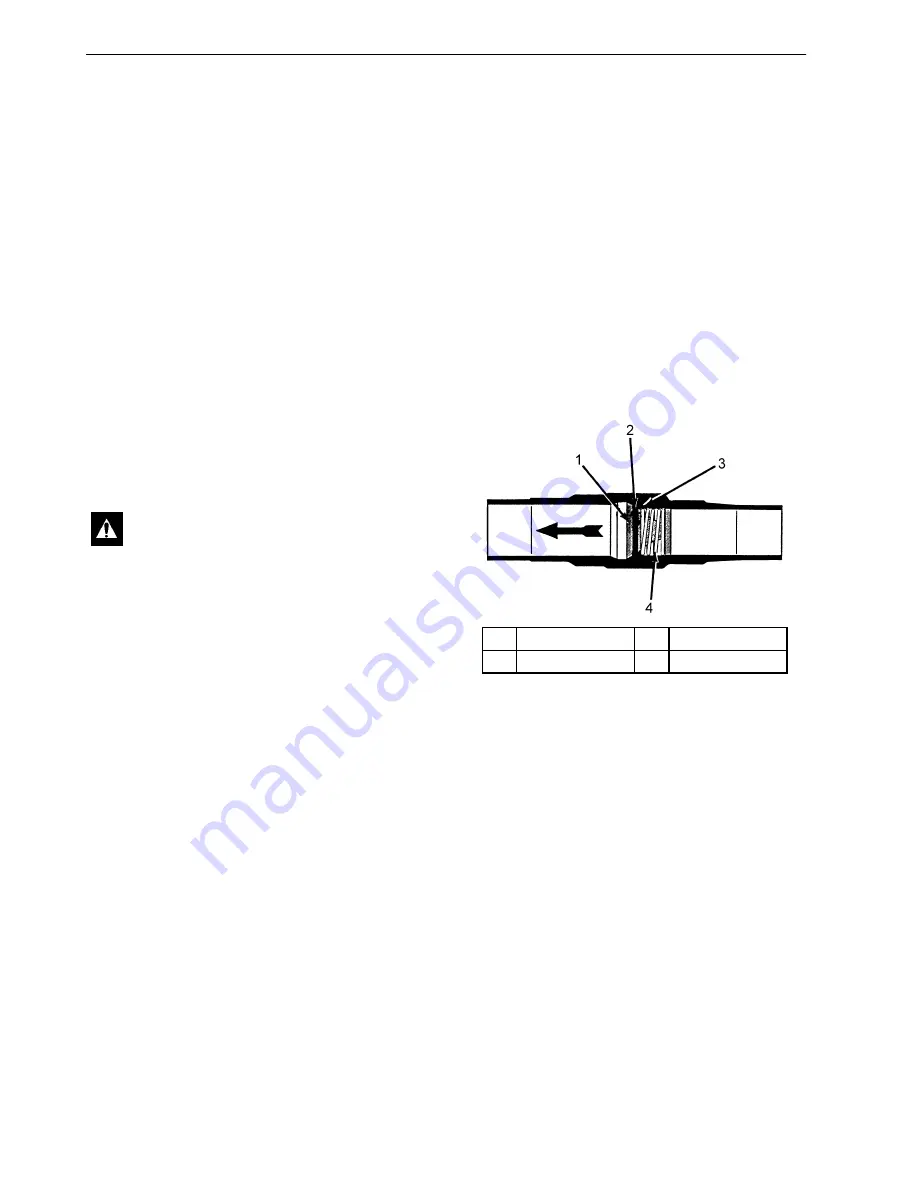
Refrigeration Service Procedures
138
4. If no leaks are found, replace the liquid line
drier then evacuate the
system.
5. Recharge the unit with refrigerant and check
the compressor oil.
6. Verify proper unit operation.
Hot Gas Solenoid (HGS) Test
1. Attach a gauge manifold to the suction service
valve and the discharge service port. Attach
another low pressure gauge to the suction
access port located in the suction line near the
accumulator inlet. Low loss fittings must be
used on the hoses connected to the discharge
service port and the suction access port.
2. Operate the unit in low speed cool.
3. Front seat the receiver tank outlet valve and
allow the low side to pump down to 0 to 5 in.
Hg vacuum (0 to -17 kPa).
4. Turn the unit Off.
5. Front seat the suction service valve to isolate
the low side while it is still in a vacuum.
6. Watch the low pressure gauge attached to the
suction access port. The low side pressure
should not rise. It it does, there could be a leak
through one (or more) of following
components: hot gas solenoid, liquid injection
solenoid, purge valve, or receiver tank
pressure check valve.
7. Check the temperatures of the refrigeration
lines on each side of the HGS by hand. A
temperature difference between the two sides
of the HGS indicates it is leaking.
8. Use the Mechanics/Premium HMI Control
Panel to enter the Interface Board Test Mode.
Refer to the appropriate Microprocessor
Diagnostic Manual for specific information
about the Interface Board Test Mode.
9. From the Interface Board Test Mode select
Hot Gas Solenoid.
10. Momentarily (for approximately 1 second)
energize the HGS with the Interface Board
Test Mode. The low side pressure should rise
slightly. If the low side pressure does not rise,
the HGS is not opening. Check the continuity
of the wiring and the solenoid coil before
assuming the solenoid is faulty.
11. Back seat the receiver tank outlet valve and
the suction service valve. Perform a
“Refrigerant Gauge Removal” procedure.
In-Line Check Valve
Replacement
This unit uses some in-line check valves. An
in-line check valve is not repairable and must be
replaced if it fails. A heat sink must be used on the
in-line check valve when it is being soldered in
place to prevent damage to the neoprene seal.
Removal
1. Recover the refrigerant charge.
2. Place a heat sink on the check valve.
3. Unsolder the refrigeration lines and remove
the check valve.
Installation
NOTE: A heat sink must be used on the in-line
check valve when it is being soldered in place to
prevent damage to the neoprene seal.
1. Clean the tubes for soldering.
2. Place the check valve in position. The arrow
on the valve body indicates the direction of
refrigerant flow through the valve.
3. Place a heat sink on the check valve.
CAUTION: Do not run scroll compressor
in a vacuum for more than 1 minute.
1.
Valve
3.
Valve Seat
2.
Neoprene Seal
4.
Spring
Figure 208: Cross Section of In-line Check Valve
AEA648
Summary of Contents for UT-1200
Page 10: ...Table of Contents 10...
Page 20: ...Safety Precautions 20...
Page 76: ...Operating Instructions for Premium HMI Control Panel 76...
Page 88: ...Electrical Maintenance 88...
Page 98: ...Engine Maintenance 98 Figure 167 Fuel Components...
Page 142: ...Refrigeration Service Procedures 142...
Page 148: ...Clutch Maintenance 148...
Page 150: ...Structural Maintenance 150...
Page 162: ...Wiring and Schematic Diagrams Index 162...
Page 163: ...163 Schematic Diagram Page 1 of 2...
Page 164: ...164 Schematic Diagram Page 2 of 2...
Page 165: ...165 Wiring Diagram Page 1 of 5...
Page 166: ...166 Wiring Diagram Page 2 of 5...
Page 167: ...167 Wiring Diagram Page 3 of 5...
Page 168: ...168 Wiring Diagram Page 4 of 5...
Page 169: ...169 Wiring Diagram Page 5 of 5...