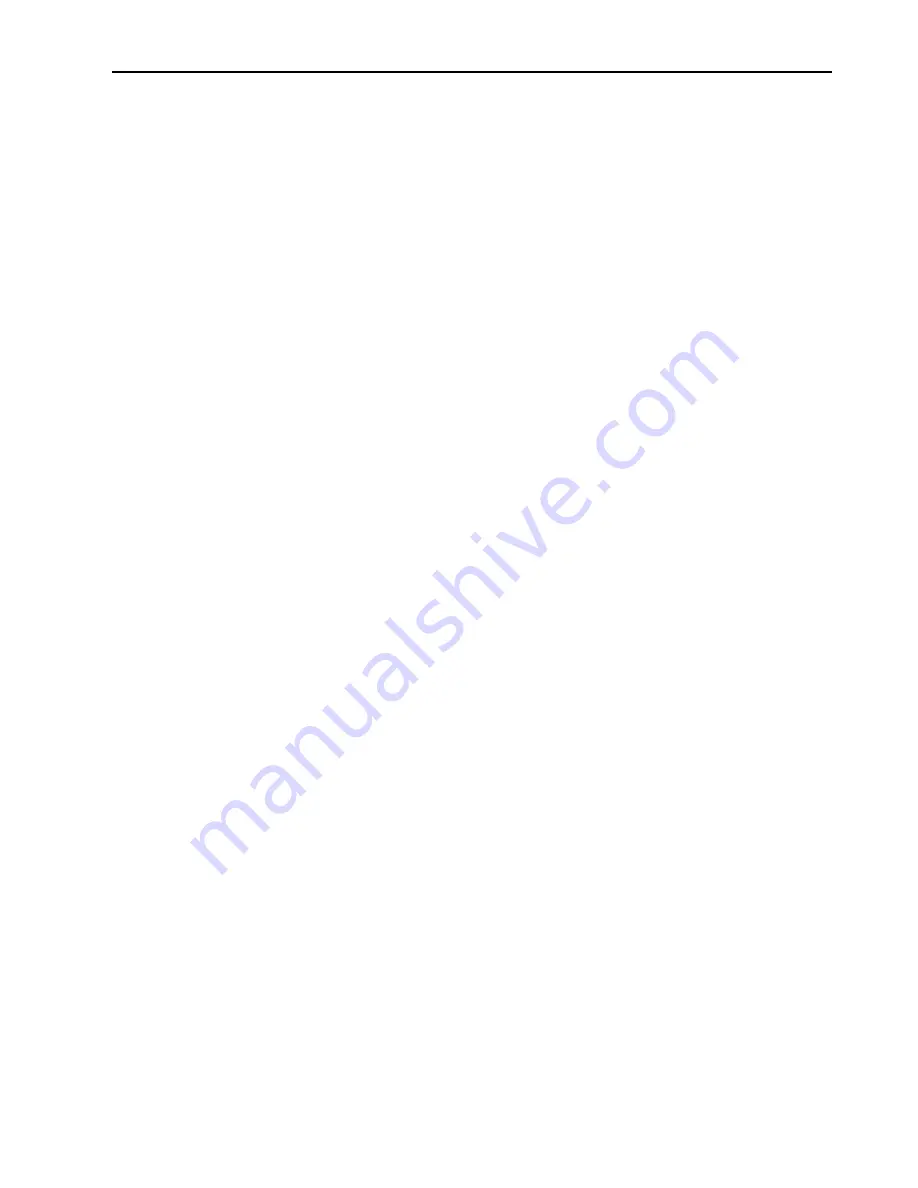
115
Refrigeration Service Procedures
Evacuation, Dehydration, and
Charging
Evacuation is Important and is Critical to System
Performance!
It has been determined through testing and system
analysis that refrigeration systems which contain
non-condensables such as nitrogen and/or air can
be overcharged with refrigerant when charged
using the sight glass method. An overcharge of
refrigerant will cause high system pressures,
system shutdowns, and compressor damage.
Moisture in the system will produce acid and
other contaminants that lead to compressor
failure.
Therefore, Thermo King recommends that all
repairs to the refrigeration system include the
removal and reclamation (cleaning) of the
refrigerant, followed by a thorough evacuation
using the proper tools and procedures.
The primary objective of evacuation is to bring
the system’s pressure into a vacuum to ensure the
removal of non-condensables. The objective of
dehydration is to bring the system into a very deep
vacuum, below 1,000 microns, to remove
moisture. There are however, certain other
principles which must be observed. These are:
•
Evacuate from 3-points, suction service valve,
discharge service port, and receiver tank outlet
to access both sides of check valves and
solenoids.
•
Always leave service valve caps on during
evacuation and do not exercise the valve stems
while the unit is in a deep vacuum. Packing
glands are prone to leak.
•
Never attempt evacuation without a micron
vacuum gauge. The micron gauge will help
determine:
a. If the pump is capable of pulling a deep
vacuum.
b. When the vacuum pump oil is
contaminated.
c. If the vacuum hoses and valves are leak
free.
d. If the unit is leak free.
e. How long you should evacuate the unit.
f. That the unit is still in a deep vacuum
before any lines are disconnected or
refrigerant is added.
NOTE: The attached evacuation procedures
have been written to be used with the Thermo
King Evacuation System (P/N 204-725).
However, the principles of 3-point evacuation
and the use of a micron gauge during
evacuation should always be practiced.
See the diagram of the Thermo King Evacuation
Station (Figure 191 on page 116) and note the
location of the valves and other components.
Valve #1 (V-1):
Is in the open position when the
pump is running to evacuate the hoses and/or the
unit. When V-1 is closed, the pump has been
isolated from the hoses and/or the unit.
Valve #2 (V-2):
Is in the open position during unit
evacuation. In the closed position, V-2 isolates the
micron gauge and thermistor assembly from the
hoses and/or the unit.
Valve #3 (V-3):
Is in the open position during unit
evacuation. When closed, V-3 isolates the micron
gauge and the vacuum pump from the other
evacuation hoses.
Valve #4 (V-4):
Is in the open position during unit
evacuation. When closed, V-4 isolates the
evacuation hoses and the unit from the evacuation
system.
Iso-Valve
:
Is in the open position when the
vacuum pump is running to evacuate the hoses
and/or the unit. When Iso-Valve is closed, the
pump has been isolated from the hoses and/or the
unit. The Iso-Valve is normally not used because
V-1 performs the same function and is more wear
resistant.
Summary of Contents for UT-1200
Page 10: ...Table of Contents 10...
Page 20: ...Safety Precautions 20...
Page 76: ...Operating Instructions for Premium HMI Control Panel 76...
Page 88: ...Electrical Maintenance 88...
Page 98: ...Engine Maintenance 98 Figure 167 Fuel Components...
Page 142: ...Refrigeration Service Procedures 142...
Page 148: ...Clutch Maintenance 148...
Page 150: ...Structural Maintenance 150...
Page 162: ...Wiring and Schematic Diagrams Index 162...
Page 163: ...163 Schematic Diagram Page 1 of 2...
Page 164: ...164 Schematic Diagram Page 2 of 2...
Page 165: ...165 Wiring Diagram Page 1 of 5...
Page 166: ...166 Wiring Diagram Page 2 of 5...
Page 167: ...167 Wiring Diagram Page 3 of 5...
Page 168: ...168 Wiring Diagram Page 4 of 5...
Page 169: ...169 Wiring Diagram Page 5 of 5...