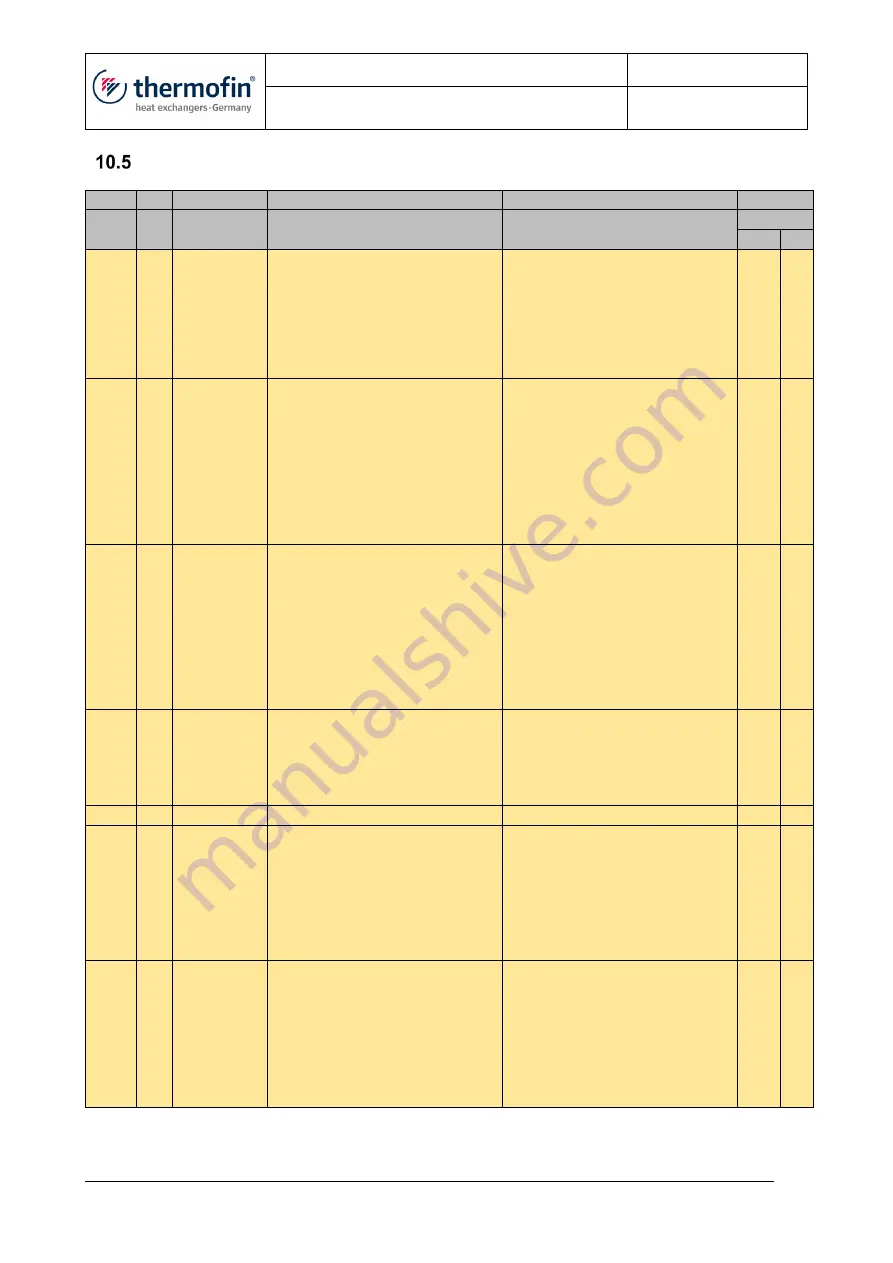
Controller operating manual
15.11.2020 – Version 1.1
TCS.2 series –
thermofin
®
control system 2
nd
generation
Page: 158/162
Operating manual - translation into English © thermofin GmbH
Signals external messages – Error code S...
English
English
English
Error
code
Type
Error text
Error explanation
Error remedy
MODBUS
Reg. Bit
S01
W
Control
voltage is
missing
- No signal at digital input 7
- The control voltage supply to the
digital inputs is interrupted
- Check the control voltage fuse of
the digital inputs (if necessary
F692)
- Check wiring in the control
cabinet or externally
- Check terminal points
- Check configuration of DI-7
141 12
S02
W
Setpoint
shift [no.]
wire break
- This error message is only active
with signal types 4-20 mA or 2-10
V.
- A current < 4 mA flows at the
corresponding analogue input or a
voltage < 2 V is applied
- Incorrect configuration of the
analogue input (jumper position)
- Control line interrupted / check
wiring
- Check terminal points
- Check the configuration of the
respective analogue input (see
device manual, chapter 3.6.4)
- The analogue input may be
defective, please contact the
manufacturer
S03
A
Slave speed
[no.] wire
break
- This error message is only active
with signal types 4-20 mA or 2-10
V.
- A current < 4 mA flows at the
corresponding analogue input or a
voltage < 2 V is applied
- Incorrect configuration of the
analogue input (jumper position)
- Control line interrupted / check
wiring
- Check terminal points
- Check the configuration of the
respective analogue input (see
device manual, chapter 3.6.4)
- The analogue input may be
defective, please contact the
manufacturer
S04
W
External
emergency
stop
- An external emergency stop has
been activated
- For two-circuit devices, the
corresponding index number 1 or 2
is also displayed
- Control line interrupted / check
wiring
- Check terminal points
- Eliminate the fault in the pump
for the pressure increase
S05
S06
W
Failure
Storage tank
- General message that the storage
tank for the service water is faulty
- If this function is not required, a
wire bridge can either be installed
on the respective terminals or the
function is deactivated in the
"Control" menu
- Control line interrupted / check
wiring
- Check terminal points
- Eliminate the fault on the storage
tank
145 8
S07
W
Failure
Pressure
increase
- General message that the
pressure increase for the service
water is faulty
- If this function is not required, a
wire bridge can either be installed
on the respective terminals or the
function is deactivated in the
"Control" menu
- Control line interrupted / check
wiring
- Check terminal points
- Eliminate the fault in the pump
for the pressure increase
145 7