list 18 07 2017 Shirt finisher VEIT SF26 93 ...
Page 94: ...Spare parts Spare parts list 18 07 2017 Shirt finisher VEIT SF26 94 ...
Page 96: ...Fig 34 Cover from 10 2016 Spare parts Spare parts list 18 07 2017 Shirt finisher VEIT SF26 96 ...
Page 97: ...Spare parts Spare parts list 18 07 2017 Shirt finisher VEIT SF26 97 ...
Page 108: ...Spare parts Pneumatics diagram 18 07 2017 Shirt finisher VEIT SF26 108 ...
Page 109: ...12 3 Circuit diagram Spare parts Circuit diagram 18 07 2017 Shirt finisher VEIT SF26 109 ...