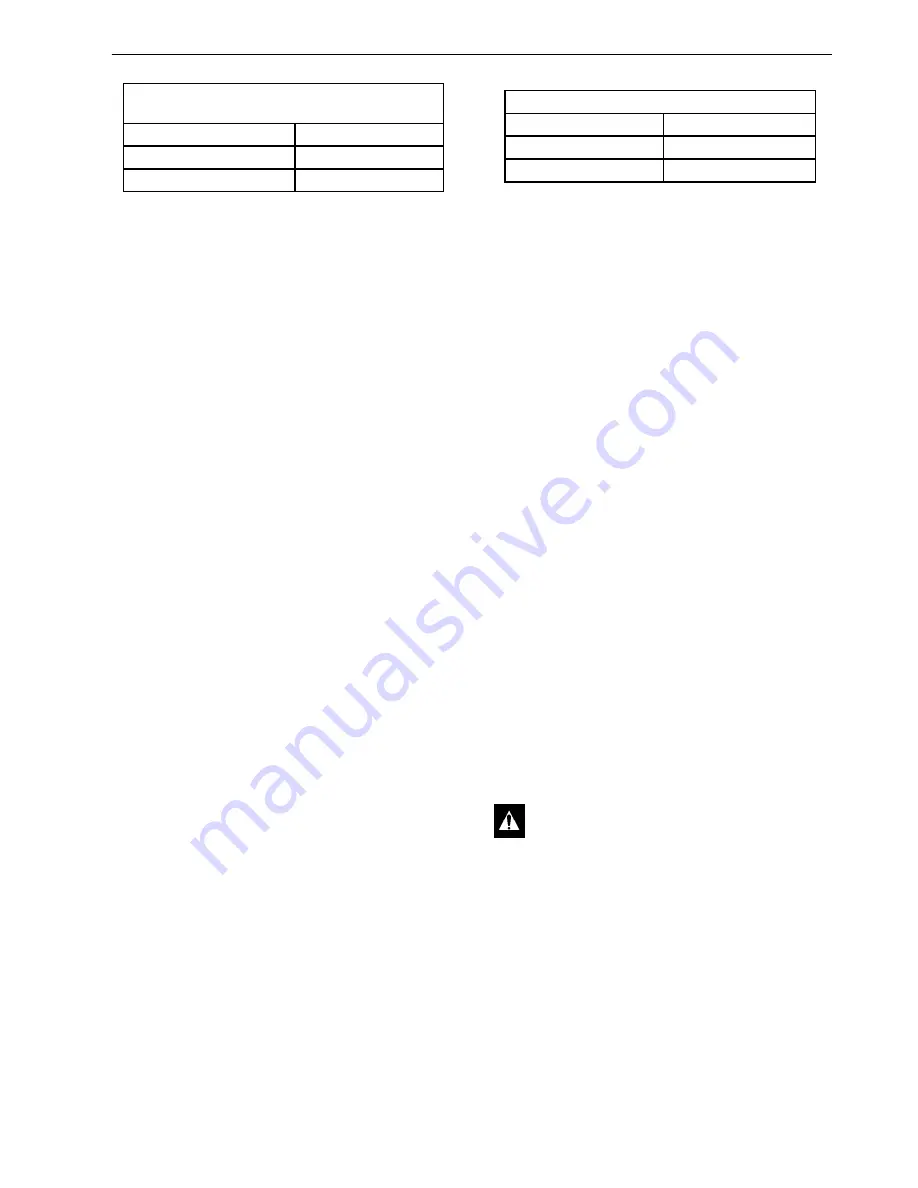
Refrigeration Service Procedures
131
Compressor Temperature Sensor
Testing
The compressor temperature sensor is part of the
SR-3 Microprocessor Control System. Alarm
Code 80 (Check Compressor Temp Sensor)
indicates a possible problem with the compressor
temperature sensor. Refer to the appropriate
Microprocessor Diagnostic Manual for
information about testing the compressor
temperature sensor.
Compressor Temperature Sensor
Replacement
NOTE: Thermo King recommends changing the
compressor temperature sensor whenever the
insulation on the leads has been broken or there
is other reason to suspect a defective sensor.
The steps for changing the compressor
temperature sensor are as follows:
1. Cut through silicone sealant surrounding
plastic cap.
2. Pry plastic cap out of top cap.
3. Remove compressor temperature sensor by
pulling it out of top cap well.
4. Clean all debris out of top cap well and off of
top cap surface.
5. Apply 0.25 to 0.50 cubic centimeters of
thermally conductive silicone grease (p/n
CHEMPLEX 1381 Heatsink Silicone) into
thermal well.
6. Insert new compressor temperature sensor into
well.
7. Apply RTV to underside of new protective
plastic cap.
8. Press new protective plastic cap in place with
wire channel pointed down. Cap will snap into
place when in proper location.
Condenser Check Valve and
Purge Check Valve Test
The condenser check valve and the purge check
valve prevent refrigerant from moving into the
condenser when the unit is in heat. A unit with a
leaking condenser check valve or purge check
valve will have good heating capacity when it first
goes into the heat mode. But, it will gradually lose
heating capacity as refrigerant moves into the
condenser. This problem is more noticeable at
lower ambient temperatures. Use the following
procedure to test the condenser check valve and
the purge check valve.
1. Attach a gauge manifold to the suction service
valve and the discharge service port. Attach
another low pressure gauge to the suction
access port located in the suction line near the
accumulator inlet. Attach a high pressure
gauge to the service port on the receiver tank
outlet valve. Low loss fittings must be used on
the hoses connected to the discharge service
port and the suction access port.
2. Operate the unit in low speed cool until the
system pressures stabilize.
3. Front seat the receiver tank outlet valve and
allow the low side to pump down to 0 to 5 in.
Hg vacuum (0 to -17 kPa).
4. Turn the unit Off.
5. Front seat the suction service valve to isolate
the low side while it is still in a vacuum.
6. Watch the low pressure gauge attached to the
suction access port. The low side pressure
should not rise. If it does, there could be a leak
through one (or more) of following
components: hot gas solenoid, liquid injection
solenoid, purge valve, or receiver tank
pressure check valve.
Spring
See Parts Manual
Screen
See Parts Manual
Screen Cover
See Parts Manual
Other Parts Which May Be Used (As Needed)
Are: (Continued)
Parts List (As Needed)
Sensor Assembly
See Parts Manual
Silicone Sealant
N/A
RTV
See Tool Catalog
CAUTION: Do not run scroll compressor
in a vacuum for more than 1 minute.
Summary of Contents for UT-1200
Page 10: ...Table of Contents 10...
Page 20: ...Safety Precautions 20...
Page 76: ...Operating Instructions for Premium HMI Control Panel 76...
Page 88: ...Electrical Maintenance 88...
Page 98: ...Engine Maintenance 98 Figure 167 Fuel Components...
Page 142: ...Refrigeration Service Procedures 142...
Page 148: ...Clutch Maintenance 148...
Page 150: ...Structural Maintenance 150...
Page 162: ...Wiring and Schematic Diagrams Index 162...
Page 163: ...163 Schematic Diagram Page 1 of 2...
Page 164: ...164 Schematic Diagram Page 2 of 2...
Page 165: ...165 Wiring Diagram Page 1 of 5...
Page 166: ...166 Wiring Diagram Page 2 of 5...
Page 167: ...167 Wiring Diagram Page 3 of 5...
Page 168: ...168 Wiring Diagram Page 4 of 5...
Page 169: ...169 Wiring Diagram Page 5 of 5...