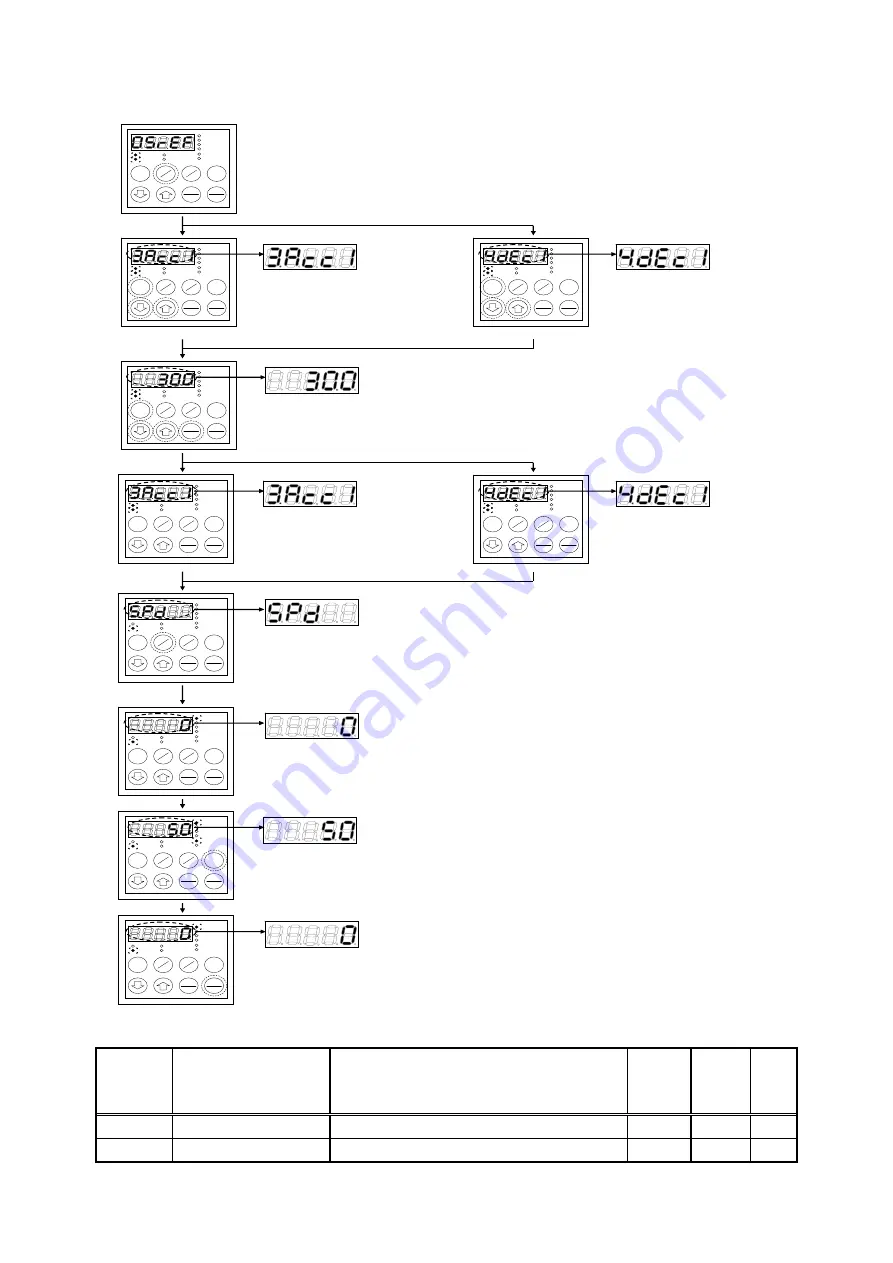
25
3.3.2. How to Change the Acceleration/Deceleration time
r/min
Hz
A
V
FNC
DIR
REV
ALM
RUN
JOG
FNC
RESET
FWD
JOG
START
STOP
REV
MONI
SET
→
When the FNC (LED) on the console panel [SET66-Z] is turned off, press the [MONI/FNC] key to turn on
the FNC (LED).
r/min
Hz
A
V
FNC
DIR
REV
ALM
RUN
JOG
FNC
RESET
FWD
JOG
START
STOP
REV
MONI
SET
→
Use the [
↑
] and [
↓
] keys to select “3.
Acc1” (Acceleration time (1)). Press
the [SET] key to confirm
.
r/min
Hz
A
V
FNC
DIR
REV
ALM
RUN
JOG
FNC
RESET
FWD
JOG
START
STOP
REV
MONI
SET
→
Use the [
↑
] and [
↓
] keys to select “4.
dEc1” (Deceleration time (1)).
Press the [SET] key to confirm.
<Acceleration
time>
<Deceleration time>
r/min
Hz
A
V
FNC
DIR
REV
ALM
RUN
JOG
FNC
RESET
FWD
JOG
START
STOP
REV
MONI
SET
→
Use the [JOG/
→
] key to move the operation digit to the right, use the [
↑
] and [
↓
]
keys to change the numbers (Acceleration time/Deceleration time), and press the
[SET] key to confirm.
*The setting range
is from 0.0 to 3600.0 [s].
r/min
Hz
A
V
FNC
DIR
REV
ALM
RUN
JOG
FNC
RESET
FWD
JOG
START
STOP
REV
MONI
SET
→
After confirming the Acceleration
time with the [SET] key, “3. Acc1” is
displayed again.
r/min
Hz
A
V
FNC
DIR
REV
ALM
RUN
JOG
FNC
RESET
FWD
JOG
START
STOP
REV
MONI
SET
→
<Acceleration
time>
<Deceleration time>
After confirming the Deceleration
time with the [SET] key, “4. dEc1” is
displayed again.
r/min
Hz
A
V
FNC
DIR
REV
ALM
RUN
JOG
FNC
RESET
FWD
JOG
START
STOP
REV
MONI
SET
→
Press the [MONI/FNC] key to turn off FNC (LED). Monitor item, such
as “SPd,” is displayed for about one second.
r/min
Hz
A
V
FNC
DIR
REV
ALM
RUN
JOG
FNC
RESET
FWD
JOG
START
STOP
REV
MONI
SET
→
1 sec.
later
About one second later, the display changes to the data of the
currently set monitor item
<The figure on the left shows that the motor speed is “0 [r/min].”>.
r/min
Hz
A
V
FNC
DIR
REV
ALM
RUN
JOG
FNC
RESET
FWD
JOG
START
STOP
REV
MONI
SET
→
When you press the [START] key, the operation starts. The motor starts
to rotate and accelerates/decelerates at the set
Acceleration/Deceleration time. During operation, the data of the
currently set monitor items is displayed.
<The figure on the left shows that the motor speed is “50 [r/min].”>
*Acceleration/Deceleration time can be changed during the operation,
too.
r/min
Hz
A
V
FNC
DIR
REV
ALM
RUN
JOG
FNC
RESET
FWD
JOG
START
STOP
REV
MONI
SET
→
When you press the [STOP/RESET] key, the operation stops and the
rotation of motor stops.
<The figure on the left shows that the current motor speed is “0
[r/min].”>
<Setting range of the Acceleration/Deceleration time/setting resolution/initialized data/unit>
Console
panel
Use monitor
display
Contents
Setting range
(Selecting item)
Setting
resolution
Initialized
data
Unit
3.Acc1
Acceleration time (1)
0.0 to 3600.0
0.1
30.0
sec
4.dEc1
Deceleration time (1)
0.0 to 3600.0
0.1
30.0
sec