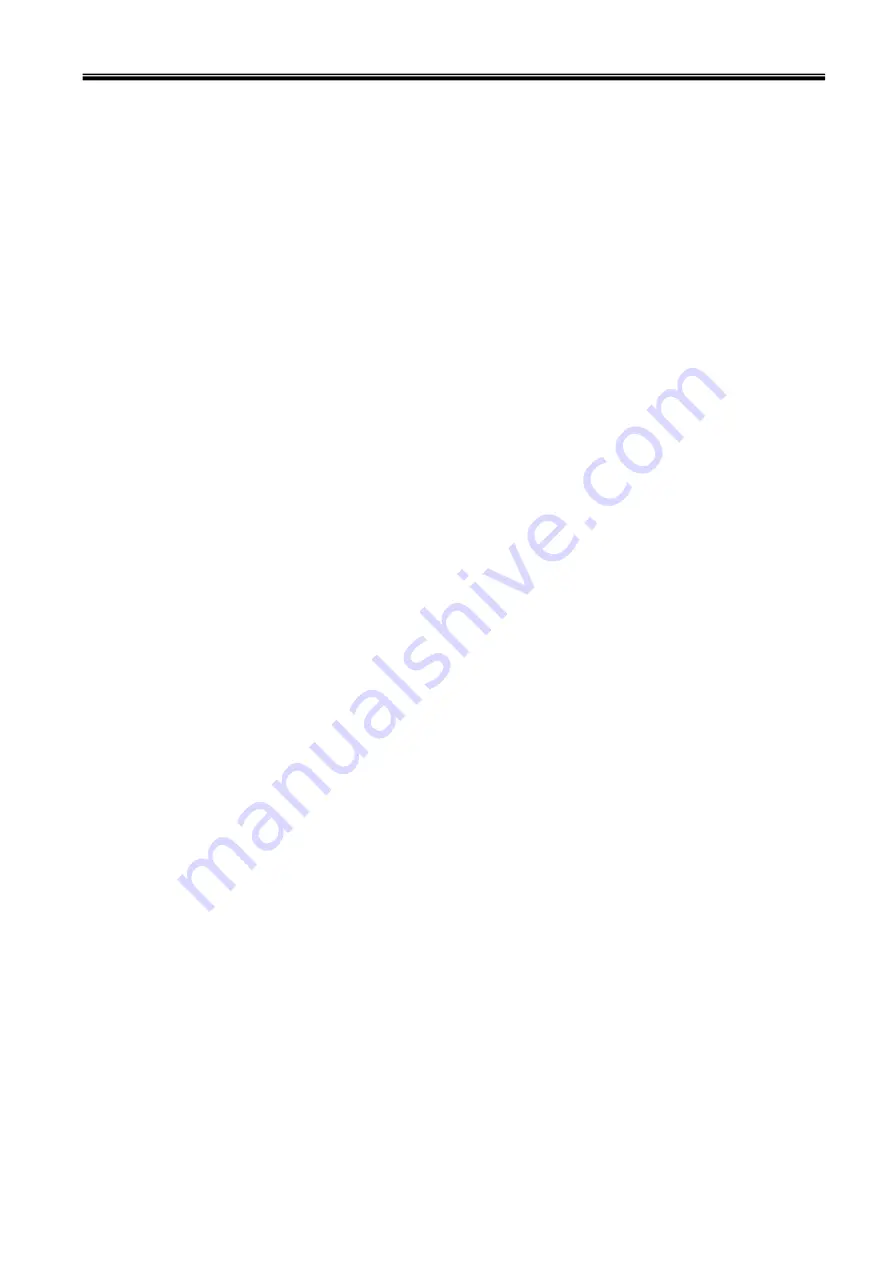
TRANSPORTATION AND INSTALLATION MANUAL
8
Installing the Controller (In case of TSL3100E) ............................................. 61
Installing the Controller (In case of TS3100) ................................................. 66
System Connections(In case of TSL3100) .................................................... 71
Connector Arrangement on the Controller ................................................ 71
Connecting the Power Cable “ACIN” ([1] of Fig. 7.1; plug connector
Connecting the Motor Cable/Encoder Cable ............................................ 74
Connecting the Brake Cable/Robot Control Signal Cable ........................ 75
Connecting Power Supply Cable for External Input/Output "GND, P24V"
Connecting and Disconnecting Cables ..................................................... 76
Examples of Connector Terminal Arrangement (for the TSL3100) ........... 78
Connector Signal Connection Diagrams ................................................... 82
Jumpers for Safety Related Signals ......................................................... 82
System Connections (In case of TSL3100E) ................................................. 84
Connector Arrangement on the Controller ................................................ 84
Connecting the Power Cable “ACIN” ([1] of Fig. 8.1; plug connector
Connecting the Motor Cable/Encoder Cable ............................................ 87
Connecting the Brake Cable/Robot Control Signal Cable ........................ 88
Connecting Power Supply Cable for External Input/Output "GND, P24V"
Connecting and Disconnecting Cables ..................................................... 89
Examples of Connector Terminal Arrangement (for the TSL3100) ........... 92